www.konstruktion-industrie.com
27
'19
Written on Modified on
Industrie-4.0-fähige Kompressoren-Steuerung bringt mehr Transparenz ins Energiemanagement
„Der Kunde kann Effizienzsteigerungen jetzt jederzeit an jedem Ort visualisieren.“
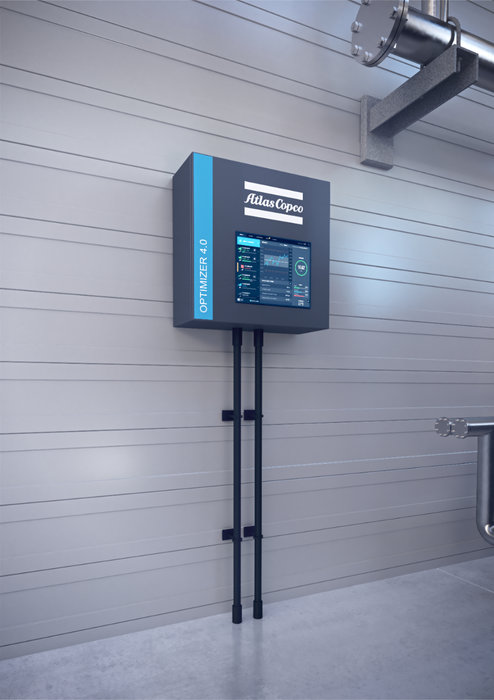
Allen voran der neue Optimizer 4.0, den der Hersteller jetzt auf den Markt bringt. Er macht die Druckluftversorgung effizienter und die Effizienz transparent – ganz im Sinne von ISO 50001. Wir sprachen mit Karsten Decker, Europäischer Energieberater (IHK) der Atlas Copco Kompressoren und Drucklufttechnik GmbH.
FRAGE: Atlas Copco bringt jetzt unter dem Namen „Optimizer 4.0“ eine neue Steuerung auf den Markt. Was war der Anlass hierfür?
Karsten Decker: Neben Betriebssicherheit, Effizienz und der gleichmäßigen Auslastung der Kompressoren ist unseren Kunden heute wichtig, nachzuweisen, dass ihr Unternehmen den Standard für ein Energiemanagement nach ISO 50001 erfüllt. Dafür wollen sich die Anwender jederzeit selbst ein Bild von der Auslastung der Anlage und ihrer Energieeffizienz machen können.
Und sie brauchen zum Teil mehr Schnittstellen für die Konnektivität. Der Optimizer unterstützt jetzt neben den klassischen Schnittstellen, wie Profibus DP und Modbus RTU, zusätzlich Modbus TCP/IP, Ethernet IP und Profinet. Diese sind etabliert und heute Standard.
Es geht also vor allem um besseren Datenfluss und bessere Visualisierung?
Jederzeit Zugriff auf die Daten zu haben und sie von jedem internetfähigen Gerät der Welt über einen Webbrowser anschauen zu können, ist der wichtigste Punkt. Wenn ich eine neue Druckluftstation mit Drehzahlregelung installiere und dabei 30 Prozent Energie spare, will ich das direkt ablesen können.
Wenn ich Produktionsparameter ändere oder in einer Woche ein anderes Druckband fahre, will ich in der nächsten wissen, wie viel ich gespart habe oder was mich das gekostet hat. Allein mit dem Druckluftmanagement per Optimizer kann man zum Beispiel 5 bis 7 Prozent Energie einsparen.
Auch diese Effizienzsteigerung soll visualisiert werden können – und zwar all das nicht nur an der Steuerung selbst. Der Anwender möchte Datentabellen oder grafische Darstellungen in das eigene System importieren können. Dazu steht vorrangig unser Datenmanagementsystem Smartlink zur Verfügung.
Der Optimizer bietet aber auch die Möglichkeit direkt auf die Daten zuzugreifen, und zwar ohne dass die Daten vorher die Firma verlassen, um auf externen Servern entsprechend aufbereitet zu werden. Genau an diesem Punkt sind viele Kunden empfindlich. Unser neuer Optimizer 4.0 speichert die Daten direkt vor Ort, der Kunde kann ohne externe Umwege direkt zugreifen.
Können denn Kunden, die mit den Vorgänger-Steuerungen arbeiten, nicht auf die Daten zugreifen?
Über unsere Software Smartlink können Kunden, die unsere bisherigen Steuerungen einsetzen, wie die ES 16 oder ES 360, sich diese Daten ebenfalls in tabellarischer oder grafischer Form anschauen.
Dazu müssen die Daten aber vorher die Firma verlassen, weil sie von Atlas Copco gespeichert, aufbereitet und visualisiert werden, also auf externen Servern. Doch genau an diesem Punkt sind viele Kunden empfindlich, zum Beispiel aus der Automobilindustrie. Aber auch im Maschinenbau gibt es Berührungsängste, vor allem in Deutschland.
Ein Hersteller, der selbst als Industrie-4.0-Anbieter gilt, hat sogar die Module ausgebaut, die für eine Smartlink-Verbindung als Hardware in der Steuerung beziehungsweise in den Kompressoren sitzen. Bei unserem neuen Optimizer 4.0 ist das anders. Der speichert die Daten direkt vor Ort, der Kunde kann ohne externe Umwege direkt zugreifen.
Und weil wir nun alle wichtigen Schnittstellen anbieten, bleibt außerdem der Echtzeitfaktor komplett erhalten. Steuern und Regeln wird viel transparenter, weil die Auslastung der einzelnen Kompressoren eins zu eins zu sehen ist.
Welche Daten möchten die Anwender denn konkret abrufen und wofür benötigen sie diese?
Unsere Kunden wollen zum Beispiel die Auslastung der Kompressoren analysieren: Arbeiten alle im optimalen Bereich, auch wenn der Luftbedarf schwankt? Den meisten Kunden ist das vor allem kurz vor einem Energieaudit wichtig. In das Energiemanagementsystem werden Verbrauchswerte übernommen, wie etwa der Volumenstrom in Kubikmetern pro Stunde oder die spezifische Leistung.
Diese sogenannte Druckluftkennzahl, die mir sagt, wie viele Kilowattstunden mich ein Normkubikmeter Druckluft bei Systemdruck kostet, kann ich jetzt auch direkt am Optimizer ablesen. Anhand dieses Wertes kann etwa der Betriebsleiter auf einen Blick erkennen, ob alles in Ordnung ist.
Die Daten können als Exceldatei oder als Bilder im JPG- oder BMP-Format eins zu eins ins Energiemanagementsystem importiert werden. Mithilfe des Optimizers kann der Anwender aber nicht nur absolute Werte leichter überblicken, sondern auch analysieren, wie sich zum Beispiel Änderungen in der Produktion auf den Energieverbrauch auswirken.
Der Betreiber will sich sofort ein Bild machen, auch um schnell eingreifen zu können. ISO 50001 bedeutet ja auch, dass Unternehmen bei der Energieeffizienz immer besser werden – das ist ein kontinuierlicher Prozess.
Energieaudit und Zertifizierung nach ISO 50001: Sind die für alle Unternehmen in Deutschland relevant?
Betriebe mit über 250 Mitarbeitern müssen eines von beiden machen. In Deutschland ist etwa die Hälfte der Unternehmen nach ISO 50001 zertifiziert. Aber auch viele kleinere Unternehmen nutzen das Energieaudit gerne, weil Energie eine zunehmend teurere Ressource wird, die sie einsparen wollen.
Außerdem können sie sich per Audit von Wettbewerbern absetzen und als nachhaltiges Unternehmen präsentieren. Große Unternehmen fordern teilweise von ihren Zulieferern die ISO-Zertifizierung, um eine ununterbrochene Zertifizierungskette für ihre Produkte nachweisen zu können.
Für welche Druckluftstationen ist der Optimizer 4.0 sinnvoll?
Der Optimizer eignet sich für Stationen ab zwei bis drei Kompressoren und mindestens 100 Kilowatt Leistung. Darunter empfehlen wir ihn nicht, weil die Energieeinsparung nicht so groß ist, dass sich die Investition schnell amortisiert.
Für kleinere Stationen passt dann zum Beispiel eher eine ES 6, die aber nur die Reihenfolge der Kompressoren vorgeben kann. Der Optimizer regelt hingegen volumenstromabhängig. Das heißt, er ermittelt in Abhängigkeit vom Volumenstrom, welcher Kompressor zum jeweiligen Zeitpunkt am effizientesten arbeitet.
Kann der Optimizer auch Fremdkompressoren regeln?
Ja. Wir geben der Steuerung die Kennlinien aller Maschinen vor, auch diejenigen von Fremdkompressoren. Dafür setzen wir ein spezielles Competitor-Modul ein. Das ist das Besondere an unserer neuen Steuerung, dass wir jetzt sowohl Last-Leerlauf- als auch drehzahlgeregelte Kompressoren anderer Anbieter aktiv regeln können.
Wir binden sie so ein, dass auch diese im optimierten Bereich arbeiten. Denn wir wollen ja, dass der Kunde möglichst effizient fährt, und dafür müssen wir – auch fremde – drehzahlgeregelte Maschinen perfekt auslasten können.
Welchen Anwendern raten Sie, zum Optimizer zu wechseln?
Kunden, deren Kompressorstationen von einer ES 16 oder 360 von Atlas Copco geregelt werden, sind im Prinzip gut aufgestellt, da diese auchvolumenstromabhängig regeln. Der existierende Algorithmus wurde auch für den Optimizer beibehalten. Eine Verbesserung gibt es aber bei der Hardware.
Hier setzen wir jetzt Standardkomponenten ein: einen Industrie-PC mit Touch-Screen, der mit unserer Software ausgestattet ist. Damit ist die Ersatzteilbeschaffung im Fall des Falles wesentlich simpler. Man sollte sich die Frage stellen, wie wichtig Visualisierung und Transparenz im Unternehmen sind.
Mit einem Update der ES 16 sind der Datentransfer und die lokale Visualisierung ohne externe Umwege ebenfalls möglich. Die Nachrüstung kostet etwa die Hälfte der neuen Steuerung, man ist aber natürlich in puncto Schnittstellen und Hardware nicht auf demselben Level.
Kann man verallgemeinernd sagen: Je komplexer die Prozesse, desto eher eignen sich hochwertige Steuerungen wie der Optimizer, weil Anwender dann auch den vollen Zugriff und die Transparenz der Daten wünschen?
Das ist sicher so. In der Pharmaindustrie zum Beispiel wird ja jeder noch so kleine Prozesswert aufgenommen.
Hier ist man eher geneigt, hinsichtlich Visualisierung, schnellem Datenaustausch und Transparenz aufzurüsten als vielleicht in anderen Unternehmen. Übrigens können wir mit dem Optimizer drei verschiedene Druckluftnetze im Unternehmen gleichzeitig regeln. Das ist derzeit vermutlich ein Alleinstellungsmerkmal des Optimizers.
Wer also zum Beispiel ein Niederdrucknetz und ein normales 6- oder 7-bar-Netz hat, ist mit dem Optimizer auch bestens bedient. Dafür wird jedes Netz mit mindestens zwei Drucksensoren ausgestattet.
Ihre neue Steuerung trägt das derzeit oft zitierte „4.0“ im Namen. Was bedeutet das in diesem Zusammenhang?
Industrie 4.0 bedeutet beim Optimizer: Wir können Daten sammeln, diese aufbereiten und entsprechende Maßnahmen ableiten, um unsere Prozesse zu optimieren. In Verbindung mit unserem Smartlink werden als Maßnahmen etwa Nachrichten über Störungen im System an den Kunden oder direkt an uns geschickt.
Wenn zum Beispiel ein definierter Drucktaupunkt nicht eingehalten wird, müssen wir nicht warten, bis eine Störung passiert ist, sondern können uns proaktiv kümmern und Probleme verhindern. In unserem Werk in Antwerpen gibt es einen sogenannten Diagnostic Room, in dem sich Techniker und Ingenieure alle über Smartlink gesendeten Daten von Maschinen anschauen können, für die der Kunde mit uns einen Servicevertrag vereinbart hat.
Wenn Unregelmäßigkeiten auftauchen, wie etwa ein häufiger Temperaturanstieg, informieren diese das jeweilige Kundenzentrum, damit jemand vor Ort beim Kunden nachschaut, was das Problem verursacht. Der große Vorteil für den Kunden ist, dass durch das frühe Eingreifen Betriebsausfälle sowie langwierigere Reparaturen verhindert werden.
Ist der Optimizer teurer als die Vorgängermodelle?
Nein. Der Optimizer kostet ebenso viel wie die ES 16, die er jetzt ablösen soll. Übrigens kann auch diese Investition vom BAFA mit bis zu 25 Prozent Kostenzuschuss gefördert werden – unter dem Stichwort „effiziente Querschnittstechnologie“. Voraussetzung für die Förderung ist eine Station mit mindestens zwei Kompressoren.
www.atlascopco.com
Fordern Sie weitere Informationen an…