www.konstruktion-industrie.com
02
'19
Written on Modified on
Angel Trains, Db Esg Und Stratasys Testen Erstmals In Grossbritannien 3d Gedruckte Bauteile In Personenzügen
Durch die Möglichkeit, Ersatzbauteile bei Bedarf schnell zu produzieren, hilft der 3D-Druck den Bahnbetreibern, Züge besser zu warten und die Servicequalität für die Fahrgäste zu verbessern.
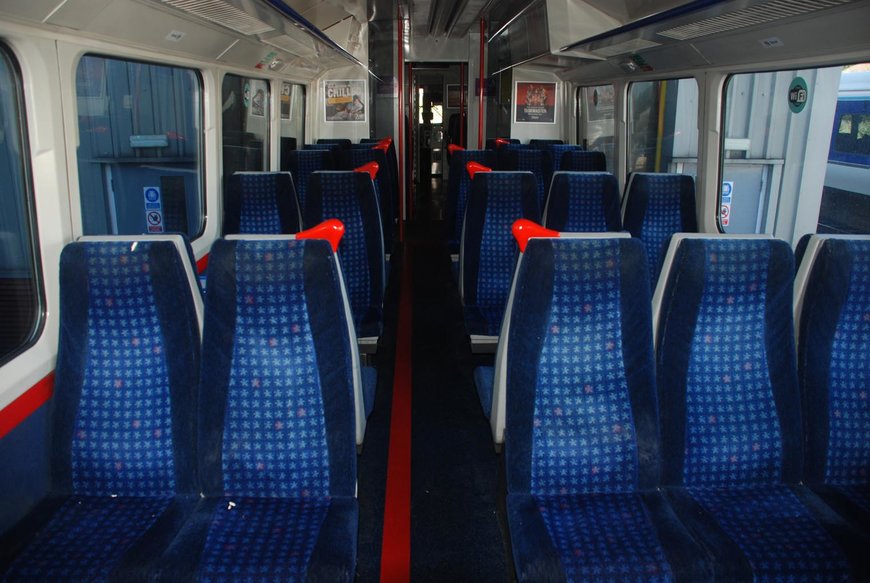
Bei diesen Bauteilen handelt es sich um vier Armlehnen und sieben Haltegriffe für Fahrgäste, die in Zügen von Chiltern Railways eingebaut wurden. Der bisherige Erfolg des Tests zeigt, wie Bahnbetreiber mittels 3D-Druck alte Bauteile schneller ersetzen, Fahrzeuge schneller wieder in Betrieb nehmen und ihre Züge besser instandhalten und so die Servicequalität für Fahrgäste verbessern können.
Die branchenübergreifende Zusammenarbeit zwischen Angel Trains, DB ESG und Stratasys zielt darauf ab, den 3D-Druck zu nutzen, um Probleme beim Austausch veralteter Bauteile in der gesamten britischen Bahnindustrie zu lösen.
Anders als in der Automobilindustrie, in der Fahrzeuge von Haushaltsmarken jedes Jahr millionenfach in Serie gefertigt werden, ist die Anzahl der Züge in der Schienenindustrie vergleichsweise gering und zum Teil über 30 Jahre alt. Bahnbetreiber stellt diese Kombination vor mehrere Herausforderungen, vor allem bei der Instandhaltung und der Erneuerung von Bauteilen.
„In jüngster Zeit machen sich die Betreiber zunehmend Sorgen um die Beschaffung von Ersatzteilen für ältere Züge. Es wird immer schwieriger, diese in kurzer Zeit zu angemessenen Kosten zu bekommen”, erläutert James Brown, Data and Performance Engineer bei Angel Trains.
„Das Problem ist, dass herkömmliche Fertigungsmethoden nur bei hohen Ersatzteil-Stückzahlen rentabel sind, und die Betreiber müssen vielleicht nur einige alte Zugteile erneuern. Unter Umständen gibt es auch Vorlaufzeiten von mehreren Monaten. Deshalb arbeiten wir gemeinsam mit DB ESG und Stratasys daran, wie Betreiber diese Hürden durch den Einsatz von 3D-Druck überwinden können, indem sie bei einem Bruchteil des Kosten- und Zeitaufwands herkömmlicher Methoden die genaue Anzahl der Bauteile fertigen, die sie benötigen”, so Brown.
Bedeutender Rückgang der Produktionskosten und Vorlaufzeiten
Ein Beispiel für diese Kosten- und Zeiteinsparungen sind die zur Zeit bei Chiltern Railways in Betrieb befindlichen Armlehnen. Brown zufolge hätte dieses Bauteil mit herkömmlichen Fertigungsmethoden eine Vorlaufzeit von etwa vier Monaten. Mit der FDM-3D-Drucktechnologie von Stratasys kann hingegen innerhalb von einer Woche eine fertige Armlehne gefertigt werden. Dies ist ein Rückgang um 94%. Brown glaubt, dass pro Bauteil Einsparungen von bis zu 50% möglich sind.
Auch beim Haltegriff musste das alte Bauteil erneuert werden. Aber der ursprüngliche Lieferant hatte seinen Betrieb eingestellt. Zur Herstellung weiterer Bauteile hätte man also ein neues Fertigungswerkzeug benötigt. Dies hätte bis zu 15.000 britische Pfund gekostet und die Vorlaufzeit hätte bei zweieinhalb Monaten gelegen. Mittels 3D-Druck konnten die sieben erforderlichen Haltegriffe in drei Wochen zu weitaus geringeren Kosten pro Bauteil gefertigt werden.
„Es sind spannende Zeiten für die britische Bahnindustrie”, sagt Brown weiter. „Bahnbetreiber können mit dieser Technologie sehr viel besser reagieren, wenn kaputte oder beschädigte Fahrgast-Bauteile erneuert werden müssen. Ein 3D-gedrucktes Ersatzteil kann bei Bedarf gefertigt und sofort eingebaut werden. Da nun geringe Stückzahlen gefertigt werden können, untersuchen wir, wie man 3D-Druck nutzen kann, um die Innenausstattung besser an pendelnde Fahrgäste anzupassen.
Wir haben beispielsweise 3D-gedruckte Rückenlehnentische mit Blindenschrift getestet. Fahrgästen wird darauf mitgeteilt, dass sich die Toilette von diesem Sitz aus zehn Reihen weiter hinten befindet. Eine derartige Berücksichtigung von Kundenanforderungen gab es noch nie und ist nur mit 3D-Druck möglich. Der Betrieb von Zügen und das Fahrgasterlebnis kann hierdurch bedeutend verbessert werden.”
DB ESG führte umfassende Tests mit verschiedenen Industriematerialien für den 3D-Druck durch, um sicherzustellen, dass 3D-gedruckte Bauteile erstmals dem britischen Bahnverkehrsstandard EN45545-2 entsprechen. Die endgültigen Bauteile wurden mit dem FDM-basierten 3D-Drucker Fortus 450mc von Stratasys aus dem ULTEM™ 9085 Resin gefertigt, der den Feuer-, Rauch- und Toxizitätsstandards der Bahnindustrie entspricht.
Martin Stevens, Mechanical Engineering Manager bei DB ESG, erläutert: “Mit dem Erhalt der Zertifizierung entfällt ein Hindernis, das der Einführung von 3D-Druck auf breiter Front in britischen Zügen bisher im Wege stand. Unsere Aufgabe bei diesem Projekt bestand darin, das Design, die Produktion und die Endbearbeitung von FDM-Bauteilen zu untersuchen und zu prüfen, ob die Bauteile den Bahnstandards entsprechen und unter den Einsatzbedingungen funktionieren. Zudem haben wir die Gestaltung von Komponenten bei der FDM-Fertigung optimiert.”
Phil Andrews, Interim Engineering Director bei Chiltern Railways sagt: „Chiltern Railways freut sich darüber, in seinen Zügen an diesem innovativen Test mit 3D-gedruckten Bauteilen mitzuwirken. Die Bearbeitungszeiten sind beim 3D-Druck viel schneller und es ist kostengünstiger als herkömmliche Fertigungsmethoden. Viele unserer Züge sind fast dreißig Jahre alt. Deshalb ist es unerlässlich, dass wir die Bauteile so schnell wie möglich beschaffen können. Dieser Test wird sich darauf auswirken, wie wir bei der Kundenzufriedenheit abschneiden, bei der wir in der Branche führend sind. Zudem gewährleistet er auch, dass die Innenausstattung unserer Züge nach höchsten Standards instandgehalten wird.”
Nach den erfolgreich verlaufenen Tests verfügt die Gruppe inzwischen über ein reproduzierbares Verfahren zur Fertigung von Bauteilen, die den Standards der Bahnindustrie entsprechen und für den Einsatz in Fahrgastwagen geeignet sind. Bahnbetreiber reagieren positiv und die Dreiergruppe will nun ihren nächsten Test durchführen, diesmal mit Great Western Railway. Das Unternehmen möchte in den kommenden Monaten in bestimmten Zügen 3D-gedruckte Bauteile einbauen.
Yann Rageul, Head of Strategic Accounts EMEA bei Stratasys, fasst zusammen: „Die Funktionsfähigkeit 3D-gedruckter Bauteile in britischen Zügen konnte erfolgreich nachgewiesen werden und dies kann zu einem Wandel der traditionellen Lieferkette der Bahnindustrie führen. Bahnbetreiber können die Probleme in Verbindung mit physischen Lagerbeständen beseitigen, indem sie eine digitale Inventarsammlung aufbauen, die bei Bedarf überall per 3D-Druck in der genauen erforderlichen Anzahl verfügbar ist. Wir erleben eine neue Ära echter bedarfsgerechter Produktion ohne Abfall.”
www.stratasys.com
Fordern Sie weitere Informationen an…