www.konstruktion-industrie.com
05
'18
Written on Modified on
Wartung mit Weitblick
Bei Koki, einem führenden Hersteller automobiler Schaltsysteme, machen ABB Ability Connected Services die Produktion effizienter und kostengünstiger. Dank der vernetzten Fertigungsanlagen können die Bediener potenzielle Probleme frühzeitig erkennen und Instandhaltungen bedarfsorientiert durchführen.
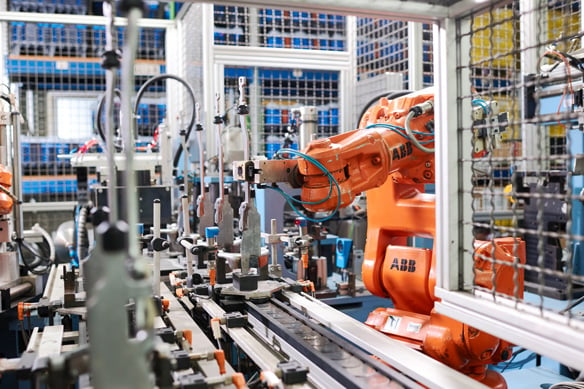
Von reaktiv zu proaktiv
„Für uns hat die Prozesssicherheit der Produktions- und Roboteranlagen höchste Priorität”, sagt Sven Sparmann, Site Manager Maintenance, Repair and Overhaul bei Koki. „Unser Ziel ist es, die Ausfallzeiten zu minimieren.“ Die Connected Services umfassen fünf Bausteine, die je nach Anforderung miteinander kombiniert werden können: Condition Monitoring & Diagnostics, Backup-Management, Remote Access, Fleet Assessment und Asset Optimization. „Diese digitalen Tools verwandeln den bisher reaktiven Ansatz bei der Wartung des Roboterbestands in ein vorausschauendes und proaktives Konzept“, erklärt André Dehlan, Gebietsverkaufsleiter Kundenservice bei ABB Robotics.
Koki zählt namhafte nationale und internationale Automobilhersteller zu seinen Kunden. „Bei der Auditierung durch die Hersteller werden wir stets gefragt, wie wir die Sicherheit der Anlagen garantieren können. Wartung, Monitoring, Service und Support für die Roboter spielen dabei eine wichtige Rolle“, erläutert Sven Sparmann. Über einen Zeitraum von vier Monaten testete Koki das ABB-Serviceangebot erfolgreich an einer Fertigungsanlage, bei der in der Vergangenheit vermehrt Probleme aufgetreten waren. Die Testphase hat gezeigt, dass Connected Services äußert hilfreich sind, um drohenden Ausfällen und Stillständen von Anlagen und Komponenten vorzubeugen.
Netzwerk der Roboter
In den Werken Niederwürschnitz, Glauchau und Jahnsdorf sind insgesamt 60 ABB-Roboter im Einsatz. Sie sind Teil eines vernetzten 24/7-Systems mit sofortigem Support. Die Koki-Mitarbeiter und das ABB-Serviceteam erhalten alle wichtigen Informationen zu den Robotern auf einer sicheren Plattform. Die Anwendung zeigt auftretende Störungen, analysiert Trends und Warnungen, benachrichtigt umgehend bei Problemen und bietet direkten Zugang zu den verschiedenen Supportoptionen.
Die Kommunikation erfolgt über eine zusätzliche 3G-Box in der Robotersteuerung. Jedes System ist über Mobilfunk mit dem ABB-Server verbunden und kommt nicht mit der IT oder internen Kundennetzwerken in Berührung. Grundsätzlich ist aber auch eine Netzwerkvariante mit gesichertem VPN-Zugang möglich. Connected Services und die daraus gewonnenen Daten machen die jährliche Wartung und Inspektion durch ABB noch effektiver. Darüber hinaus können beide Partner anhand der Daten Ad-hoc-Reparatureinsätze schnell und zielgerichtet planen – mit bevorzugter Behandlung von Aktivitäten, mit denen die wichtigsten Kundenprozesse verfügbar bleiben.
Fehler per Telefon beheben
Der Support erfolgt nicht nur über die MyRobot-Homepage, sondern auch klassisch per Telefon über eine 24-Stunden-Helpline. Wird ein Techniker vor Ort benötigt, ist er mit den erforderlichen Komponenten innerhalb von neun Stunden an der Produktionsstätte. Zudem wurden die Bediener bei Koki im Umgang mit den Robotern speziell geschult. „Die Schulung hat unsere Mitarbeiter in die Lage versetzt, mithilfe des ABB-Supports Fehler schnell per Telefon zu beheben und entsprechende Anpassungen vorzunehmen“, sagt Sven Sparmann. In einem konkreten Fall stellte ABB eine Überhitzung in der Steuerung fest. Die Koki-Mitarbeiter in der Instandhaltung nahmen sich des Problems an und konnten den Fehler innerhalb von zwei Stunden beheben – so verhinderten sie einen 24-stündigen Produktionsausfall.
Fordern Sie weitere Informationen an…