www.konstruktion-industrie.com
04
'23
Written on Modified on
Keba: Maschinenbedienung unter Glas als Wettbewerbsvorteil
Genug Freiraum, die eigenen Features optimal darzustellen und eigene Masken und Layouts zu entwickeln, eine Lösung, die aus einer Hand kommt, eine Innnovation, mit der man sich vom klassischen Standard abhebt.
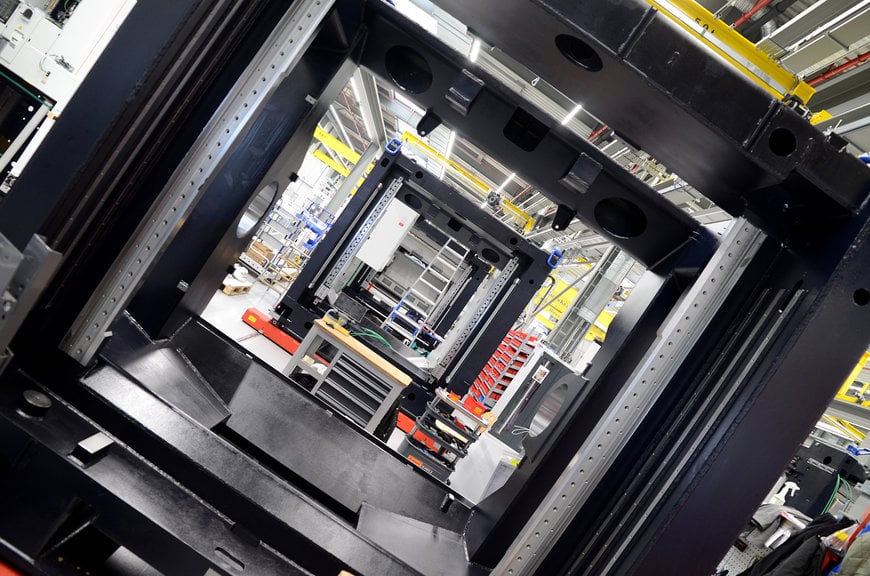
Das war der Rahmen für die Entwicklung eines künftigen HMI bei SW. Das Unternehmen wollte die gesamte Maschinenbedienung „unter Glas“ bringen. Nicht als Vision – sondern als Wettbewerbsvorteil. Wie SW HMI interpretiert und welche Rolle KEBA Industrial Automation bei der Umsetzung des Konzeptes spielt, lesen Sie in diesem Beitrag.
Sie nennen sich Technology People, weil sie Technik begeistert, sie immer wieder den aktuellen Stand des technisch Möglichen in Frage stellen und daraus ableitend neue smarte Fertigungslösungen entwickeln. Die Rede ist von den rund 1400 Mitarbeiter:innen bei SW mit Hauptsitz in Schramberg – Waldmössingen, Deutschland, die wissen, dass die Liebe im Detail liegt. Wie wichtig dem Maschinenbauer Design und Easy to Use als Konzept sind, sieht man, wenn man die hellen Produktionshallen am sehr modernen Standort besucht: Design, konsequent durchgezogen vom Empfang bis zur Verpackung der Maschinen.
Die Produktpalette von SW reicht vom mehrspindligen CNC-Bearbeitungszentrum mit modular aufgebauter Automation über autarke Fertigungszellen bis hin zu kompletten Fertigungssystemen und damit verknüpften Softwarelösungen.
Das Maschinenportfolio von SW umfasst sowohl Einplatzmaschinen für die Bearbeitung komplexer, großvolumiger Werkstücke als auch Zweiplatzmaschinen für die hochpräzise Bearbeitung filigraner Komponenten. Der Einsatz eines Doppelschwenkträgers ermöglicht das hauptzeitparallele Be- und Entladen für minimierte Nebenzeiten und eine höhere Produktivität. Die patentierte Monoblockbauweise gewährleistet für alle SW-Maschinen eine hohe Maschinensteifigkeit. Dabei setzt SW neben Kugelgewindeantrieben auch auf Linearmotorantriebe, welche in den hoch performanten Bearbeitungszentren weltweit zum Einsatz kommen. Durch den Kauf der Bartsch GmbH vor einigen Jahren entstand die SW Automation – was dem Unternehmen erlaubt, komplette Fertigungssysteme anzubieten.
Der Umstieg bzw. Trend weg von Verbrenner-Motoren in Richtung E-Antriebe ist für SW durchweg positiv. Da das Unternehmen kaum Kunden hat, die reine Motorenteile produzieren, können sie beide Bereiche sehr gut abdecken. Der Trend zu E-Mobility hat das Geschäft von SW beflügelt – die größten Neukunden sind diesem Segment zuzuordnen.
Das Unternehmen erzielt seinen Umsatz zu einem Großteil mit Aufträgen aus dem Automotive-Umfeld mit Fokus auf PKW und verbucht seit einigen Jahren ein jährliches Wachstum von mehr als 20%.
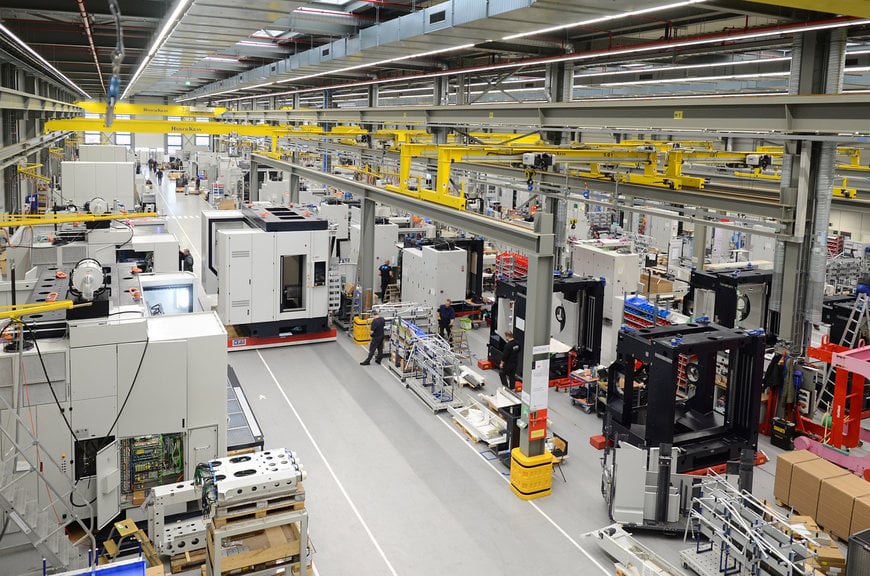
Echte Innovation, die uns vom Markt abhebt
„Wir wollten bzgl. Maschinenbedienung ganz neue Wege gehen, auch unter der Prämisse, dass es Gegenwind von manchen Anwendern geben könnte. Das was wir vorhatten, war ein echter Bruch: wir wollten die gesamte Bedienung unter Glas bringen“, erzählt Peter Siegel, Projektleiter Entwicklung, auf die Frage nach dem Start der Zusammenarbeit mit KEBA. Es folgte eine intensive Marktrecherche, was state-of-the-art war und welche Anbieter welche Technologien im Portfolio hatten oder gerade entwickelten. Bestehende Lieferanten überzeugten nicht.
Die Latte lag besonders hoch. Siegel: „Beim bestehenden Lieferanten hätten wir nicht entwickeln, sondern nur projektieren können, sprich, in ihrem Framework lediglich die verfügbare Funktionalität nutzen, welche leider die Usability sehr eingeschränkt hätte.“ Um diese nachzubilden, wäre eine aufwändige OEM-Programmierung erforderlich geworden, was die Steuerungsressourcen unberechenbar beeinflusst hätte. Siegel weiter: „Erfahrung bzgl. Touch-Anwendungen im Schmutzbereich waren ebenfalls eine Grundvoraussetzung für SW, welche KEBA bereits aus anderen Projekten erfolgreich vorweisen konnte.“
Moritz Ragg, Teamlead User Interface Development bei SW: „KEBA hatte eine konkrete Vorstellung und auch das bessere Konzept. Unser Ziel: möglichst viel in Software abzubilden, damit wir auf den Kunden möglichst flexibel reagieren und ihn so bei der Bedienung unterstützen können, in dem bspw. in der jeweiligen Bediensituation nicht benötigte Inhalte ausgeblendet werden, natürlich unter Einhaltung der normativen Vorgaben.“
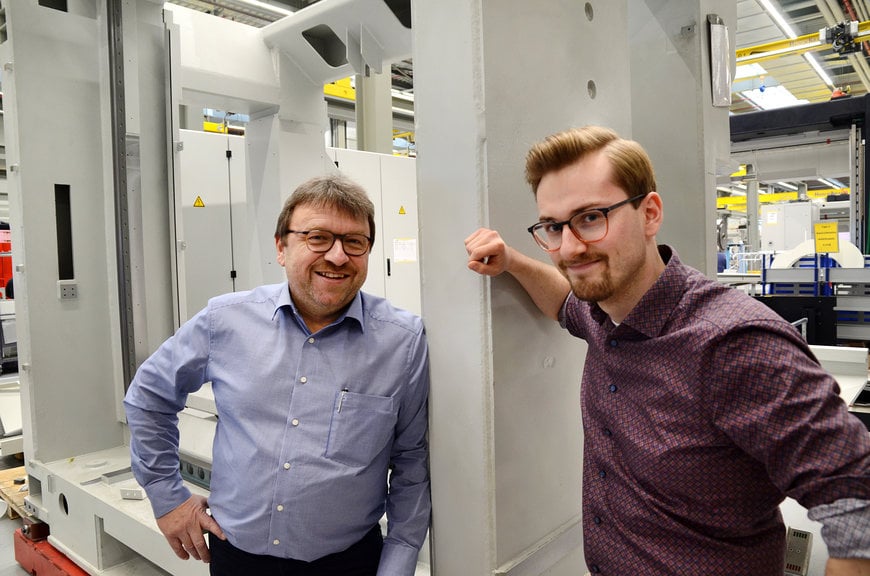
v.l.n.r.: Peter Siegel, Projektleiter Entwicklung SW; Moritz Ragg, Teamlead User Interface Development bei SW.
Überzeugend: KeWheel und Force Feedback
Ausschlaggebend bei der Entscheidung waren das KEBA KeWheel und der Force Feedback-Ansatz. Beim KEBA KeWheel handelt es sich um einen volladaptiven Dreh-Drückknopf als zentrales Bedienelement. Mit dem KeWheel lassen sich Overrides, Handräder, Betriebsartenwahlschalter, Achsverfahrtasten und User Interface Eingabemöglichkeiten in einem Gerät vereinen. Das KeWheel lässt den Bediener über ein breites Spektrum an haptischem Feedback zusätzliche Information über den Maschinenzustand erfühlen. Siegel: „Als wir das KeWheel sahen, wussten wir: das ist genau das, was wir brauchen, ein echtes Alleinstellungsmerkmal – welches es in dieser Funktionalität am Markt noch nirgends gibt.“
Das Force Feedback half dem Maschinenbauer bei der Herausforderung, alles unter Glas zu bringen, vor allem bei den Hürden zum Thema Sicherheit. Ragg: „Da unsere Remote Service-Lösung auch auf die Bedienoberfläche zugreift und man unabhängig davon bei touch-basierten Systemen einfacher Fehlbedienungen auslösen kann, benötigen wir eine technische Absicherung, die z.B. das Bewegen von Achsen nur bei einer bewussten Bedienhandlung durch Überschreiten eines Kraftpunktes während der Betätigung erlaubt." Auch diese Funktion wollte SW ‚unter Glas‘ abgebildet wissen, Hardwarelösungen wie Fußtaster oder eine zusätzliche Taste kamen nicht in Frage. Ragg: „Wir brauchten also eine Lösung unter Glas, mit der wir die Norm einhalten und trotzdem eine Einhand-Bedienung ermöglichen. Force-Feedback-Touch war hier genau die richtige Technologie für uns.“
Fertigungstiefe mit Sicherheit
Zuerst startete das Team mit der Hardware-Entwicklung zusammen mit KEBA und einem Industriedesigner. Für die Konzipierung der Bedienoberfläche setze man dann von Beginn an auf einen UX-Designer, der bereits erfolgreich Projekte mit KEBA durchgeführt hat – so wurde das Gesamtkonzept für die Bedienoberfläche entwickelt.
Ragg: „Wir haben relativ rasch gemerkt, dass das Know-how bei KEBA tief ansetzt, auch was die Fertigung betrifft. Eigenentwicklungen in dieser Größenordnung und mit Flexibilität für Erweiterungen haben wir bei keinem anderen Anbieter gesehen.“ Siegel ergänzt dazu: „Die Tatsache, dass KEBA von der Entwicklung über Layout bis hin zur Fertigung alles selber im Hause macht und dadurch auch in der Lage ist, Re-Designs schnell und flexibel umzusetzen, hat unsere Entscheidung stark beeinflusst.“ Nicht ahnend, was die Industrie in letzter Zeit bzgl. Bauteileverfügbarkeit erfahren hat, legte SW damals schon einen besonderen Wert auf die Fertigungstiefe.
Darüber hinaus war das Team von SW auch stark von Qualitätsfaktoren getrieben. „Mit KEBA haben wir Sicherheit was die Qualität betrifft - weil der Lieferant selber viel in der Hand hat,“ meint Siegel. “Bei anderen Anbietern, die nahezu alle Komponenten und Platinen zukaufen, hängt man sehr stark von Drittanbietern ab. Bei KEBA sind wir im Falle eines Re-Designs wesentlich schneller – und das hat uns rascher als erwartet eingeholt. Bis dato kam es zu keinem Lieferverzug bei Bauteilen“. Als letztes Jahr der bisherige Lieferant plötzlich keine Komponenten aus China bekam, drohte SW eine Lieferunfähigkeit aufgrund fehlender Panels. Siegel: „KEBA hat dann kurzerhand 100 Panels mehr geliefert als im Forecast vorgesehen war, was in etwa 25-30% zusätzlichen Panels entsprach.“
Siegel weiter: „Was wir unbedingt vermeiden wollten, war eine Konstellation bei der es zu viele Partner gibt - also, einer liefert die Hardware, ein anderer die Software, wir packen nochmal was drauf… Das war ein No-Go für uns. Nur die Hardware zu kaufen und intern alles selbst zu machen ging für uns nicht. Da fehlt uns die Zeit, die langjährige Erfahrung und gerade dafür hat KEBA ein gutes Framework angeboten.“
Ragg: „Die komplette Workbench, um so eine Bedienoberfläche zu designen, wurde ja von KEBA selbst entwickelt und zur Verfügung gestellt. Andere Anbieter sind selber auch nur Kunde bei Software-Unternehmen. Im Problemfall hätte das aber den Nachteil, dass die Lösungsfindung schwieriger wäre - bei KEBA haben wir einen Ansprechpartner für die gesamte Technologie.“
Die Zusammenarbeit: schnell, unkompliziert und auf Augenhöhe
„Natürlich gibt’s in jeder Geschäftsbeziehung Höhen und Tiefen, auch mal Differenzen, wo man mal nicht dieselbe Meinung hat. Aber wenn ich die Zusammenarbeit mit KEBA Industrial Automation beschreiben müsste, ist es vor allem eine sehr dynamische“, betont Ragg. „Häufig kommen im Entwicklungsprozess Hürden hervor, die vorher keiner gesehen hat. Wenn man bei KEBA so ein Problem anspricht, geht es schnell an die Lösungsfindung. Bei anderen Anbietern kann hier auch schnell viel Zeit und Mühe vergehen, bis man da mal mit Entscheidungsträgern über neue Ansätze sprechen kann. Bis es zur Umsetzung kommt, dauert es mitunter noch länger… Bei KEBA haben wir sowas nicht.“ Siegel ergänzt: „Gerade bei Änderungen in der Entwicklungsumgebung erwirken wir rasch einen Change-Request. Und in der darauffolgenden Version sind Funktionalitäten dann auch schon umgesetzt“.
Was den beiden in der Zusammenarbeit mit KEBA noch auffällt, sind die kurzen und direkten Kommunikationswege und die Agilität bei der Herangehensweise. Siegel: „Die Entwickler stimmen sich unter einander schnell ab. Man kann seine Fragen, Bedenken, Vorschläge direkt vorbringen und stößt auf offene Ohren. Das ist sicher einer der Punkte, der das schnelle Vorankommen im Projekt erlaubt hat. Man hat direkt mit den Leuten zu tun, die das Projekt vorantreiben und an der Umsetzung beteiligt sind. Es gibt keine Zwischenpersonen.“
„Der Unterschied zu anderen Anbietern ist der direkte Austausch mit den Entwicklern,“ so Ragg. „Vor kurzen saß ich direkt mit den Entwicklern von KEBA zusammen, das hab ich woanders in der Form noch nie geschafft.“ Dass diese Art der Zusammenarbeit das Prädikat ‚agil‘ verdient, zeigt sich auch in der Dynamik: zwischen dem ersten „Pinselstrich am Zeichenbrett“ und der Vorstellung des Prototypen der Bedienoberfläche vergingen gerade mal sechs Monate.
Was ebenfalls zur Dynamik beiträgt, ist die Tatsache, dass KEBA Industrial Automation keine Standardlösung aus der Schublade liefert, sondern auf den jeweiligen Kunden zugeschnittene Ansätze entwickelt. Siegel: „KEBA hat im Projekt unsere Anwendung im Fokus und muss nicht, wie es bei anderen Automatisierungsanbietern der Fall ist, wenn sie Änderungen machen, zuerst gegen ihr System und all ihre anderen bisherigen Anwendungen testen, da jede Änderung zu ihrem ganzen Leistungsumfang passen muss und nicht bereits Existierendem widersprechen darf. Das macht die Entwicklung viel langsamer.“
www.keba.com
Fordern Sie weitere Informationen an…