Schaeffler liefert größtes Gelenklager aus
Hohes Konstruktions- und Fertigungs-Know-how für 4,7 Tonnen schweres Speziallager
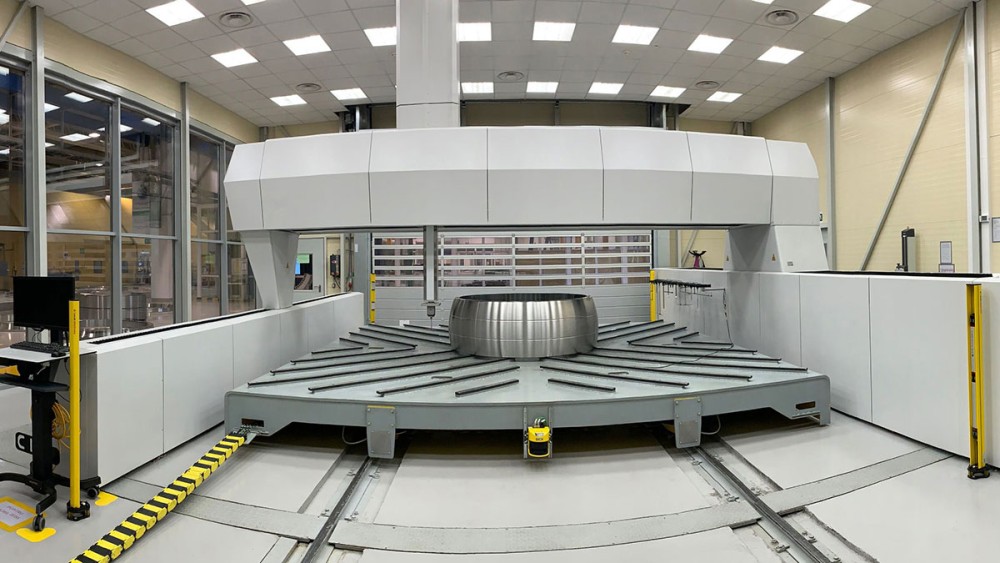
Nicht nur die Auslegung des Speziallagers stellte hohe Anforderungen an die Schaeffler-Experten, sondern auch die Herstellung.
- Speziallager mit fast zwei Metern Außendurchmesser für Anwendung in Schneidkopfbagger
- Asymmetrische Auslegung spart Bauraum und Gewicht
- Fertigung des einteilig konstruierten Innen- und Außenrings durch Schaeffler-Know-how ermöglicht
Schaeffler hat das in seiner Firmengeschichte bisher größte Gelenklager gefertigt. Das Speziallager hat einen Außendurchmesser von 1.900 Millimetern, einen Bohrungsdurchmesser von 1.500 Millimetern und eine Höhe von 600 Millimetern.
Das Gewicht beträgt knapp 4,7 Tonnen. Eingesetzt wird das Lager in einem Schneidkopfbagger, der von Royal IHC ausgelegt und gebaut wurde.
Das niederländische Unternehmen ist Spezialist für Anlagen, Schiffe und Dienstleistungen für die Offshore-, Ausbagger- und Nassabbaumärkte.
Besondere Einsatzbedingungen
Ein Schneidkopfbagger ist ein Arbeitsschiff mit oder ohne eigenen Antrieb, das festes Material von Gewässerböden löst. Unterdruck saugt das Gestein an und fördert es, unter anderem über schwimmende Leitungen, an Land.
Besonders belastet ist hierbei die Verbindung zwischen der Rohrleitung und dem Schiff, die über ein am Rumpf montiertes Gelenklager erfolgt.
Das Lager nimmt dabei die Rotativ-Bewegungen, die zwischen Rohrleitung und Rumpf entstehen, auf. Auf Basis dieser Anforderungen wurde ein spezifisches, auf die Anwendung ausgelegtes Lager konstruiert.
Kompetenz für den Kunden – alles aus einer Hand
Durch die hohe Kompetenz von Schaeffler in Anwendung, Konstruktion und Produktion sowie durch einen engen Austausch mit dem Kunden Royal IHC war es möglich, das Lager in einer Rekordzeit von nur drei Monaten gemäß den Kundenanforderungen zu fertigen.
Dabei stellte nicht nur die Auslegung des Speziallagers hohe Anforderungen an die Schaeffler-Experten, sondern auch die Herstellung. Die in der Anwendung auftretenden Stoßbelastungen machten eine einteilige Konstruktion des Innen- und Außenrings erforderlich.
Hohe Betriebszuverlässigkeit bei geringem Wartungsaufwand
Das Lager muss die auftretenden Kantenspannungen eliminieren und den Dimensionen entsprechend große Kräfte aufnehmen. Weil die Kräfte nur einseitig auf das Gelenklager wirken, wurde es asymmetrisch ausgelegt. Das spart Bauraum und Gewicht.
Um eine lange Lagerlebensdauer sowie geringen Verschleiß zu gewährleisten, hat Schaeffler ein spezielles Schmiernutensystem konstruiert. Die Schmiernuten sind so ausgelegt, dass sich das Fett auch bei kleinen Schwenkbewegungen im Bereich von 20 Grad gleichmäßig verteilt und somit eine optimale Schmierung gewährleistet ist.
Die Einsatzbedingungen im Offshore-Bereich erfordern zudem einen speziellen Korrosionsschutz. Dafür wurden die Gleitflächen des Lagers mit einem bewährten Gleitlack versehen.
Dieser sorgt dafür, dass auch bei Mangelschmierung kein metallischer Kontakt zwischen Innen- und Außenring entsteht. Durch Fettschmierung wird das Lager zusätzlich vor Korrosion geschützt.
So ist für den Kunden eine hohe Betriebszuverlässigkeit bei geringem Wartungsaufwand gewährleistet.
www.schaeffler.com
Fordern Sie weitere Informationen an…