www.konstruktion-industrie.com
12
'22
Written on Modified on
Der 24/7-Einsatz von Robotern in Logistikzentren
Da der globale E-Commerce-Markt weiter wächst – teilweise aufgrund der erheblichen Auswirkungen der durch die Corona-Pandemie verursachten Einschränkungen (Lockdown und die steigende Zahl von Online-Käufen) – nimmt das Versandvolumen erheblich zu.
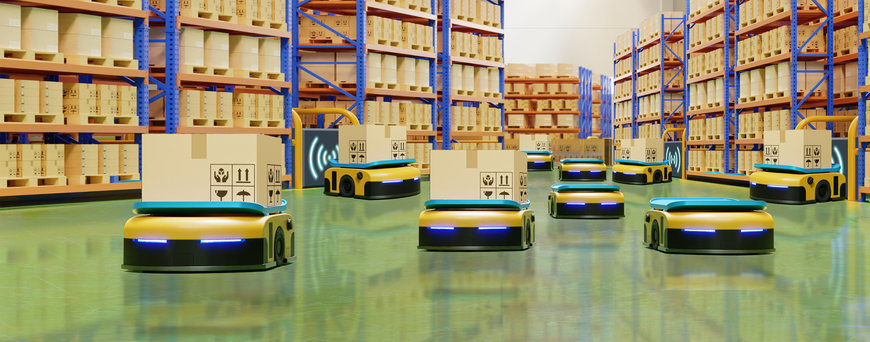
Heute kann jeder rund um die Uhr Waren bestellen, und immer mehr Einzelhändler bieten inzwischen eine Lieferung innerhalb von 24 Stunden nach der Bestellung an. Diese schnelle Abwicklung setzt die Verteilzentren massiv unter Druck und erhöht die Belastung der Mitarbeiter, die schneller arbeiten müssen.
In den kommenden Jahren wird die Zahl der in diesen Verteilzentren umgeschlagenen Güter weiter steigen. Um die Arbeitsqualität zu verbessern, die Sicherheit der Mitarbeiter zu gewährleisten und einen 24-Stunden-Betrieb in Verteilzentren zu ermöglichen, wird dort weltweit zunehmend mehr Automatisierung eingeführt. In diesem Zusammenhang kommen AGVs (Automatic Guided Vehicles) bzw. fahrerlose Transportsysteme (FTS) zum Einsatz, um Pakete zu transportieren.
Ein AGV ist ein Elektrofahrzeug, das ohne großen manuellen Eingriff automatisch auf einer festgelegten Route fahren kann. Als unverzichtbares Element für eine intelligentere Nutzung und Planung zukünftiger Logistikzentren finden AGVs große Beachtung. In den letzten Jahren wurden mit der Integration von IoT- und KI-Technik sogar Modelle eingesetzt, die autonom fahren und Sensoren und spezielle Software verwenden, um Hindernissen auszuweichen. Sie werden als AMRs (Autonome Mobile Roboter) bezeichnet.
Das Problem mit dem Laden
Die tägliche Betriebszeit dieser elektrisch angetriebenen Roboter ist in erster Linie durch die Akkulaufzeit begrenzt. Obwohl sie mit einer bestimmten Geschwindigkeit fahren und Beschleunigungen sowie Abbremsen so gesteuert und programmiert sind, dass sie Energie sparen, müssen sie dennoch aufgeladen werden.
Die meisten Ladepläne für Roboter verwenden eine Kombination aus verbleibendem Ladestand und einem festgelegten Zeitraum, um zu entscheiden, wann der Akku wieder aufgeladen werden soll. Diese herkömmliche Methode funktioniert gut, wenn nur wenige AGVs in einer Anlage betrieben werden. Hier werden jedem Fahrzeug festgelegte Aufgaben zugewiesen, die innerhalb eines bestimmten Zeitrahmens erledigt werden müssen. Ähnlich wie ein Mitarbeiter, der eine Mittagspause einlegt, werden diese Fahrzeuge regelmäßig aufgeladen.
Je nach den Bedingungen vor Ort, kann es beim manuellen Aufladen der Akkus über Kabel zu einer Funkenbildung oder sogar zu schweren Unfällen kommen. Ein Brand in einem Verteilzentrum kann sich schnell ausbreiten und den Betrieb bis zum Löschen aufhalten. Es besteht auch die Gefahr, dass Ware durch Rauch beschädigt oder, noch schlimmer, zerstört wird.
Je mehr Roboter in einem Verteilzentrum eingesetzt werden, desto mehr Wegstrecke ist zurückzulegen, was das Steuerungsmanagement äußerst kompliziert macht. Ist der Akku beispielsweise leer und befindet sich das AGV nicht in der Nähe einer Ladestation, ist ein manueller Batteriewechsel erforderlich. Diese ungeplante Wartung kostet Zeit und Geld und erhöht die Möglichkeit menschlicher Fehler während des Einbaus. Zu bedenken ist auch, dass ein AGV, das außer Betrieb ist, nicht arbeitet, die Produktivität verringert und die Arbeitsbelastung der anderen AGVs in der Einrichtung erhöht.
Ein weiteres Problem, das es zu lösen gilt, besteht darin, dass dieses herkömmliche Ladeverhalten mit dem Übergang auf AMRs allmählich nachlässt. Diese Roboter bewegen sich autonom und setzen selbst Prioritäten für hochwertige Aufgaben, die innerhalb eines bestimmten Zeitfensters ausgeführt werden müssen. Um diese zusätzlichen Probleme zu lösen, muss der Roboter den Ladevorgang adaptiv planen, was die betriebliche Effizienz und Sicherheit verbessert.
Wireless Power – Kabelloses Laden
Die Einführung der kabellosen Energieübertragung (Wireless Power) hat den Vorteil, dass sie ein sequenzielles Laden ermöglicht (Bild 1) und Funkenbildung durch das Anschließen und Trennen an herkömmliche Ladegeräte ausschließt. Sequenzielles Laden bedeutet, dass Akkus während des Betriebs aufgeladen werden, was die Batterielebensdauer des AMR verlängert und die Gesamtarbeitszeit erhöht.
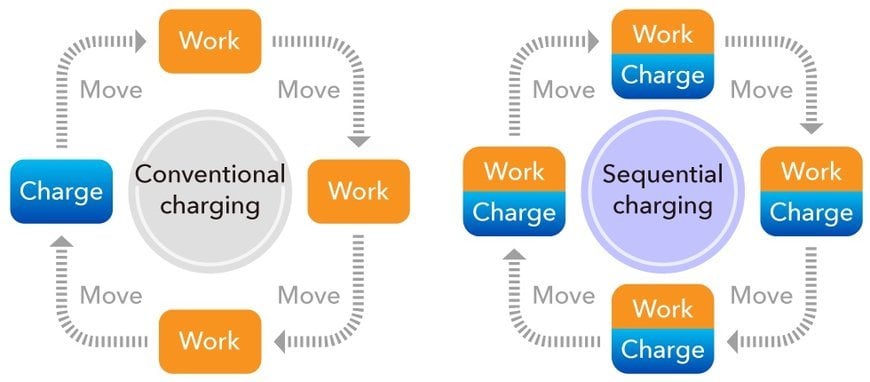
Bild 1: Vergleich zwischen konventionellem und sequenziellem Laden bei mobilen Robotern.
Die Idee für Wireless Power gibt es schon lange. Nikola Tesla und andere Pioniere führten bereits in den 1880er Jahren Experimente zur kabellosen Energieübertragung mittels elektromagnetischer Wellen durch.
Wireless Power lässt sich grob in Strahlung, bei der Energie über Funkwellen (Mikrowellen) oder einen Laser übertragen wird, und in Nicht-Strahlung einteilen, bei der Energie mit Hilfe eines elektrischen oder magnetischen Feldes übertragen wird. Die Strahlungsvariante hat den Vorteil, dass sie über große Entfernungen funktioniert – aber die Energieverluste sind aufgrund von Umgebungseinflüssen groß und daher ineffizient. Im Vergleich dazu reduziert die strahlungslose Methode den Energieverlust so weit wie möglich und bietet daher eine bessere Übertragungseffizienz – aber deren Schwäche besteht darin, dass die Übertragungsstrecke begrenzt ist.
Elektromagnetische Induktion ist seit den 1990er Jahren weit verbreitet, um den Akku von Elektrorasierern und Zahnbürsten zu laden. Zudem sind heute verschiedene Ladepads und Ladestationen erhältlich, die das elektromagnetische Induktionsverfahren zum Laden des Akkus von Mobilgeräten wie Smartphones nutzen. Magnetresonanz ist eine weitere Methode, die aufgrund von Forschungsarbeiten, die 2006 und 2007 am MIT (Massachusetts Institute of Technology) vorgestellt wurden, in der Branche für Aufsehen sorgte.
Magnetresonanz-Laden
Das WPX1000 (Bild 2) ist ein von TDK entwickeltes Wireless-Power-Versorgungssystem der 1-kW-Klasse mit mittlerer Kapazität für AGVs und AMRs, das auf Magnetresonanz basiert. Die Technik überträgt Energie durch Resonanzkreise, die auf der Sende- und Empfangsseite vorgehalten sind. Beide Seiten sind so abgestimmt, dass sie auf der gleichen Frequenz schwingen. Die Technik kann einen zulässigen Spulenversatzbereich von ±30 mm in Fahrtrichtung des AGV/AMR und einen Abstand von 20 bis 40 mm zwischen leistungsübertragenden Spulen erreichen, was den Stromübertragungsbereich erweitert. Auf eventuelle Spulenverschiebungen wird reagiert, und die Technik eignet sich optimal für sequenzielles Laden.
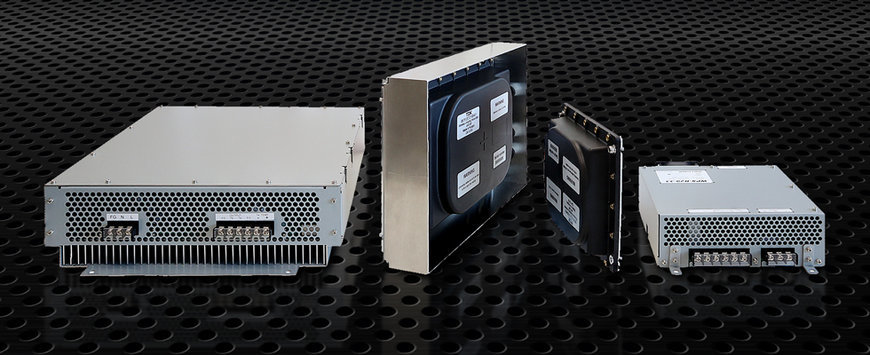
Bild 2: Das Wireless-Power-Versorgungssystem WPX1000 für AGVs.
Da die Spuleneinheit sowohl auf der Stromübertragungs- als auch auf der Stromempfangsseite staubdicht und tropfwassergeschützt nach IP65 ausgeführt ist, eignet sich dieses kabellose Ladegerät für den Einsatz in rauen Innen- und Außenumgebungen. Zudem ermöglicht die zum Laden des Akkus optimale Konstantspannungs-/Konstantstromregelung (CV-CC-Regelung) das direkte Laden des Akkus. Die integrierte serielle Kommunikation (RS-232) ermöglicht die Regelung des Ladespannungs-/Ladestromwerts.
Alternative kabellose Energieübertragung
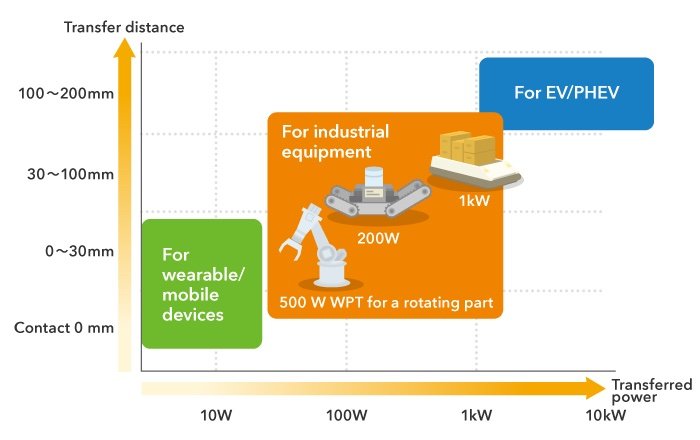
Bild 3: Kabellose Stromversorgungs-/Ladelösungen von TDK.
Neben der kabellosen Energieübertragung mittels Magnetresonanz hat TDK ein elektromagnetisches Induktionsverfahren entwickelt. Diese Technik wird hauptsächlich für tragbare und mobile Geräte verwendet. TDK bietet kabellose Ladesysteme für Mobilgeräte und industrielle Systeme mit mittlerer Leistung an. Das Unternehmen arbeitet auch an der Entwicklung von Hochleistungssystemen für Elektrofahrzeuge (EV/PHEV, Bild 3). Der Kern dieses umfangreichen Angebots ist die Ferrit-Technologie, die die Grundlage von TDK bildet. Ferrit ist das Kernmaterial der Sende-/Empfangsspule, dessen Eigenschaften einen wesentlichen Einfluss auf die Übertragungseffizienz einer kabellosen Stromversorgung hat.
www.tdk.com