www.konstruktion-industrie.com
08
'19
Written on Modified on
Im 3D-Druck-Verfahren Werkzeuge für die Zukunft herstellen
Kennametal entwickelt ein leichtes, im 3D-Druckverfahren hergestelltes Aufbohrwerkzeug zur Bearbeitung von Motorstatorgehäusen, das bezüglich Genauigkeit, Rundheit und Oberflächengüte alle Anforderungen erfüllt.
Kennametal hat ein im 3D-Druckverfahren hergestelltes Aufbohrwerkzeug zur Bearbeitung von Motorstatorgehäusen entwickelt, um der wachsenden Nachfrage nach leichteren Werkzeuglösungen zur Bearbeitung von Komponenten für Hybrid- und Elektrofahrzeuge zu begegnen.
Komponenten für Elektrofahrzeuge werden üblicherweise auf kleineren, weniger leistungsstarken CNC-Bearbeitungszentren hergestellt, auf denen nur leichtere Werkzeuglösungen eingesetzt werden können. Das neue, im 3D-Druckverfahren hergestellte Aufbohrwerkzeug von Kennametal wiegt nur halb so viel wie die in herkömmlichen Verfahren gefertigte Ausführung, genügt beim Aufbohren von Aluminium-Motorblöcken jedoch allen Anforderungen, was die Genauigkeit, Rundheit und Oberflächengüte angeht.
„Die Hauptbohrung für den Stator eines Elektromotors hat einen Durchmesser von ca. 250 mm und eine Länge von ca. 400 mm. Außerdem muss in den Boden des Motorgehäuses eine kleinere Lagerbohrung eingebracht werden“, erklärt Harald Brütting, verantwortlich für die Programmentwicklung. „Würde die für diese Art Motorgehäuse benötigte Reibahle in einem herkömmlichen Verfahren hergestellt, wöge sie sie über 25 Kilogramm. Und das wäre sowohl für die verwendete Werkzeugmaschine als auch für den Maschinenbediener viel zu schwer.“
Daher regten Brütting und die Entwicklungsingenieure von Kennametal an, in der hauseigenen additiven Fertigung ein leistungsstarkes, aber leichtes Werkzeug herzustellen. Dabei kamen einige, in der Praxis bereits bewährte Kennametal-Technologien zum Einsatz, darunter die fein einstellbaren RIQ Schneidkörper für die Hochpräzisionsbearbeitung und ein KM4X-Adapter für maximale Steifigkeit. Außerdem verfügt das neue Werkzeug über innere, im 3D-Druckverfahren hergestellte Kühlkanäle. Diese sollen ebenfalls dazu beitragen, die Produktivität und Lebensdauer des Werkzeugs zu maximieren.
„Durch den Einsatz des 3D-Drucks mit Metallpulverbett und einer FEM-Analysesoftware ließ sich ein Werkzeug konstruieren und bauen, bei dem das Kippmoment sehr nahe an der Spindelstirnseite liegt. Dadurch konnten wir einerseits die Steifigkeit der Konstruktion erhöhen, andererseits aber auch die Gewichtsvorgaben des Kunden erfüllen“, führt Werner Penkert aus, verantwortlich für den Bereich Zukunftstechnologien. „Das neue Werkzeug belegt eindrucksvoll, wie effektiv Kennametal fortschrittliche Fertigungstechnologien einsetzt, um auch kundenspezifische Herausforderungen zu meistern.“
Das neue Werkzeug ist in zwei verschiedenen Ausführungen erhältlich. Die eine ist mit einem rohrförmigen Kohlefaserkörper ausgestattet, die andere verfügt über einen im 3D-Druckverfahren hergestellten Metallkörper. Die Ergebnisse waren sehr überzeugend. Das Werkzeug mit dem im 3D-Druckverfahren hergestellten Körper wog nur 10,7 kg und die Kohlefaserversion nur 9,5 kg. Damit waren beide Ausführungen noch nicht einmal halb so schwer wie mit herkömmlichen Verfahren hergestellte Werkzeuge.
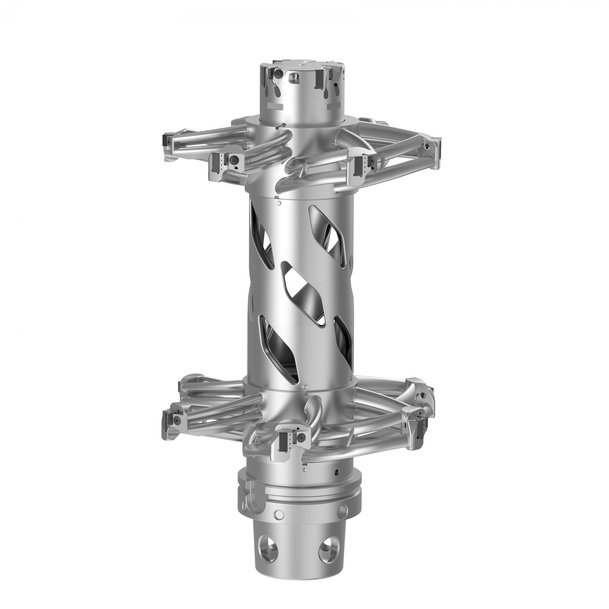
Nutzung bewährter Kennametal-Technologien. Hochpräzise RIQ Schneidkörper und KM4X-Adapter für höchstmögliche Steifigkeit.
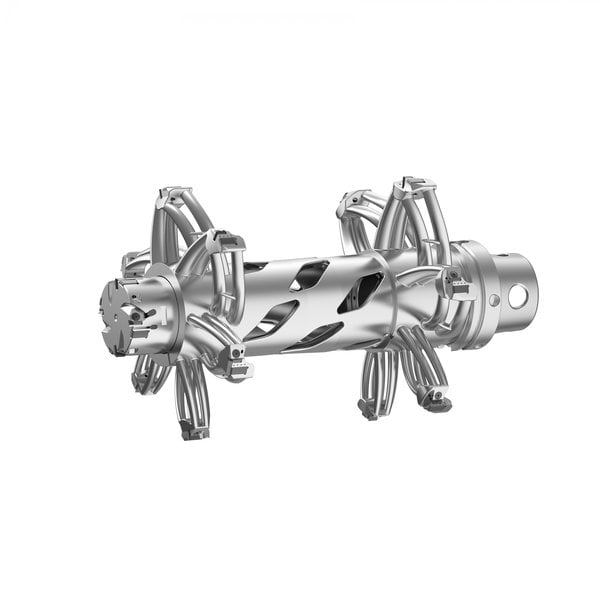
Gewichtsreduzierung durch additive Fertigungsverfahren. Das Gesamtgewicht des im 3D-Druck hergestellten Werkzeugs liegt bei 10,7 kg. Somit wurde eine Halbierung des Gewichts erreicht. Die Bohrungen für den Stator erfüllen dennoch alle Anforderungen, was die Oberflächengüte, Rundheit und Genauigkeit angeht.
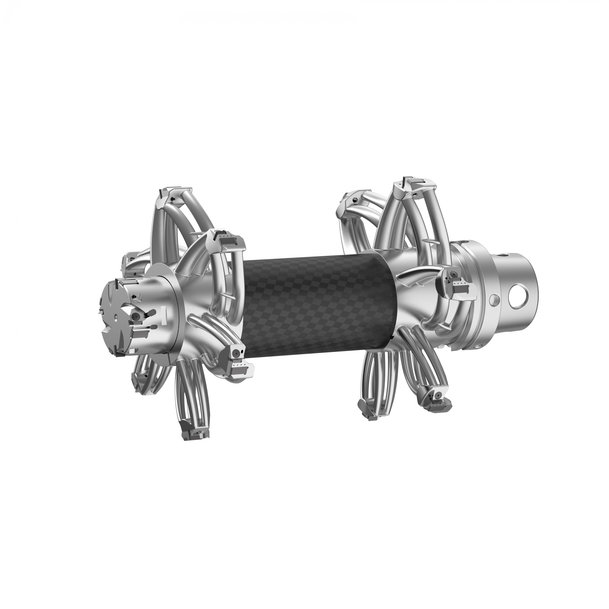
Das gleiche Werkzeug, nur noch leichter. Anstelle des im 3D-Druckverfahren hergestellten Metallkörper kommt ein Kohlefaserkörper zum Einsatz. Dadurch wird eine weitere Gewichtsreduzierung auf 9,5 kg ermöglicht.
Fordern Sie weitere Informationen an…