www.konstruktion-industrie.com
31
'20
Written on Modified on
Wie die additive Fertigung das disruptive Potenzial erschließt
Die additive Fertigung verändert nicht nur die industrielle Fertigung. Sie leistet auch einen Beitrag zur nachhaltigen Entwicklung.
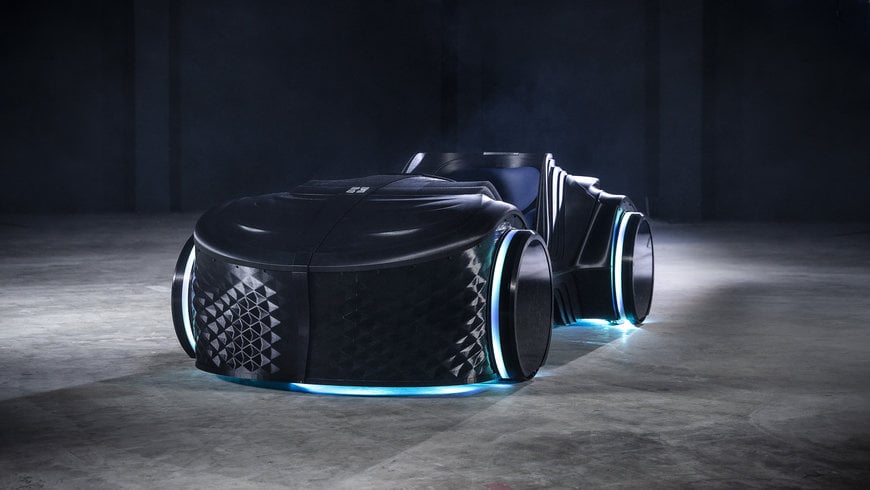
Die additive Fertigung – im B2C-Bereich als 3D-Druck bekannt – wird oft als die disruptivste Produktionstechnologie der Gegenwart bezeichnet, die ganz erhebliche Auswirkung auf die Zukunft der industriellen Produktion haben wird. Bereits Anfang der 1980er Jahre erfunden, ist ihre Marktdurchdringung in den letzten Jahren stark gewachsen. Zu den Gründen dafür gehört neben der Weiterentwicklung der AM-Verfahren selbst auch die Konvergenz diverser Technologien im digitalen Zeitalter.
Noch vor wenigen Jahren wurde die additive Fertigung nahezu ausschließlich für die schnelle Herstellung von Prototypen verwendet. Inzwischen gilt sie in vielen Bereichen der Industrie als Patentlösung, die jederzeit und (fast) überall umsetzbar ist. Anders als bei der konventionellen „subtraktiven“ Fertigung, bei der Material z.B. durch Fräsen, Drehen oder Schleifen abgetragen wird, trägt man bei der additiven Fertigung schichtweise Material auf, um ein Objekt zu formen. Dabei kommen verschiedene Verfahren zum Einsatz, und das Spektrum der Werkstoffe reicht von diversen Kunststoffen und Metallen über Keramik bis hin zu Biochemikalien, die in medizinischen Implantaten Anwendung finden.
Vorteile: Leichtbau und Funktionsintegration
Einer der wichtigsten Vorteile der additiven Fertigung ist, dass maßgeschneiderte Teile – sei es das verlorene Rad eines Spielzeugautos oder der Reifen eines Marsrovers – zu relativ kostengünstigen Preisen in „Stückzahl Eins“ hergestellt werden können. Außerdem können Konstruktionen mit komplexen Geometrien gefertigt werden, die sich durch geringes Gewicht und zugleich hohe Belastbarkeit auszeichnen.
Ein bekanntes Beispiel ist die von GE entwickelte und im 3D-Druck produzierte Kraftstoffdüse für das LEAP-Triebwerk. Die zuvor aus 20 Teilen zusammengebaute komplexe Düse mit der Größe einer Walnuss wird jetzt in einem Teil produziert. Sie wiegt 25% weniger als das konventionell gefertigte Vorgängermodell, ist 30% kostengünstiger und ihre Lebensdauer beträgt das Fünffache.
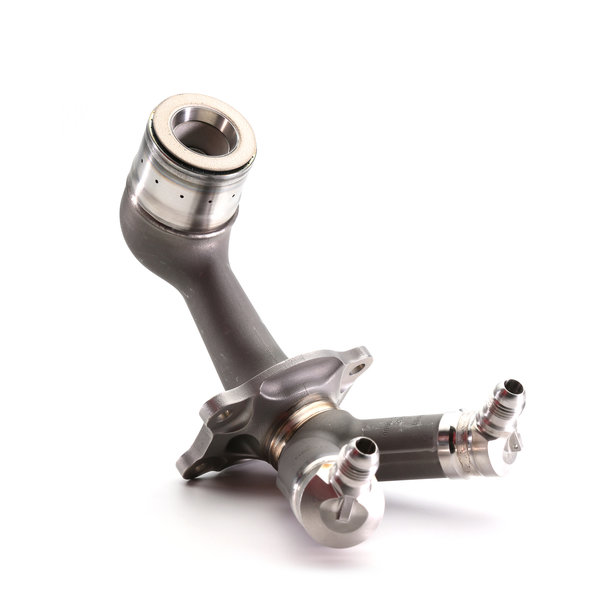
Janne Kyttanen, 3-D-Visionär und Erfinder von 3DTI – der allerersten 3D-Druck-Technologie für die „Mass Customisation“ –, zufolge sind Anwendungen der additiven Fertigung lediglich durch (fehlende) Kreativität Grenzen gesetzt.
Nachteile: Hohe Anfangsinvestitionen, hohe Fertigungskosten
Das Verfahren der additiven Fertigung bringt jedoch nicht nur zahlreiche Vorteile, sondern auch einige Nachteile mit sich. Der größte Nachteil sind – wenn man die Anlagen selbst betreibt – die hohen Anfangsinvestitionen sowie die Betriebsausgaben. Letztere entstehen durch die hohen Kosten des Materials, das in den meisten Fällen von Hardware-Herstellern geliefert wird und an OEM-Verträge gebunden ist. Das erschwert eine Massenproduktion insbesondere von großen Teilen. Hier spricht die Wirtschaftlichkeitsberechnung ganz klar für die konventionellen Verfahren.
Bei besonderen Anforderungen bietet die additive Fertigung jedoch auch bei großen Bauteilen erhebliche Vorteile – zum Beispiel bei Kfz-Sitzkonsolen, mit denen die Sitze und Gurte an der Karosserie befestigt werden. General Motors hat die neueste Generation dieser Komponenten mit Autodesks AM-CAD-Programm entwickelt. Zuvor wurde ein kastenförmiges Teil aus acht Teilen zusammengeschweißt, heute wird die schlanke Verankerung aus Edelstahl 3-D-gedruckt. Das neue Teil ist nicht nur 40 % leichter, sondern auch 20 % stärker und zudem günstiger in der Herstellung, weil weniger Anbieter involviert sind und die Schweißarbeiten entfallen.
Da überrascht es kaum, dass alle Automobilhersteller inzwischen in additive Fertigungstechniken investieren, um die Entwicklung zu optimieren und Kosten zu sparen. Ein durchschnittliches Auto besteht aus 30.000 Teilen und zahlreiche davon können im 3-D-Druck hergestellt werden.
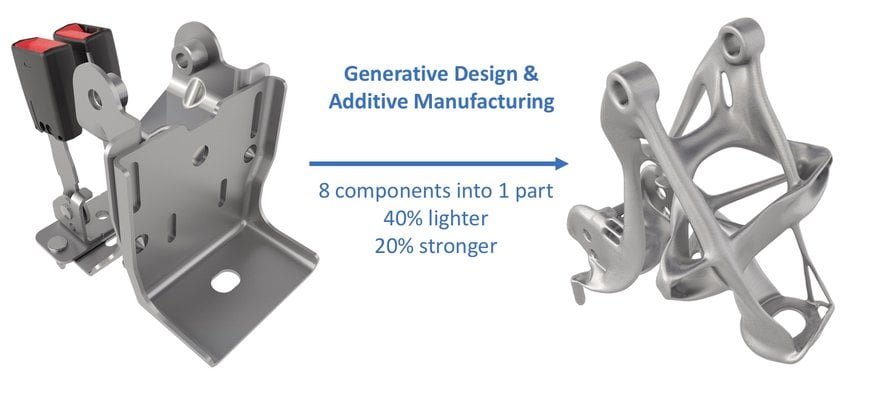
3D-gedruckte Sitzkonsole für Fahrzeuge von General Motors
Rückblick auf die formnext 2019
Im November 2019 fand in Frankfurt die formnext statt: Europas größte Fachmesse für additive Fertigung. Führende Unternehmen wie 3D Systems, Addup, BigRep, DMG Mori, EOS, Formlabs, GE Additive, HP, Markforged, Renishaw, Siemens, Stratasys und Voxeljet stellten dort ihre Innovationen vor.
GE Additive, Teil von GE und weltweiter Marktführer und Vorreiter in der additiven Fertigung, präsentierte unter anderem den Arcam EBM Spectra L. Dieser 3-D-Metalldrucker ermöglicht eine höhere Produktionsgeschwindigkeit und bietet zudem zahlreiche Automatisierungsfunktionen. Nach Angaben des Herstellers senkt er die Bauteilkosten um rund 10%, und durch die Strahlleistung von 4,5 kW wird die Baugeschwindigkeit im Vergleich zum Arcam EBM Q20plus um 20 % gesteigert.
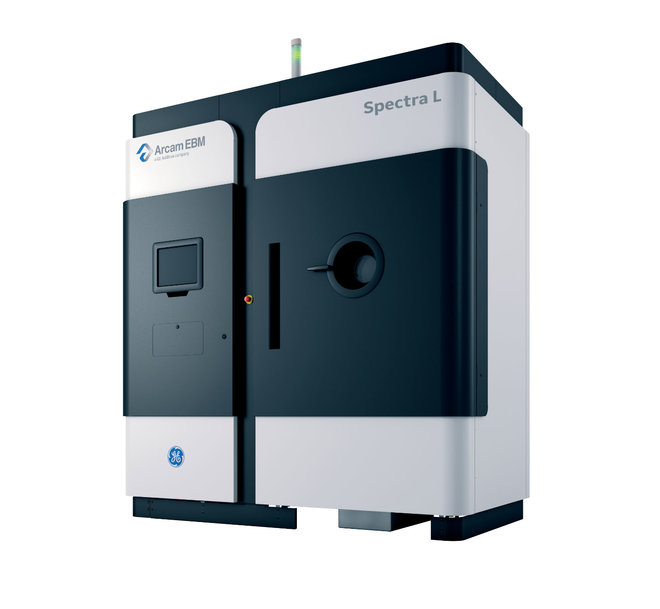
Außerdem führte das Unternehmen kürzlich den Concept Laser M2 Serie 5 für den Metalldruck ein. Er erfüllt höchste Erwartungen in Sachen Qualität und Reproduzierbarkeit und adressiert Anwender in streng regulierten Sektoren wie der Luftfahrt- und der Medizinindustrie.
BigRep, Entwickler des weltweit größten in Serienproduktion hergestellten 3-D-Druckers, präsentierte stellte mit LOCI ein vollständig 3-D-gedrucktes Konzept für autonome elektrische Podcars vor. Der LOCI-Prototyp wurde als Last-Mile-Transportlösung im städtischen Raum entwickelt und soll an Flughäfen und Bahnhöfen, auf Pendelstrecken und als Campus-Verkehrsmittel für lokale Lieferungen eingesetzt werden soll.
Auf Grundlage der parametrischen Modellierung entwickelt, schöpft LOCI das Potenzial der additiven Fertigung aus. Das Design des Podcars kann einfach auf einen bestimmten Standort oder eine Anwendung zugeschnitten werden. Auch Spezialräder für unterschiedliche Untergründe und ein integrierter Solarbetrieb sind möglich. Auf der Formnext stellte das Unternehmen mehrere LOCI-Varianten vor - vom kompakten Einpersonen-Pendelfahrzeug bis zum Zubringerfahrzeug mit Luxusausstattung, Solarmodulen und robuster Bereifung.
Ein weiteres Exponat von BigRep war das fahrerlose Transportfahrzeug NEXT AGV, das in Zusammenarbeit mit Bosch Rexroth entwickelt wurde und in der intelligenten Fabrik genutzt werden soll. Es wird von einer induktiven, netzabhängigen Energieeinheit angetrieben, kann als automatisiertes Logistikfahrzeug betrieben werden und besitzt eine Ladekapazität von bis zu 250 kg. Auf der Plattform lassen sich Werkzeuge und zusätzliche Geräte wie Roboter montieren. Mit den 3-D-gedruckten Rädern aus zwei verschiedenen Werkstoffen kann sich die Plattform auch seitwärts bewegen.
3D Systems wurde 1983 von Chuck Hull, dem Erfinder des 3-D-Drucks, mitbegründet. Das Unternehmen stellte auf der Formnext 2019 neue Anlagen für die AM-Fertigung und beispielhafte Produkte vor – unter anderem ein Metall-Funktionsbauteil für ein Flugzeug, das mit Hilfe von additiven Technologien, herkömmlicher Metallbearbeitung und innovativen Software-Lösungen in reproduzierbarer Qualität zu geringeren Stückkosten hergestellt werden kann.
Bei diesem Projekt kommt auch die strategische Partnerschaft mit GF Machining Solutions im Bereich der Präzisionsbearbeitung zum Tragen. Diese Kooperation ermöglicht die nahtlose Verknüpfung additiver und subtraktiver Technologien, um mit hoher Effizienz komplexe Metallteile mit geringer Fehlertoleranz zu produzieren und die Gesamtbetriebskosten zu verringern.
Als ein weltweit führender Technologieanbieter von industriellen Metall- und Polymer-3D-Drucken zeigte EOS in Frankfurt erstmals seine „Fine Detail Resolution“-Technologie (FDR) für die Polymerverarbeitung. EOS entwickelte als erster Hersteller eine Lösung für pulverbasierte industrielle 3-D-Drucke mit einem CO-Laser. So können sehr empfindliche und dennoch robuste Teile mit Oberflächen mit einer hohen Detailauflösung und einer Mindestwandstärke von nur 0,22 mm hergestellt werden.
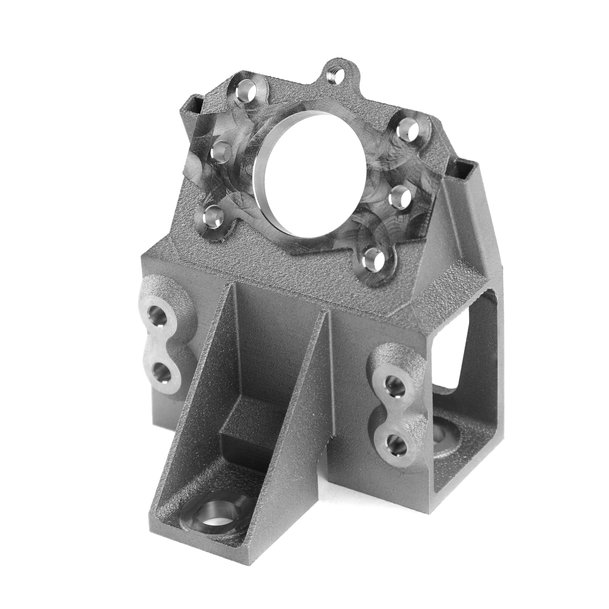
Von 3D Systems entwickelte hybride Flugzeughalterun
Bei der Auswahl der richtigen 3-D-Drucktechnologie von EOS für die Polymerverarbeitung steht der Industrie eine noch breitere Vielfalt zur Verfügung. Die FDR-Technologie verbindet die Vorteile zweier Welten miteinander: die Detailauflösung der Stereo-Lithographie (SLA) und die Haltbarkeit und Qualität des selektiven Lasersinterns (SLS). Das eröffnet Möglichkeiten für ganz neue Anwendungen der additiven Fertigung in Kunststoff, beispielsweise für Filteranlagen und Komponenten der Fluidtechnik sowie für Konsumgüter wie beispielsweise Brillen.
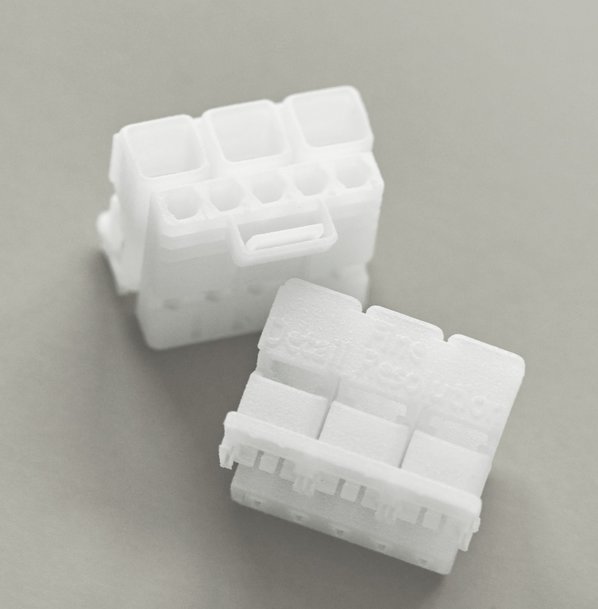
Neuheiten aus dem Bereich der Werkstoffe gibt es von Essentium. Das Unternehmen gab die Einführung von Hochtemperaturwerkstoffen (HT) und von neuen Varianten der Essentium High Speed Extrusion (HSE)-Druckplattform bekannt.
Die Düsentemperatur des neuen HSE 180 S HT erreicht 550 °C. Die produzierten Bauteile halten Temperaturen von 180 °C stand. Damit hat es Essentium geschafft, additive Fertigungsmethoden für Hochtemperaturwerkstoffe zu entwickeln, ohne Faktoren wie Geschwindigkeit, Stabilität und Wirtschaftlichkeit zu beeinträchtigen. Damit hat das Unternehmen das Potenzial der industriellen additiven Fertigung erweitert.
Außerdem stellte Essentium vier neue Werkstoffe für den 3d-Druck vor: PEEK, Hochtemperaturnylon (HTN), HTN-CF25 und HTN-Z (ESD-leitfähig). Sie gewährleisten in industriellen Anwendungen eine hohe Hitze-, Chemikalien- und Ermüdungsbeständigkeit sowie hohe mechanische Resistenz.
Zudem kündigte Essentium seine Absicht an, die Software Materialise 3D Printing Magics Essentials in die HSE-3-D-Drucker zu integrieren. Damit stellt das Unternehmen eine offene und umfassende Suite mit einem End-to-End-Workflow bereit.
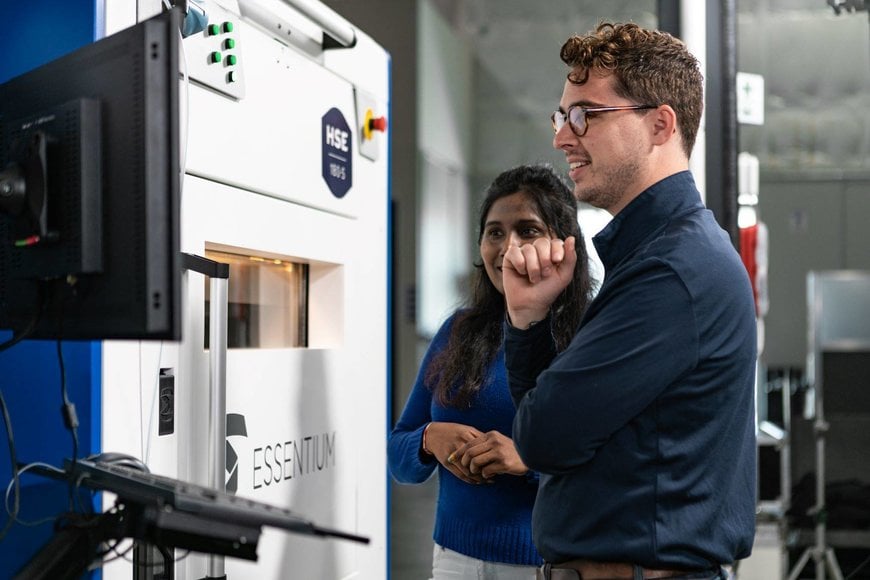
Renishaw führte mit InfiniAM Sonic ein Programm zur akustischen Prozessüberwachung des AM-Prozesses ein. Mit diesem Tool können Ingenieure akustische Ereignisse in der Baukammer des AM-Gerätes ermitteln und daraus nützliche Informationen über die Prozess- und Bauteilqualität ableiten. Die Software ist im Sektor der additiven Fertigung die erste ihrer Art. Das Paket wird auf der Anlage RenAM 500Q als werksseitige Option installiert. Vier Sensoren detektieren Vibrationen in der Kammer. Mit vier 500-W-Hochleistungslasern erreicht die Anlage hohe Produktivitätsraten. Da die Laser auf der gesamten Bauplatte arbeiten und so gesteuert werden, dass die Interaktion mehrerer Laser nicht die Verarbeitungsqualität beeinträchtigt, ist für maximale Effizienz gesorgt.
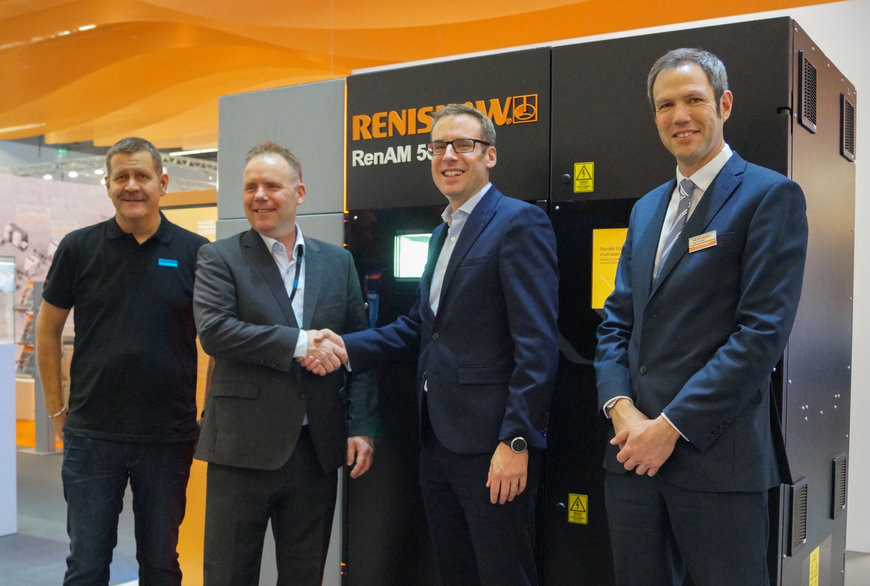
Gemeinsam mit Sandvik Additive Manufacturing arbeitet Renishaw daran, neue Materialien für Produktionsanwendungen in der additiven Fertigung zu entwickeln. Dazu gehören neue Legierungszusammensetzungen von Metallpulvern, die für das selektive Laserschmelzen (SLM oder Laser Powder Bed Fusion) optimiert wurden.
Wenn 3-D-Drucker ein Objekt durch Scannen und Drucken reproduzieren, bestehen jedoch auch Sicherheitsrisiken. Ein Schlüssel kann ganz leicht abfotografiert oder gescannt und als Duplikat gedruckt werden. Dieses Risiko wird mit einer Innovation ausgeschlossen, die zum Abschluss der formnext mit dem ersten Preis der „Purmundus Challenge“ ausgezeichnet wurde. Beim 3-D-gedruckten „Stealth Key“ der UrbanAlps AG aus der Schweiz handelt es sich um einen physischen Schlüssel und ein Zylindersystem, in denen der Code sicher unter schmalen, robusten Leisten versteckt ist. Da der rein mechanische Schlüssel nicht gescannt werden kann, bietet er maximale Sicherheit und keine Angriffsfläche für unerlaubtes Duplizieren.
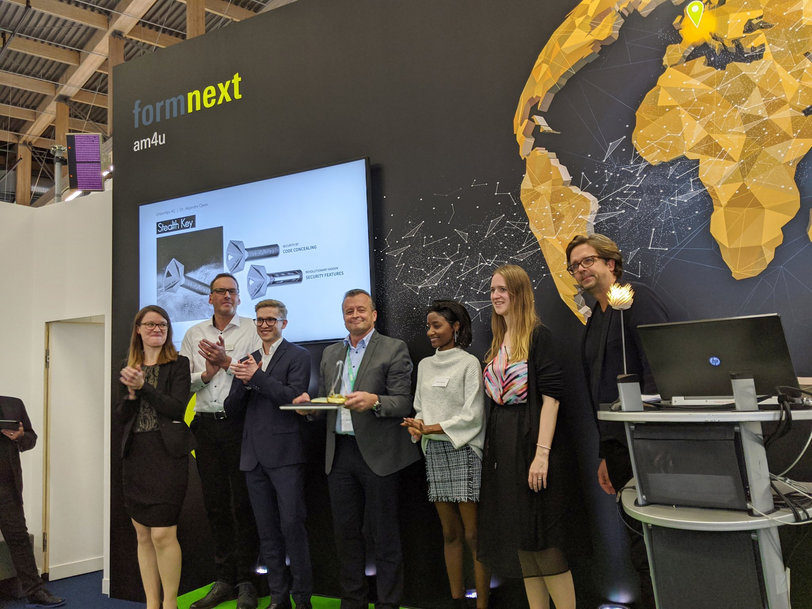
Der 3D-gedruckte Stealth Key erhielt den ersten Preis bei der Purmundus Challenge
Der Weg in die Zukunft
Die wachsende Sorge um die Umweltzerstörung und den Klimawandel hat auch die Industrie erfasst. „Nachhaltigkeit“ lautet das neue Mantra, „Klimaneutralität“ das neue Ziel. Laut den Vereinten Nationen streben nun mehr als 60 Länder danach, bis 2050 klimaneutral zu werden. Mitte 2019 erklärte Bosch, das Unternehmen werde schon in diesem Jahr – 2020 – komplett klimaneutral produzieren. Auch viele andere Unternehmen arbeiten nach eigenen Zeitplänen auf dasselbe Ziel hin.
Diese Entwicklung spricht dafür, dass der 3-D-Druck insbesondere in der Mobilität eine bedeutendere Rolle spielen wird. Denn hier ist es ein wesentliches Ziel, das Gewicht der Verkehrsmittel auf dem Land, zu Wasser und in der Luft zu reduzieren. Additive Fertigung bietet die (Leichtbau-)Technologie, mit der sich dieses Vorhaben umsetzen lässt. Das Beispiel der Sitzkonsole von General Motors wurde schon erwähnt. Das Autodesk-Programm Fusion 360 schlug mehr als 150 verschiedene Entwürfe vor, aus denen das optimale Design ausgewählt wurde. Autodesk und BMW arbeiten jetzt daran, mithilfe von generativen Gestaltungstechnologien und Methoden der additiven Fertigung einen neuen Fahrzeugtyp zu entwickeln, der Gewicht spart und sich schneller und günstiger produzieren lässt.
Die Kombination aus generativer Gestaltung und additiver Fertigung kommt aber auch über die Mobilität hinaus in vielen anderen Bereichen zum Einsatz – zum Beispiel in der Architektur, in Industriemaschinen, Konsumgütern und in der Medizin. In all diesen Bereichen birgt die Technologie ebenfalls hohes Potenzial, da sie die Produktivität steigert, Energie spart, neue Konstruktionsweisen ermöglicht und auch das Realisieren neuer Geschäftsmodelle (individualisierte Produkte, „Print on demand“ von Ersatzteilen…) erlaubt.
Apropos Material: Die additive Fertigung setzt sich auch im Lebensmittelsektor, besonders bei Konditoreiwaren, durch. Kuchen und Schokolade können jetzt per 3-D-Druck mit originellen und ansprechenden Designs in die gewünschte (oft individuelle) Form gebracht werden.
Angesichts der schnellen Entwicklung und der höheren Wirtschaftlichkeit aufgrund immer günstigerer Hardware und Werkstoffe wird der Anteil des 3-D-Drucks im Vergleich zu konventionellen Produktionsverfahren in den kommenden Jahren weiter wachsen. Von Torten und Schuhen bis hin zu Podcars und Raumschiffen revolutioniert diese Technologie die Konstruktions- und Produktionsmethoden und ebnet somit den Weg für eine spannende, nachhaltige Zukunft.
••• Bruno FORGUE
Fordern Sie weitere Informationen an…