www.konstruktion-industrie.com
16
'21
Written on Modified on
IMPAQT macht den Unterschied
Die Software-Leistung von IMPAQT beeindruckt selbst erfahrene Verarbeiter.
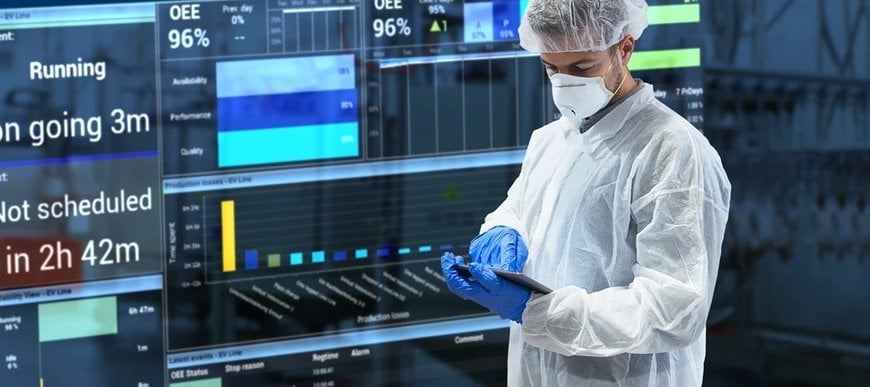
Die IMPAQT-Software bietet enorm viele Vorteile. Selbst erfahrene Verarbeiter sind von den Funktionsfähigkeiten dieses äußerst leistungsfähigen Tools erst überrascht und dann begeistert. Besonders die Möglichkeiten, mit IMPAQT Ausfallzeiten zu reduzieren, findet viel Anklang. Sie freuen sich auch, dass sie die IMPAQT-Software an ihre eigenen Bedürfnisse und Anforderungen anpassen können.
Mit der Gesamtanlageneffektivität (OEE) wird in fast allen Fertigungsindustrien die Effizienz ermittelt. Normalerweise werden die Daten der Produktionszeit in die Kategorien Verfügbarkeit, Leistung und Qualität unterteilt. Eine Verfügbarkeit oder Betriebszeit von 100 % bedeutet, dass ein Herstellungsprozess immer ohne ungeplante Stopps verfügbar ist. Eine Leistung oder ein Durchsatz von 100 % wird erreicht, wenn die tatsächlichen Ergebnisse den theoretischen Maximalwert erreichen. Hierbei wird auch berücksichtigt, warum und wo Leistungsverluste aufgetreten sind. Eine Qualität von 100 % bedeutet, dass der Produktionsprozess absolut keinen Qualitätsverlust aufweist. Das heißt für die Geflügelverarbeitung, dass es keine an einem Bein aufgehängten Produkte gibt, keine Produkte aus der Linie gefallen sind und keine Produkte bei der Veterinärkontrolle abgelehnt worden sind.
IMPAQT beeindruckt
IMPAQT bietet Verarbeitern bislang unbekannte Möglichkeiten. László Bárány, Geschäftsführer von Master Good in Ungarn, der größten Broiler-Integration in Ungarn, drückt es so aus:
„Wir sind natürlich daran interessiert, dass unsere Ausrüstung jederzeit Höchstleistungen zeigt. Mit IMPAQT können wir uns sofort auf Probleme konzentrieren, die einen Rückgang des Ertrags oder der Qualität verursachen. Unsere technischen Mitarbeiter haben damit ein unschätzbares Werkzeug zur Hand. Sie können ihre entscheidende Aufgabe noch effektiver erfüllen.“
László Bárány, Geschäftsführer von Master Good in Ungarn
IMPAQT basiert auf Fakten
Die Verarbeiter freuen sich über den positiven Effekt von IMPAQT, da Entscheidungen nicht mehr aus dem Bauchgefühl der Mitarbeiter heraus getroffen werden. Die Bediener denken, sie hätten die richtige Ursache eines Problems gefunden. IMPAQT hingegen stützt seine Ergebnisse nur auf Fakten und beweist manchmal, dass die Bediener leider daneben lagen. Jan Legters, Werksleiter von Esbro in den Niederlanden, nennt ein Beispiel:
„Wir hatten ein interessantes Gespräch mit einem Bediener der Bratfertigungslinie, der über 30 Jahre Erfahrung hat und sich weigerte IMPAQT zu glauben, die meldete, dass Einheit 9 der Nuova nicht optimal funktionierte. Er war überzeugt, dass es reiner Zufall war, wenn die Maschine nicht so lief, wie sie sollte. Schließlich bat ich ihn, die Einheiten 9 und 10 auszutauschen. Erst dann, nachdem er in mein System geschaut hatte, gab er zu, dass IMPAQT richtig lag.“
Jan Legters, Werksleiter von Esbro in den Niederlanden
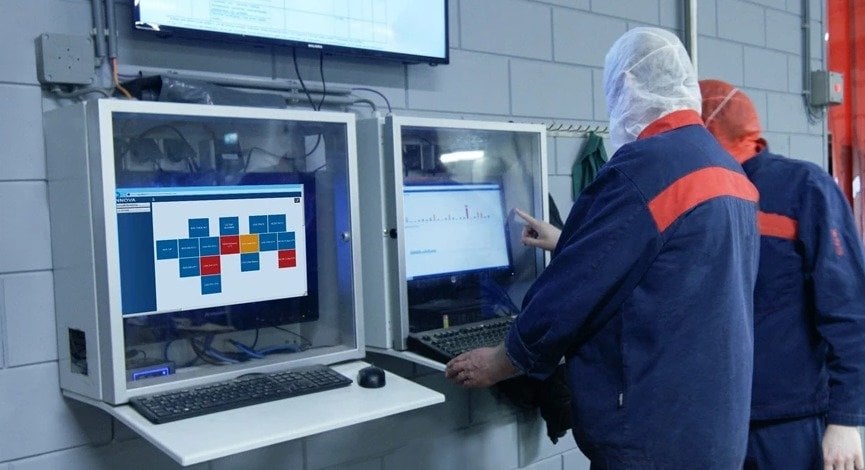
IMPAQT nennt Ursachen
Verarbeiter finden es normalerweise schwierig, die Ursache eines Linienstopps aufzuspüren. Aber das gehört jetzt der Vergangenheit an. Sie sind sehr froh, dass IMPAQT nicht nur sofort einen Linienstopp signalisiert, sondern auch die Ursache anzeigt. Robert Duda, Application and Maintenance Manager bei Cedrob in Polen, sagt:
„Mit IMPAQT können wir in Echtzeit genau sehen, welche Ereignisse während des Betriebs der Linie aufgetreten sind. Es ist viel einfacher geworden, zum Beispiel beschädigte Kübel zu erkennen. Wir können solche Probleme viel schneller als bisher lösen, was unsere Ausfallzeiten wirklich minimiert. Es gab eine Zeit, da blieb die Linie immer wieder stehen, obwohl das Bedienfeld keinen Fehler anzeigte. Jedes Mal mussten die Bediener warten, bis die Linie wieder angelaufen war. Wir suchten im Ereignisprotokoll nach dem Grund des Stillstands der Linie und IMPAQT konnte uns sofort weiterhelfen. Der Grund war ein beschädigter Kontakt im Sicherheitsschalter. Oxidation verursachte Leitungsvibrationen, die den Sicherheitskreis jedes Mal für eine sehr kurze Zeit unterbrachen. Diese Erkenntnis hat uns eine Menge Ärger erspart.“
Robert Duda, Application and Maintenance Manager bei Cedrob in Polen
IMPAQT verbessert den Prozess
Mit IMPAQT verursacht eine Warnung keine Panik mehr. Im Gegenteil, wenn jeder im Werk und im Kontrollraum genau weiß, was zu tun ist, kann der Prozess noch weiter optimiert werden. Der genaue Grund eines Alarms kann schnell analysiert und zukünftige Warnungen verhindert werden. Jan Legters weiter:
„Normalerweise vermerken die Bediener nicht, was während eines Linienstopps passiert. Sie wollen die Linie nur so schnell wie möglich wieder in Betrieb nehmen. Sie sehen ein in der Bratfertigmaschine feststeckendes Huhn, nehmen es heraus, setzen die Maschine zurück. Die Maschine funktioniert wieder und die Welt scheint in Ordnung zu sein. Leider hilft uns das nicht bei der Verbesserung unserer Prozesse. Auf diese Weise reagieren wir nur passiv auf Vorfälle. Mit IMPAQT kann ich nachweisen, dass der Kühltunnel um 10:22 Uhr gestoppt wurde und die Bratfertigmaschine 12 Sekunden später. Daher hat ein Ausfall des Kühltunnels den Stillstand verursacht. Wir müssen also diese Anlage unter die Lupe nehmen, um unseren Prozess zu verbessern.“
Jan Legters, Werksleiter von Esbro in den Niederlanden
www.marel.com
Fordern Sie weitere Informationen an…