www.konstruktion-industrie.com
27
'20
Written on Modified on
PNEUMATISCHE AUTOMATISIERUNGSTECHNIK: FLEXIBEL, ATTRAKTIV UND KOSTENGÜNSTIG
Die Pneumatik ist eine altbekannte Teildisziplin der industriellen Automatisierungstechnik. Sie ist einfach aufgebaut und vielseitig und bietet im Technologievergleich einige Vorteile, die sich vor allem aus den Eigenschaften ihrer Energiequelle – der Druckluft – ergeben. Sicherheit, geringe Betriebskosten, einfache Implementierung und hohe Kostenffizienz sind wichtige Gründe dafür, dass viele europäische Industrieunternehmen auf Pneumatik setzen, wenn sie Automatisierungslösungen benötigen.
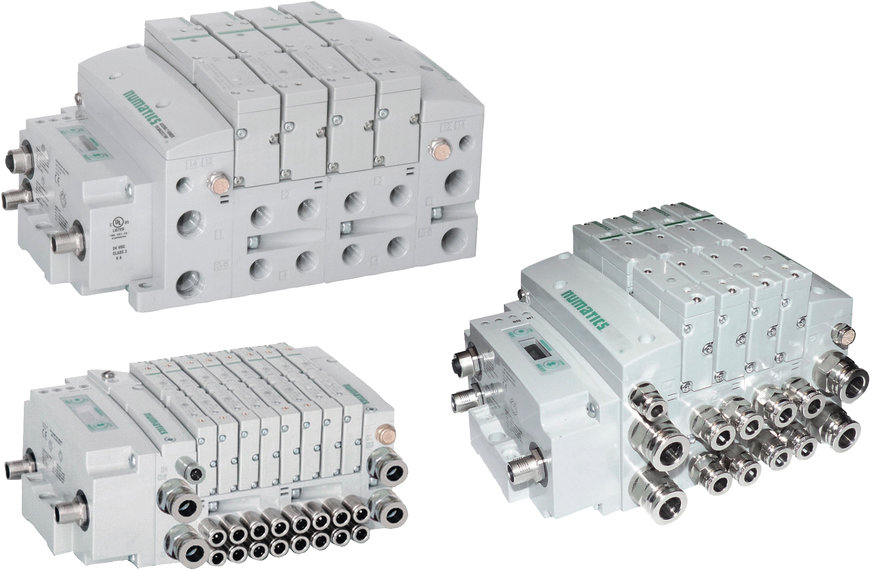
Leonardo Brand, Engineering Supervisor von ASCO-EMERSON: “Aus Sicht vieler Anwender punktet die Pneumatik mit ihrer Vielseitigkeit und den günstigen Kosten. Insbesondere in der Automobilindustrie und der Massengüterproduktion in anderen Industriebereichen ist die Pneumatik erste Wahl, wenn es um Automatisierungsprojekte geht. Aber auch in vielen anderen Anwendersparten ist diese Haltung weit verbreitet – zum Beispiel im Bergbau, in der Metallurgie, in Chemie und Petrochemie sowie in der Papierindustrie.”
Nach Angaben von Brand ist die Prozessindustrie der Hauptzielmarkt von Asco-Emerson für die pneumatische Automation. “Dazu gehören für uns Chemie, Bergbau, Pulp & Paper, Medizintechnik, Energieerzeugung und die Ölindustrie. In diesen Anwendungsbereichen haben wir umfassendes Know-how und können den Kunden sehr ausgereifte und leistungsfähige Automationslösungen vorschlagen.“
Nach Brand ist besonders der Bergbau ein interessanter Einsatzbereich, hier insbesondere die Prozesskette der Abwasserbehandlung. Dort ist der Einsatz von pneumatischen Zylindern, Wegeventilen und Luftaufbereitungseinheiten weit verbreitet.
Ein weiterer Anwendungsschwerpunkt ist die Reifenproduktion, vor allem die Steuerung von Autoklaven. Ventilinseln und elektronische Druckregelventile gehören hier zu den Standardkomponenten der pneumatischen Automation. Und in der gesamten Chemieindustrie – vor allem beim Handling von flüssigen Medien – kommen intelligente Ventilinseln und Druckluft-Wartungseinheiten zum Einsatz.
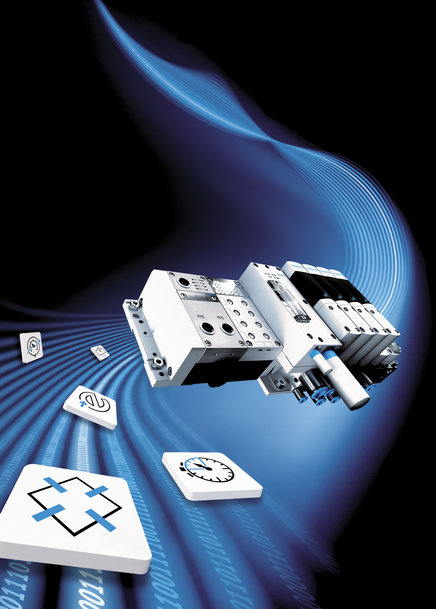
Osvaldo Tomio Sato, Produktmanager bei FESTO, hebt ebenfalls hervor, dass die Pneumatik in der Industrie nahezu universell eingesetzt wird: “Den Anwendungen sind kaum Grenzen gesetzt. Typische Beispiele sind Linearbewegungen in Verpackungsmaschinen, das Positionieren von Werkstücken in Werkzeugmaschinen, der Teiletransport in der Automobilproduktion, das Greifen von Bauteilen in der Elektrik-/ Elektronikproduktion, das Produzieren von Dispensern in der Pharmaindustrie, das Öffnen und Schließen der Türen von Bussen und Bahnen sowie das Schüttgut-Handling in der Lebensmittelindustrie.“
Dabei treibt Festo den Einsatz pneumatischer Antriebe in diversen Anwenderbereichen weiter voran. Sato: “In der Lebensmittelindustrie befassen wir uns zum Beispiel mit Nischenanwendungen wie der Fleischproduktion einschließlich des Gefrierens, der Produktion von Schokokolade und Konfekt sowie von Milchprodukten. Hier kann Pneumatik aufgrund ihrer Vielseitigkeit gut eingesetzt werden – zum Beispiel beim Transport und Handling, aber auch bei der Verpackung und Inspektion von Lebensmitteln. Dabei werden häufig auch die Produktivität und der Hygienestandard verbessert. Denn die hier eingesetzten pneumatischen Automationskomponenten sind als ‘Clean Design’ klassifiziert, und zentrale Baugruppen wie Rohre, Rohrverbinder, Aktuatoren und Ventilinseln werden aus Werkstoffen gefertigt, die den FDA-Anforderungen entsprechen.“
PNEUMATIK UND INDUSTRIE 4.0
Flexibilität, einfacher Aufbau und günstige Kosten sind nach Ansicht von Leonardo Brand (Asco) zentrale Vorteile der pneumatischen Automation. „Man muss allerdings zugeben, dass es Prozesse gibt, bei denen die Installation eines effizienten Pneumatiksystems mit Luftspeichern und –verteilung schwierig ist, weil die dafür nötige Infrastruktur fehlt. In diesen Fällen ist es einfacher, auf Elektroautomation zu setzen statt zunächst Idealbedingungen für die Pneumatik herzustellen.“
Brand fügt hinzu, dass es aber auch genug Unternehmen gibt, die bereits mit einem “State of the art”-System zur Druckverteilung ausgerüstet sind. Bei ihnen, so seine Empfehlung, sollten pneumatische Automationssysteme z.B. für das Handling, Positionieren und Bearbeiten von Bauteilen nicht durch elektrische Automation ersetzt werden – ganz einfach weil solche Systeme drei- bis viermal teurer sind als pneumatische, die dieselben Funktionen erfüllen.
Darüber hinaus, so Brand weiter, zeichnet sich die Pneumatik durch ihre Fähigkeit aus, ohne besonderen Schutz in industrieller Umgebung zu arbeiten. „Im Unterschied dazu muss die elektrische Ausrüstung immer geschützt werden – zum Beispiel gegen Feuchtigkeit, Vibrationen, Hitze und Elektromagnetismus. Der Pneumatik machen solche Umgebungsbedingungen nichts aus.”
Häufig stellen potenzielle Anwender die Frage: Lässt sich die pneumatische Automation vollständig in die modernen industriellen Prozesse integrieren? Leonardo Brand bejaht die Frage ohne Wenn und aber: “Die Pneumatik eignet sich zum Beispiel für die Integration in Feldbusprotokolle sowie in diverse Systeme zur Sammlung und Auswertung von Daten – und das seit 15 Jahren. Heute ist sie bereit, zusammen mit anderen Systemen in Industrie 4.0-Umgebungen zu migrieren. Dazu leisten etwa smarte Ventilinseln mit IO-Link einen wesentlichen Beitrag.“
Osvaldo Tomio Sato hebt hervor, dass pneumatische Automation immer einfach aufgebaut ist. “Druckluft gehört zu den ältesten vom Menschen genutzten Energiequellen. Sie wird aus atmosphärischer Luft gewonnen, die überall und unbegrenzt zur Verfügung steht. Es ist einfach, daraus Druckluft zu erzeugen, und auch die Instandhaltung birgt keine großen Herauforderungen. Wegen des relativ simplen Aufbaus zeichnen sich auch die Automationssysteme selbst durch sicheren und zuverlässigen Betrieb aus.“
Zu den Zielen der pneumatischen Automation gehörte es immer, menschliche Arbeit bei Wiederholaufgaben zu ersetzen und damit sowohl die Produktivität zu steigenr als auch die Produktionskosten zu senken. Der Mensch, so der Grundgedanke, soll Aufgaben übernehmen, in denen er seine Intelligenz und Anpassungsfähigkeit besser ausspielen kann – zum Beispiel in der vorbeugenden Instandhaltung, beim Programmieren und Parametrieren sowie bei der Verbesserung von Prozessen. Damit trägt die Pneumatik dazu bei, dass die industrielle Produktion auch in Hochlohnstandorten wettbewerbsfähig bleibt.
Sato weist darauf hin, dass sein Unternehmen kontinuierlich das Systemangebot für die pneumatische Automation erweitert – aktuell zum Beispiel um das Motion Terminal VTEM. „Dieses Terminal nutzt das Konzept der digitalisierten Pneumatik, indem es die Vorzüge von Elektrik und Pneumatik vereint und einen leistungsfähigen Software-Controller verwendet. Damit ist ein hoch innovatives Produkt entstanden. Es ermöglicht eine Vielzahl von Funktionen, für man sonst mehr als fünfzig individuelle Komponenten benötigen würde.”
Das Motion Terminal, so Sato weiter, ist einzigartig, weil es mit einem einzigen Ventil eine solche Bandbreite an Funktionen abdecken kann. Dabei wird es über ‘Motion Apps’ gesteuert, deren Parameter in Echtzeit verändert werden können: “In einem Produkt und auf einer Plattform haben wir hier alle Aspekte realisiert, die erforderlich sind für die Anforderungen von Industrie 4.0: Flexibilität, Energieeffizienz und Selbstüberwachung. Damit ist VTEM das ideale Produkt für die industrielle Automation der Zukunft. Denn die digitale Pneumatik beschleunigt Automatisierungsprozesse von der Planung über die Konstruktion bis zur Realisierung und Parametrierung. Und die Produktivität im Betrieb wird durch die Fähigkeit gesteigert, das System ganz schnell und einfach an veränderte Anforderungen anzupassen.“
Somit lässt sich festhalten: Pneumatische Automation ist nicht nur bestens etabliert, sondern auch gut vorbereitet auf die Integration in IIoT- und Industrie 4.0-Umgebungen. Sie zeichnet sich dabei durch einfachen Aufbau und nahezu unbegrenzte Anwendungsmöglichkeiten aus.

ELEKTRONIK-PLATFORM DER SERIE 580 JETZT AUCH MIT IO-LINK
ASCO-EMERSON bietet die Elektronikkomponenten der Serie 580 – die kompatibel mit den Ventilinseln der Serien 501, 502 und 503 sind – jetzt mit integrierter IO-Link-Anbindung an.
Über den IO-Link-Standard (CEI 61131-9) wird eine ebenso einfache wie intelligente Verbindung von Input-/ Output-Endgeräten (d.h. von Sensoren und Aktoren) zu einem Steuergerät hergestellt – über kostengünstige und ungeschirmte Standardleitungen. Außerdem kann der Anwender über IO-Link Diagnose- und Konfigurationsparameter wiederherstellen.
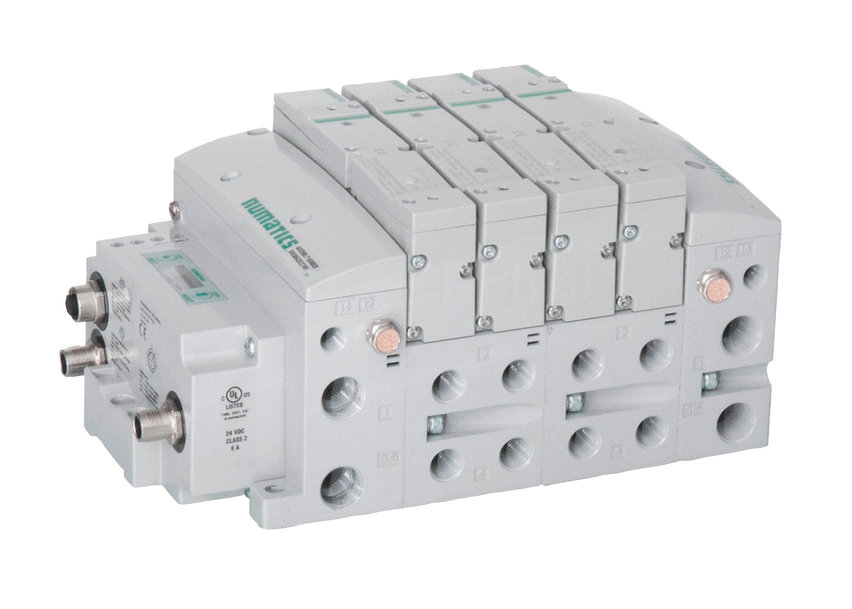
Hauptvorteile
Zu den wesentlichen Vorteilen der IO-Link-Anbindung gehört die Übereinstimmung mit dem internationalen Standard CEI 61131-9. Dadurch ist die Interoperabilität (Kommunikation unter den angeschlossenen Teilnehmern) gewährleistet .Und dass IO-Link den digitalen Datenaustausch von den Feldgeräten zur Steuerung ermöglicht, gibt dem Anwender die Möglichkeit, die Produktivität der jeweiligen Anlage zu steigern.
Ein weiterer Vorteil ist der deutlich verringerte Instandhaltungsaufwand, denn IO-Link-Komponenten werden im Falle eines Austauschs automatisch identifiziert und konfiguriert. Weitere Zeitersparnis ergibt sich u.a. daraus, dass ASCO Numatics 580 IO-Link eine Input-/ Output-Diagnose bereitstellt, die sehr einfach programmiert werden kann. Die event-basierte Diagnose kommt mit wenigen Datenwörtern, und die Verarbeitung der Daten in der Cloud über einen kompatiblen Master ist ebenfalls möglich.
Zu erwähnen ist außerdem die Kosteneffizienz, die sich aus dem Einsatz ungeschirmter Leitungen und Standard-Verbindungselementen ergibt. Die Kompatibilität mit der gesamten 500er Serie der Ventilinseln (501, 502, 503) schafft die Voraussetzung für flexiblen und universellen Einsatz. Auf Anfrage kann ASCO-EMERSON auch die Serie 2035 mit einer Anbindung für 580 IO-Link ausstatten.
Die modulare Architektur der Elektropneumatik von ASCO-EMERSON ermöglicht eine sehr hohe Leistungsdichte der Komponenten und eine große Anzahl an Konfigurationsmöglichkeiten. Auf der Grundplatte einer Ventilinsel können Module mit verschiedenen Größen und Durchflussleistungen aufgebaut werden. Außerdem erlaubt dieser Aufbau den Betrieb von Komponenten mit verschiedenen Druckbereichen ohne zwischengeschalteten Regler.
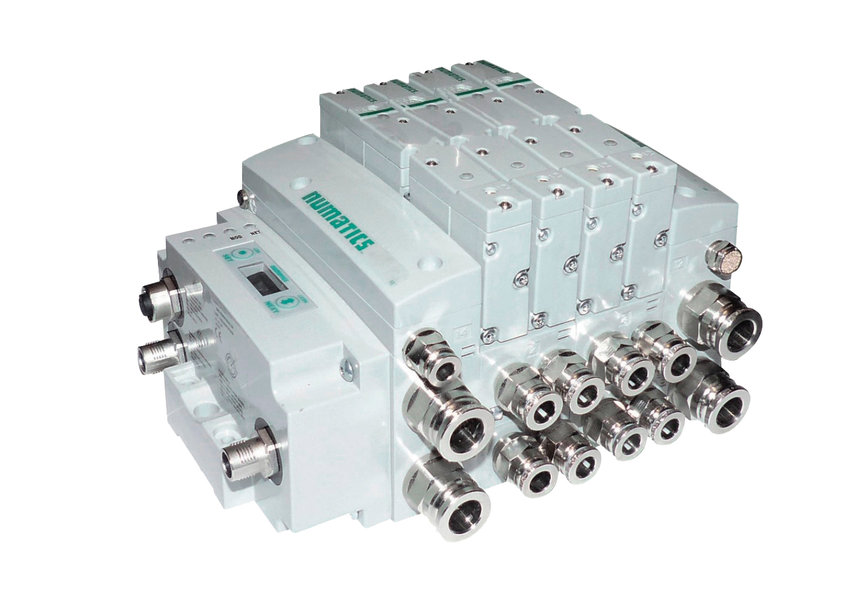
Einsatzmöglichkeiten und Anwendungen
Die Serie 580 IO-Link eignet sich perfekt für die Energieversorgung und Steuerung von modularen Systemen und von Anwendungen, bei denen die Sensorik und die pneumatische Steuerung nicht weiter als 20 Meter voneinander entfernt sind. Typische Einsatzbereiche sind Förderanlagen, pneumatische Roboterhände und –greifer, Montagemaschinen und Abfüllanlagen in der Lebensmittel- und Kosmetikindustrie.
www.asco.com
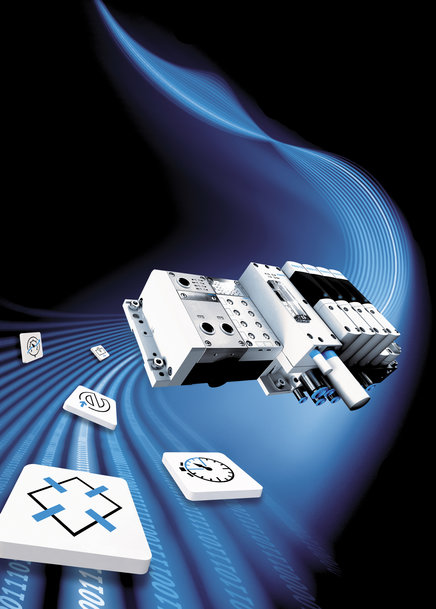
FESTO MOTION TERMINAL: ÜBER 50 FUNKTIONEN AUF EINEM SYSTEM
Das Festo Motion Terminal markiert den Startpunkt für ein neues Zeitalter in der Industrie. Ähnlich wie das Smartphone im Konsumgütermarkt wird es Teil einer Marktrevolution werden.
Die Pneumatik ist eine bestens etablierte (Antriebs-)Technik in der Industrie. Mit dem Festo Motion Terminal VTEM wird sie nochmals effizienter, vielseitiger und flexibler werden. Das Terminal katapultiert die Pneumatik ins Zeitalter von Industrie 4.0 – mit Apps, die es ermöglichen, mehr als fünfzig Einzelkomponenten zu ersetzen. Möglich wird das durch Weiterentwicklungen in Piezotechnik und Software.
Wie das Smartphone vor zehn Jahren den Markt der Mobilfunk-Endgeräte transformiert hat, so wird das neue Motion Terminal nach Überzeugung von Festo die Automatisierungstechnik auf den Kopf stellen. Die neue Art der Funktionsintegration – kombiniert mit Software-Apps – vereinfacht die komplette Wertschöpfungskette, denn es wird nur noch eine Hardware benötigt.
Echte Industrie 4.0
Piezotechnologie, integrierte Hub- und Drucksensorik, gepaart mit der Ansteuerung über Motion Apps, eröffnen Maschinen- und Anlagenbauern ganz neue Perspektiven. Dank der im Festo Motion Terminal verwirklichten Fusion aus Mechanik, Elektronik und Software wird ein pneumatisches Produkt zur echten Industrie-4.0-Komponente und ermöglicht eine flexible Produktion.
Der Wechsel pneumatischer Funktionen sowie die Adaption auf neue Formate werden mittels Parameteränderung über Apps gesteuert. Darüber hinaus erspart die integrierte intelligente Sensorik für Regelung, Diagnose und selbstlernende Aufgaben den Einsatz zusätzlicher Komponenten.
Apps
Bei der Markteinführung des VTEM-Terminals stehen zehn Funktionen über Motion Apps zur Verfügung: von der einfachen Änderung der Wegeventilfunktionen bis zu energieeffizienten Bewegungen, vom proportionalen Verhalten bis hin zu unterschiedlichen Bewegungsprofilen. Das Besondere dabei: Alles funktioniert mit einer identischen Ventilhardware. Durch schnelles Zuschalten neuer Funktionen über Apps können Maschinenentwickler einen Basis-Maschinentypen erstellen und je nach Auswahl der Apps diese Maschine mit unterschiedlichen Funktionen und Ausprägungen je nach Kundenwunsch ausstatten.
Die Funktionszuweisung per Software bringt noch weitere Vorteile: Manipulationssicherheit und Know-how-Schutz, denn von außen ist den Ventilen nicht anzusehen, welche Funktionen sie ausführen. Außerdem vereinfacht sich das Thema Wartung, da man auf lange Ersatz- und Verschleißteillisten verzichten kann.
Energieeffizienz inklusive
Für Energieeinsparungen im Betrieb sorgen die speziell entwickelten Motion Apps sowie die Diagnose- und Leackagedetektionsfunktionen. Aber auch die energiesparende Piezo-Technologie für die proportionale Ventilvorstufe trägt ihren Teil dazu bei.
Mit den Apps „Wählbares Druckniveau“ und „Eco-Betrieb“ lässt sich der Luftverbrauch flexibel an die Anforderungen anpassen. Der Eco-Betrieb senkt den Druckluftverbrauch auf das nötige Minimalniveau, sofern keine Press- und Haltekräfte in der Endlage benötigt werden. Abhängig von der Applikation sind so Einsparungen von bis zu 70 Prozent im Vergleich zum Standardbetrieb möglich.
Weniger Kosten, geringere Komplexität
Das Festo Motion Terminal ermöglicht sowohl die schnelle und kraftvolle Bewegung als auch die Leckage-Diagnose zu deutlich niedrigeren Kosten gegenüber heutigen Lösungen. So werden beispielsweise im Vergleich zu elektrischen Lösungen weniger Controller benötigt, da beim VTEM ein Controller bis zu acht Bewegungen regeln kann. Auch der Stromverbrauch sinkt, und der benötigte Einbauraum geht nach Angaben von Festo um bis zu 65 Prozent zurück.
Im Technologievergleich bieten Automationslösungen mit dem Festo Motion Terminal kostensparende und hoch flexible Lösungen für bis zu acht Applikationen. Anstelle eines Ventils, eines Druckreglers und eines Drucksensors benötigt man nur noch ein einziges Ventil.
Weitere Informationen unter:
https://www.festo.com/vtem/pt/cms/motion-terminal.htm
Fordern Sie weitere Informationen an…