www.konstruktion-industrie.com
16
'21
Written on Modified on
Robotergestützte Sensormontage in Industrie 4.0-Umgebung
Flexibilität in Reinkultur.
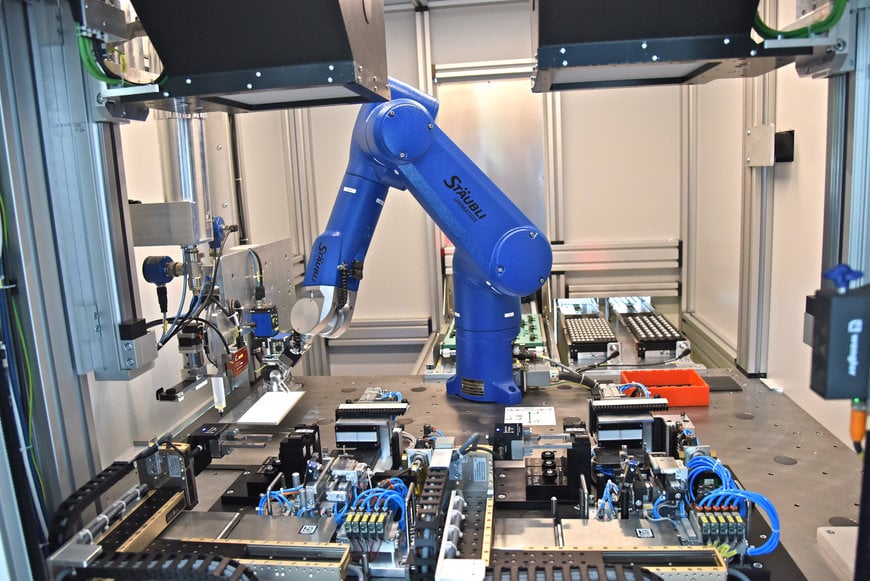
Sensorhersteller sind innovativ. Müssen sie auch, kommt doch der Leistungsfähigkeit der Sensorik in digital vernetzen Prozessen eine Schlüsselrolle zu. Wenglor in Tettnang am Bodensee beweist mit einer intelligent konzipierten Montagezelle, dass nicht nur die Endprodukte wegweisend sind, sondern auch deren Produktion.
Die Frage nach dem Geschäftsverlauf in den zurückliegenden Jahren erübrigt sich bereits auf dem Weg vom Parkplatz ins Gebäude. Auf dem Gelände der Firmenzentrale zeugen zahlreiche Neubauten von erheblichen Investitionen in der jüngeren Vergangenheit. Am positiven Geschäftsverlauf hat sich auch aktuell nichts geändert, wie Michael Martin, Softwareentwickler bei wenglor, versichert: „Unser Business boomt weiterhin. Wir planen bereits den nächsten Neubau, um die immense Nachfrage nach smarten Sensortechnologien decken zu können. Tatsächlich profitieren wir stark vom Industrie 4.0 Trend, der den Sensorikmarkt enorm beflügelt. “
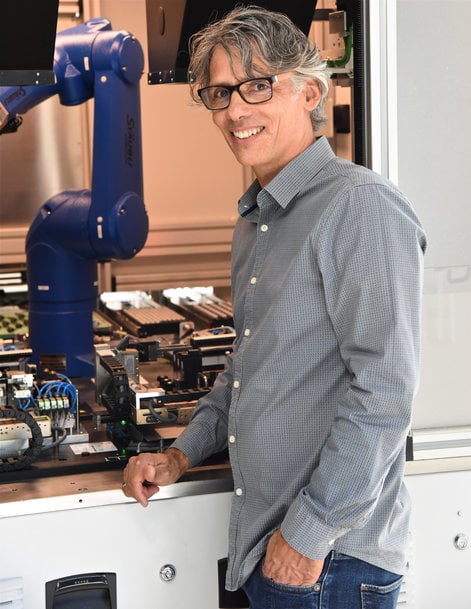
Michael Martin, Softwareentwickler bei wenglor, freut sich über die positive Entwicklung des Sensorikmarktes.
Rund 300 Mitarbeiter beschäftigt wenglor allein am Standort Tettnang und der Bedarf an qualifiziertem Personal ist kaum zu decken. Unter diesen Gegebenheiten genießen effiziente, hochautomatisierte Produktionskonzepte mit höchster Performance hinsichtlich Output und Qualität oberste Priorität. Wie solche Lösungen in der Praxis aussehen, zeigt eine Roboterzelle, in der Optikmodule für unterschiedliche optoelektronische Sensorbaureihen schnell und präzise montiert werden. Zu den Schlüsselkomponenten der Zelle gehören ein Stäubli TX60L Sechsachs-Roboter, eine Beckhoff TwinCAT3 Soft-SPS sowie ein .NET-Hostprogramm.
Die Besonderheit der Zelle bringt Martin auf den Punkt: „Das Roboterprogramm unterstützt beliebige Anforderungen, die Ausführungsschritte in der SPS sind frei konfigurierbar, die Ausstattung der Zelle hochflexibel – das gibt uns jede Menge Freiheit. Die Anlage kann deshalb nicht nur Linsen justieren, sondern beherrscht auch ein breites Spektrum an Montageapplikationen.“
Derzeit werden in der Zelle ausschließlich Optikmodule für diverse modular konzipierte Sensorbaureihen montiert: Die Variantenvielfalt geht hier nahezu gegen unendlich. Typische Losgrößen liegen bei 100 bis 2.000 Optikmodulen. Analog dazu stehen bis zu fünf Umrüstungen pro Tag an. Aufgrund der Flexibilität der Anlage und der steuerungstechnischen Voraussetzungen mit dem Hostprogramm, aus dem die entsprechenden Prozessabläufe nur abgerufen werden müssen, lässt sich die komplette Zelle in wenigen Minuten umrüsten.
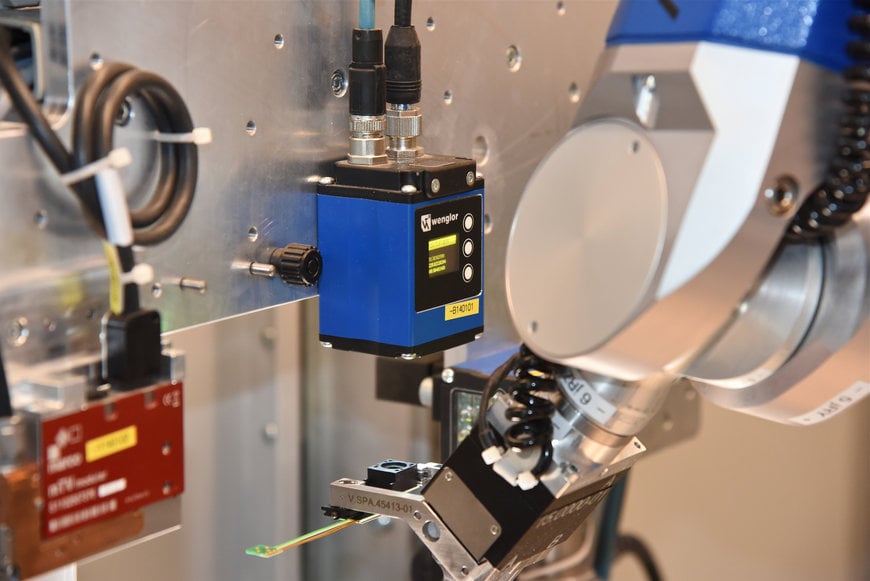
Die Smartkamera erfasst die exakte Position des Optikmoduls im Greifer, um es später mit der geforderten Genauigkeit an der Montageposition ablegen zu können.
Der Montageprozess im Überblick
Einen Großteil der Handhabungsprozesse der drei Einzelteile Optikmodul, Sende- und Empfangslinse, die über Trays bevorratet werden, übernimmt der Stäubli Sechsachser vom Typ TX60L. Das L steht für die Langarmvariante, die dem Roboter eine Reichweite von 920 mm verleiht und so das problemlose Anfahren aller Stationen innerhalb der Zelle ermöglicht.
Der Prozessablauf beginnt mit dem Aufnehmen eines unbestückten Optikmoduls. Der TX60L ist dazu mit einem Greifer ausgestattet, der über IO-Link konfiguriert und angesteuert wird. Da die Lage der Module im Tray nicht exakt definiert ist, fährt der Roboter zunächst zu einer Station, an der die Position des Bauteils über die wenglor Smartkamera weQube erfasst wird. Nur so lässt sich das Modul später mit der geforderten Genauigkeit an der Montageposition ablegen.
Direkt im Anschluss steuert der Roboter eine Station an, die für die Benetzung der Linsenaufnahmen des Moduls mit Klebstoff zuständig ist. Jetzt muss der TX60L das Bauteil nur noch exakt in seiner Aufnahme ablegen und fertig ist Teil eins des Handhabungsprozesses. An seiner Endposition wird das Optikmodul gespannt, kontaktiert und über IO-Link konfiguriert.
„Das Positionieren des Moduls in seiner Aufnahme verlangt vom Roboter hohe Präzision. Wir arbeiten hier im Toleranzbereich von wenigen Hundertstel Millimeter. Der Stäubli Roboter bewerkstelligt diese Genauigkeitsanforderungen mühelos und erledigt die Positionierung schnell und zuverlässig“, so Martin.
Präzisionsarbeit: die Justage der Linsen
Anschließend macht sich der Roboter an die Handhabung von Sende- und Empfangslinse. Die Arbeitsschritte sind dabei identisch: Der TX60L holt jeweils eine Linse ab, fährt zur Smartkamera-Vermessungsstation, die die Lage des Objekts im Greifer ermittelt und legt die Linse an einer Übergabeposition ab.
An dieser Station übernimmt ein hochpräzises Linearsystem die Handhabung und Justage der Linsen im Optikmodul. Trotz der vorbildlichen Präzision des Stäubli Roboters ließ sich diese Aufgabenstellung nicht mit dem Sechsachser lösen. Dazu Martin: „Sende- und Empfangslinse müssen im Optikhalter auf wenige Mikrometer genau justiert werden, was nur mit einem ultrapräzisen Linearsystem möglich ist. Die Justage der Sende- und Empfangslinse ist der wichtigste Schritt innerhalb des Montageprozesses.“
Bei der Positionierung der Linsen setzt der Anbieter auf ein optisches Feedback-System bestehend aus der wenglor-Smartkamera, der SPS, dem Linearsystem und einem 3D-Regelalgorithmus. Befindet sich der Lichtfleck in Größe und Position im vorgegebenen Toleranzfenster, wird der Justage-Algorithmus beendet und der Klebstoff ausgehärtet. Im letzten Schritt nimmt der Stäubli-Roboter das Optikmodul und legt es im Tray ab.
Mit dieser innovativen Produktionstechnologie ist es möglich geworden, dass alle wenglor Sensoren der optoelektronischen PNG//smart-Baureihe identische optische Eigenschaften haben - wovon Kunden des Anbieters in aller Welt profitieren.
Um die Taktzeiten zu verkürzen, ist die Justagestation doppelt ausgeführt. Dank seiner hohen Dynamik kann der Stäubli Roboter die beiden identischen Stationen im Wechsel bedienen. Die komplette Kommunikation zwischen allen Teilnehmern in der Zelle läuft über EtherCAT. Für die Auswahl des Roboters war die EtherCAT-Option deshalb ein Ausschlusskriterium.
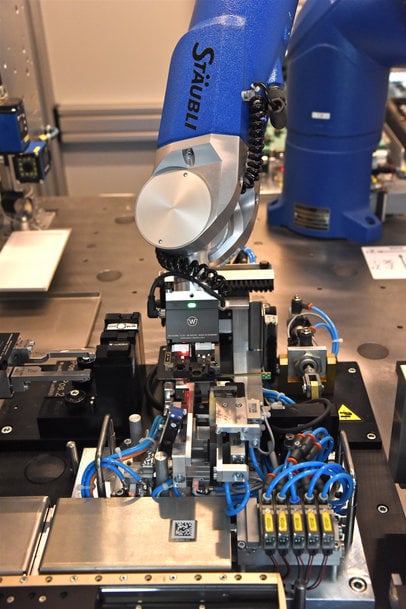
Der TX60L übernimmt einen Großteil der Handhabungsprozesse der drei Einzelteile Optikmodul, Sende- und Empfangslinse, die über Trays bevorratet werden.
Digitalisierung schafft bis dato unerreichte Flexibilität
Während man vielerorts noch von Industrie 4.0 spricht, haben die Entwicklungsingenieure von wenglor die entsprechenden Standards in ihrer Zelle bereits umgesetzt: „Wir stellen die auszuführenden Prozesse quasi über „atomare“ Schritte zusammen, die wir beliebig konfigurieren können. Die Anzahl der einzelnen Schritte kann dabei stark variieren und reicht von 1.000 bei der Linsenjustage bis hin zu 30.000 bei komplexeren Aufgaben. Zu jedem Schritt sind alle Parameter abgespeichert, so dass sich der Prozessablauf bis ins kleinste Detail nachvollziehen lässt“, betont Martin.
Mit der wegweisenden Montagezelle zeigt wenglor, wie sich sowohl Produktivität als auch Flexibilität mit moderner Steuerungstechnik und hochperformanten Robotern auf die Spitze treiben lässt. Die Anlage erfüllt alle Erwartungen und verrichtet ihren Dienst mit maximaler Verfügbarkeit – wenn morgen nicht mehr bei der Linsenjustage, dann vielleicht übermorgen bei der Montage von Steckern. Mehr Investitionssicherheit geht nicht.
www.staubli.com
Fordern Sie weitere Informationen an…