www.konstruktion-industrie.com
19
'19
Written on Modified on
Wertstoffsortierung durch Druckluftcontainer mit drehzahlgeregelten Kompressoren
Bedarfsgerechte Druckluftversorgung spart Energie und minimiert Ausfallzeiten.
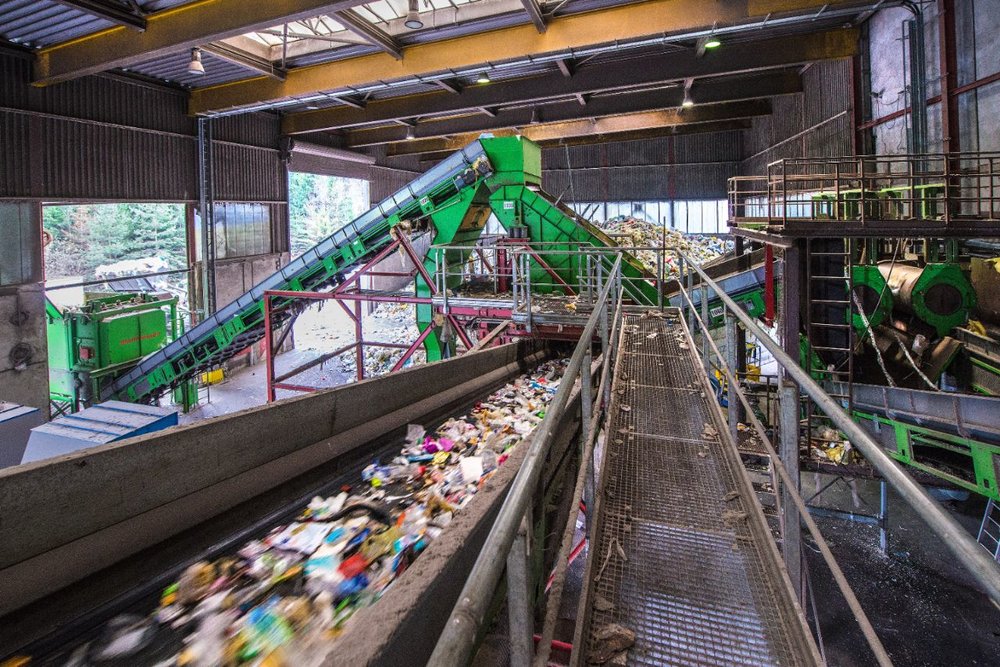
Dass das Thema Recycling für Stefan Böhme mehr als ein Job ist, bemerkt der Besucher bereits, bevor er dessen Unternehmen im oberfränkischen Rehau betritt. Ein Steg führt über einen kleinen Teich bis zum Eingang des Bürogebäudes. Die Bohlen sehen zwar aus wie Holz, sind aber aus Recyclingkunststoff gefertigt.
„Die Paneele stellt ein Unternehmen in Hessen aus unserer Mischkunststoff-Fraktion her“, berichtet der Betreiber der zweitgrößten Wertstoffsortieranlage Bayerns stolz. „Auch für Bootsstege ist das Material aufgrund seiner Haltbarkeit sehr gefragt.“ Böhme ist es wichtig, dass aus den sortierten Fraktionen wieder etwas Sinnvolles entsteht.
Möglichst auf kurzen Wegen bei regionalen Wiederverwertern. Dafür legt er bei seinen Sortierprozessen auch gern noch eine Schippe drauf auf die gesetzlichen Vorgaben. „Es war immer unsere Philosophie, nicht nur das zu tun, was uns der Gesetzgeber vorschreibt, sondern mit den gegebenen technischen Möglichkeiten so viel Material aus den gesammelten Wertstoffen herauszuholen und wiederzuverwerten wie möglich“, erklärt Böhme.
„Außerdem haben wir den Ehrgeiz, den Verwertern eine möglichst hohe Qualität zur Verfügung zu stellen.“
“ Es war immer unsere Philosophie, nicht nur das zu tun, was uns der Gesetzgeber vorschreibt, sondern mit den gegebenen technischen Möglichkeiten so viel Material wie möglich aus den gesammelten Wertstoffen herauszuholen und wiederzuverwerten. ”
Stefan Böhme , Anlagenbetreiber Böhme GmbH, Rehau.
Hochwertiges stoffliches Recycling unter den Top 3 in Deutschland
Was die stoffliche Verwertungsquote angeht, zählt sich Böhme zu den Top 3 in Deutschland. „Wir erreichen hier eine sehr hohe Quote von über 50 Prozent und ermöglichen ein hochwertiges stoffliches Recycling: zu neuen Produkten, Granulaten oder Papierfasern“, beschreibt Böhme den Weg der sortierten Wertstoffe.
„Metall geht ins Stahlwerk, Alu wird im sogenannten Umschmelzverfahren gereinigt und aufbereitet. Aus dem Sortierrest lassen wir einen Ersatzbrennstoff herstellen, der beispielsweise im Zementwerk Öl oder Gas ersetzt.“
2018 wurden in Böhmes Anlage rund 70000 Tonnen an Leichtverpackungen sortiert – etwa zehnmal so viel wie bei der Gründung des Standortes vor 22 Jahren. „Anfangs hatten wir 14 Leute, die in einer Schicht an fünf Förderbändern standen und manuell sortiert haben“, erinnert sich Stefan Böhme.
Seitdem wurde die Anlage Jahr für Jahr erweitert und automatisiert. Inzwischen wird nur noch wenig von Hand sortiert; die meisten Handsortierkräfte haben im Unternehmen andere Aufgaben übernommen. Heute beschäftigt Böhme insgesamt 115 Mitarbeiter.
Druckluftbedarf steigt mit dem Automatisierungsgrad
Die Sortierung der Kunststoffe erledigen mittlerweile unter anderem sogenannte Nah-Infrarotgeräte. Die scannen das Material, erkennen durch IR-Technik in Sekundenbruchteilen eine zuvor programmierte Fraktion, wie beispielsweise Polypropylen und Polyethylen (PP/PE), und senden dann im richtigen Moment einen Luftimpuls, der das gewünschte Material über einen Trennscheitel auf ein Förderband schießt.
Neun dieser Maschinen sind inzwischen im Einsatz. Hinzu kommt noch ein Filmsorter, der nach demselben Prinzip arbeitet und speziell für die Erkennung von Folien eingesetzt wird.
Mit steigendem Automatisierungsgrad ist auch der Druckluftbedarf bei Böhme stetig gestiegen. Ende 2017 kamen die vier vorhandenen Kompressoren, die in einem offenen Container untergebracht waren, endgültig an ihre Grenzen. „Wir wollten mal wieder neue Aggregate in die Sortieranlage einbinden, und dabei stellte sich dann die Frage nach einer passenden Druckluftversorgung“, berichtet Lars Hillebrand, Assistent der Geschäftsführung.
Er ist auch für den Aufbau der neuen Druckluftstation verantwortlich. „Unsere Kompressoren waren schon sehr verschlissen und liefen am Limit. Redundanz hatten wir keine, so dass wir die Produktion bei Störungen nur noch teilweise aufrechterhalten konnten.“
Schnelle Reaktion und passendes Konzept gaben den Ausschlag
Bei seiner Internetrecherche nach möglichen Lösungen und Herstellern stieß Hillebrand auf die Kompressoren von Atlas Copco. „Auf meine Anfrage bekam ich bereits nach einer Stunde einen Rückruf“, lobt er. „Und in der folgenden Woche hatten wir schon das erste Beratungsgespräch hier vor Ort.“ Die zügige Reaktion in Kombination mit dem passenden Konzept bescherte Atlas Copco schließlich den Zuschlag für das Projekt.
„Der Zeitplan für die Umsetzung war ambitioniert“, erinnert sich Şevket Suzan, technischer Berater bei Atlas Copco. „Schon im April 2018 sollte die Anlage von der neuen Druckluftstation versorgt werden.“ Da war es hilfreich, dass das Institut für Energie und Umwelt (BFE) parallel bereits eine Druckluftverbrauchsmessung durchgeführt hatte.
Das BFE unterstützt die Böhme GmbH auch bei der Durchführung eines Energieaudits gemäß EN 16247, das alle Einsparmöglichkeiten im Unternehmen auslotet und die Drucklufterzeugung als großen Energieverbraucher unter die Lupe genommen hat.
“ Aktuell sind wir dabei, die kompletten Verbrauchsdaten inklusive Druckluft zusammenzuführen. Die notwendigen Messgeräte sind bereits eingebaut, so dass wir dann den Energieverbrauch bis zum kleinsten Gerät nachweisen können. ”
Tamara Munzert , Böhme GmbH, Energiemanagement, IT und Marketing.
Hohe Effizienz durch drehzahlgeregelte Kompressoren
„Nach der Erweiterung der Sortieranlage wurde ein Druckluftbedarf von 28 Kubikmetern pro Minute bei einem Betriebsüberdruck zwischen 7 und 8 bar erwartet“, erklärt Suzan. „Daraufhin schlugen wir eine Anlage mit drei Kompressoren vor, die jederzeit 30 Kubikmeter pro Minute liefern kann – auch wenn eine der Maschinen ausfällt.
“ Wegen der hohen Bedarfsschwankungen fiel die Wahl auf den Einsatz drehzahlgeregelter Kompressoren. „So können wir uns vom Atlas-Copco-Konzept und den energetischen Vorteilen der Kompressoren überzeugt hat.“ Bei den drei Maschinen der neuen Druckluftstation handelt es sich um öleingespritzte Schraubenkompressoren vom Typ GA 75 VSD+, wovon einer als Redundanz dient.
„Trotz der Reservemaschine können wir damit einen Grundlastwechsel generieren, weil die drei Maschinen gleich groß sind. Auf diese Weise lasten wir sie gleichmäßig aus“, erläutert Şevket Suzan. Die GA-VSD+-Kompressoren sind mit einer Drehzahlregelung der neuesten Generation und besonders energiesparenden Permanentmagnetmotoren ausgestattet.
Mit ihnen lassen sich im Vergleich zu einer schlecht ausgelasteten Drucklufterzeugung mit Last-Leerlauf-Regelung Energieeinsparungen von bis zu 50 % erzielen. Im Vergleich zur Vorgängergeneration sind die Maschinen noch einmal um 9 % effizienter. exakt die Druckluftmenge erzeugen, die in der Sortieranlage benötigt wird“, begründet Hillebrand die Entscheidung. „Das war dann auch der ausschlaggebende Punkt, der.“
“Mit den drehzahlgeregelten Kompressoren können wir exakt die Druckluftmenge erzeugen, die in der Sortieranlage benötigt wird. Das war der ausschlaggebende Punkt, der uns vom Atlas-Copco-Konzept und den energetischen Vorteilen der Kompressoren überzeugt hat.” Lars Hillebrand , Assistenz der Böhme-Geschäftsführung für das Druckluftprojekt verantwortlich.
„Bayerisch-Sibirien“ stellt hohe Anforderungen an Drucklufttrocknung
Die erzeugte Druckluft gelangt in eine Sammelleitung und durchläuft mehrere Aufbereitungsstufen. Wegen der extrem kalten Winter lag ein besonderes Augenmerk auf der Drucklufttrocknung. „In der warmen Jahreszeit erzeugen wir kältegetrocknete Druckluft mit einem Taupunkt von drei Grad Celsius“, erklärt Hillebrand.
„In den Wintermonaten ist diese Gegend hier jedoch als Bayerisch-Sibirien bekannt; und da wir Außenleitungen haben, besteht immer die Gefahr, dass Wasser kondensiert. Um dem vorzubeugen, haben wir zwei Adsorptionstrockner mit im Konzept.“ Die Druckluft durchläuft dann sowohl den drehzahlgeregelten Kältetrockner vom Typ FD 760 VSD als auch einen warmregenerierenden Adsorptionstrockner BD 550+ von Atlas Copco. Sie enthält dadurch deutlich weniger Feuchtigkeit: In dem Fall liegt der Drucktaupunkt bei –40 °C.
Kompressoren und Drucklufttrockner lassen sich flexibel kombinieren
„Wir haben das System so aufgebaut, dass wir Kompressoren und Trockner flexibel miteinander kombinieren können und so für alle Fälle gerüstet sind“, beschreibt Suzan die Lösung. „Dafür steht uns zur Sicherheit auch noch ein kaltregenerierender Trockner vom Typ CD 550+ zur Verfügung.
Der würde zum Zuge kommen, wenn in den Wintermonaten der warmregenerierende Trockner ausfällt. Wird der Kältetrockner gewartet, können wir auch nur über den Adsorptionstrockner fahren.“ Beim warmregenerierenden Adsorptionstrockner handelt es sich um ein Gerät in der Ausführung „Zero Purge“.
Das heißt, der Regenerationsprozess des Trockenmittels kommt komplett ohne Spülluft aus. „Wir eliminieren die Feuchtigkeit mittels Zusatzheizung aus dem Trockenbett“, erläutert Suzan das Prinzip. „Denn die elektrische Heizung ist hier effizienter als die Erzeugung von Spülluft über die Kompressoren.
Beim kaltregenerierenden Trockner liegt der Spülluftbedarf je nach Temperatur und Volumenstrom bei 15 bis 30 Prozent der Kompressorleistung.“
Die Kompressorensteuerung Optimizer 4.0 sichert effizienten Betrieb der Kompressoren
Neben den Trocknern umfasst die Druckluftaufbereitung zwei UD+-Filter von Atlas Copco, die Allzweck- und Hochleistungsfilter kombinieren, sowie zwei Staubfilter, die den Adsorptionstrocknern nachgeschaltet sind. Koordiniert wird die komplette Drucklufterzeugung über die neue Optimizer-4.0-Steuerung von Atlas Copco.
„Wir können hier ein sehr enges Druckband von plus/minus 0,1 bar fahren, auch weil wir für das Konzept drehzahlgeregelte Maschinen ausgewählt haben“, erläutert Suzan. „Außerdem ist es ein Alleinstellungsmerkmal von Atlas Copco, dass wir den drehzahlgeregelten Kompressoren im Verbund nicht nur ein Anforderungssignal weitergeben und die Regelung der Maschine überlassen, sondern über den Optimizer 4.0 ganz klar vorgeben, mit welcher Drehzahl der Kompressor fahren soll.
Damit stellen wir beim gleichzeitigen Betrieb der drehzahlgeregelten Maschinen sicher, dass diese im effizienten Bereich arbeiten.“
“ Es ist ein Alleinstellungsmerkmal von Atlas Copco, dass wir den drehzahlgeregelten Kompressoren im Verbund nicht nur ein Anforderungssignal weitergeben und die Regelung der Maschine überlassen, sondern über den Optimizer 4.0 ganz klar vorgeben, mit welcher Drehzahl jeder Kompressor fahren soll.
Damit stellen wir beim gleichzeitigen Betrieb der drehzahlgeregelten Maschinen sicher, dass diese im effizienten Bereich arbeiten. ” Şevket Suzan , technischer Berater bei Atlas Copco.
Druckluft Containerlösung = sauber und flexibel
Die Druckluftstation ist in zwei parallel verbundenen 40-Fuß-High-Cube-Containern untergebracht. Drinnen herrscht eine fast hermetische Atmosphäre, da die benötigte Außenluft über Filtermatten gereinigt wird. „Der Container ist die beste Lösung, die wir hier umsetzen konnten“, betont Hillebrand.
„Die Aggregate stehen sauber und trocken, und bei Bedarf kann ich die komplette Station verlegen. Wir haben hier eine hohe Staubbelastung, viel Dreck und Feuchtigkeit. Das ist natürlich Gift für die Maschinen.“ Auch die gewünschte schnelle Realisierung des Projekts ließ sich mit der Containerlösung umsetzen.
Denn die Kompressoren konnten im Container bereits vorinstalliert werden. Die Umstellung von der alten auf die neue Druckluftstation dauerte dann lediglich einen halben Tag, da nur noch die Medienanschlüsse im Plug-and-Play-Verfahren verbunden werden mussten.
Dokumentation der Druckluftmenge durch Visualisierung und Monitoring über Smartview
Über den Optimizer 4.0 und die Software Smartview von Atlas Copco wird die Druckluftanlage visualisiert und die erzeugte Druckluftmenge dokumentiert. Im Gegensatz zum internetbasierten Datenüberwachungs-Service Smartlink des Herstellers müssen die Daten dafür das Unternehmen nicht verlassen.
Sie werden allerdings auch nicht von den Druckluftexperten von Atlas Copco aufbereitet, sondern müssen intern analysiert und ausgewertet werden. „Aktuell sind wir dabei, die kompletten Verbrauchsdaten unserer Sortieranlage inklusive Druckluft zusammenzuführen“, berichtet Tamara Munzert, die bei Böhme für Energiemanagement, IT und Marketing zuständig ist.
„Die notwendigen Messgeräte sind bereits eingebaut, so dass wir dann den Energieverbrauch bis zum kleinsten Gerät nachweisen können. Das ist die Voraussetzung für unser Energieaudit gemäß EN 16247.“
BAFA förderte die Druckluftstation mit 30 % der Investitionskosten
Der Einsatz der hocheffizienten GA-VSD+-Kompressoren hat sich für Böhme in doppelter Hinsicht gelohnt. Zum einen ist der Stromverbrauch merklich gesunken, zum anderen wurden Maschinen, Steuerung und Installation der Anlage mit 30 % vom Bundesamt für Wirtschaft und Ausfuhrkontrolle (BAFA) gefördert.
„Zum Stromverbrauch haben wir zwar noch keinen Langzeitwert, aber der wird sich durch die drehzahlgeregelten Maschinen definitiv verbessern“, ist sich Hillebrand sicher. Bei der Investition sei es aber nicht nur um Energieeffizienz gegangen, sondern vor allem um Zuverlässigkeit und einen störungsfreien Betrieb.
„Durch die volle Redundanz haben wir nun keine Ausfallzeiten mehr, die auf die Druckluft zurückzuführen wären“, zieht Hillebrand Bilanz. „Und die saubere Containerlösung hat darüber hinaus den Wartungsaufwand minimiert.
“ Als nächster Schritt steht nun die Installation einer Wärmerückgewinnung für die Druckluftstation und ihre Einbindung ins bestehende Heizungssystem an. Denn auch in puncto Energieeffizienz bleibt Stefan Böhme seinem Motto treu, „möglichst viel herauszuholen“. Autorin: Stephanie Banse, Journalistin in Hamburg
Böhme GmbH, Rehau: Seit 1985 erfasst, sortiert und vermarktet die Böhme GmbH Wertstoffe. In der 1996 eröffneten Hauptgeschäftsstelle in Neukühschwitz bei Rehau und einer Niederlassung in Oberpferdt bei Konradsreuth arbeiten heute insgesamt 115 Mitarbeiter, der Umsatz lag 2017 bei 14,8 Millionen Euro.
Der nach § 56 des Kreislaufwirtschaftsgesetzes (KrWG) zertifizierte Entsorgungsfachbetrieb betreibt unter anderem die größte Sortieranlage für Leichtverpackungen (LVP) für die Dualen Systeme Deutschland in Nordbayern. Darüber hinaus stellt das Unternehmen öffentliche Behälter in den Landkreisen Hof und Wunsiedel bereit und fährt die gesammelten Wertstoffe ab. 2015 hat in Neukühschwitz zudem eine der modernsten Sortieranlagen für Papier ihren Betrieb aufgenommen.
www.atlascopco.com
Fordern Sie weitere Informationen an…