www.konstruktion-industrie.com
04
'11
Written on Modified on
Prüfung von elektrischen Motoren für Automotive-Anwendungen
Für seine Prüfstände in Labor und Fertigung entschied sich Unus International für die schlüsselfertige MEROBEL Lösung
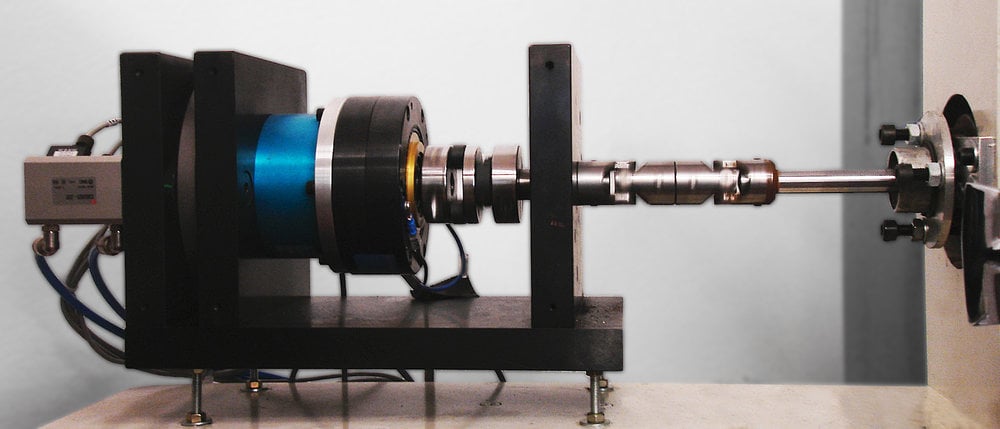
Unus International fertigt 12, 24 und 48 V Gleichstrommotoren, größtenteils eingesetzt als servomechanisches Equipment für die Automobilindustrie und die industrielle Fertigungstechnik.
Gegründet in den 70er Jahren in Padua, verlegte Unus im Jahr 1995 seinen Hauptsitz nach Rival di Piangia (Venedig). Das Unternehmen beschäftigt derzeit rund 60 Mitarbeiter, mit einer Produktionskapazität von über 2.000.000 Stück pro Jahr.
Dazu gehören Motoren und Getriebemotoren für folgende Automobilanwendungen:
- Einrichtungen für Fenster, Schiebedächer und Sonnenblenden
- Bewegungs- und Ausrichtungsmechanismen für die Sitzverstellung
- Lenkradeinheit
- Implementierte Automatikgetriebe
Die vielfältige Produktpalette umfasst zudem Motor-basierte Ausrüstungen für andere Industriezweige wie beispielsweise die Kontrolle von Schiebetüren, Überbauten, für Tore und Automatisierung im Allgemeinen.
Die Ingenieure von Unus entwickeln neue Produkte zugeschnitten auf die jeweiligen Kundenanforderungen.
Hohe technische Fachkompetenz und Flexibilität sind die wichtigsten Unternehmenswerte. Diese Werte ermöglichen eine Reduzierung der Zeiten für die Entwicklung, die Erstellung des Prototyps und die Herstellung von Mustern. Diese Organisation gewährleistet eine schnelle Reaktion auf eine Vielzahl von Marktbedürfnissen und ein schnelles Time-to-Market. „Unsere Mission ist es, Produkte herzustellen, die genau auf die Bedürfnisse unserer Kunden zugeschnitten sind; hierbei sind ein hoher technischer Standard und hohe Qualitätsansprüche zentrale Themen“, sagte Ingenieur Massimo Melato, General Manager von Usus International. „Ausgangspunkt hierfür sind unsere Qualitäts-Richtlinien und unsere ständigen Bestrebungen im Bereich R&D, aber auch Design, Produktion und Unternehmensorganisation im Allgemeinen, mit dem Ziel, die Kundenzufriedenheit stetig zu verbessern.“ „Die hervorragenden Ergebnisse, die wir im In- und Ausland mit unseren High-Tech-Produkten erzielen konnten, bestätigen, dass wir damit auf dem richtigen Weg sind. Wir arbeiten kontinuierlich daran, unsere Wettbewerbsfähigkeit und unsere Qualität zu steigern. Im Übrigen werden Unus Motoren und Getriebemotoren als Erstausrüstung bei großen deutschen Autoherstellern sowie den wichtigsten Herstellern von Automatisierungssystemen eingesetzt.“
Die strategische Bedeutung von Testverfahren
Verantwortlich für den Erfolg des Unternehmens sind neben der technologischen Kompetenz die hohe Zuverlässigkeit und die Qualität in der Produktion.
Unus International gehört zu den 100 erfolgreichsten italienischen Unternehmen, die im dritten Eurispes Bericht aufgelistet sind. Um eine derart hohe Kompetenz sicherstellen zu können, kommt der Produktprüfung eine äußerst strategische Bedeutung zu. (während der Produktion, aber auch bereits in der Laborphase und während des Entwicklungsprozesses).
Insbesondere für die 100-Prozent-Prüfung der Motoren für die Automobilindustrie wurden spezialisierte Prüfstände erstellt. „Sie wurden vor allem zum Testen motorisierter Fenster, der Sitzverstellung, Schiebedächer, der Lenkradeinstellung und dem „tendon movement“ eingerichtet, sagt Dipl-Ing. Melato. „Momentan entwickeln wir einen Motor, der den Kompressor zur Luftfederung eines Autos steuert.“
Die zugehörigen Prüfstände wurden nicht für eine spezielle Kundenapplikation entwickelt. Unus hat die Richtlinien vieler Automobilhersteller gesammelt und eine Vielzahl von Prüfständen entwickelt, die in der Lage sind, diese Spezifikationen zu erfüllen.
„Lösungen, die man üblicherweise auf dem Markt antrifft, sind dafür ausgelegt, eine möglichst breite Palette von Anwendungen abzudecken“, sagt Dipl.-Ing. Melato. „Sie entsprechen jedoch oftmals nicht ganz unseren spezifischen Bedürfnissen. Dadurch, dass wir die Prüfstände im eigenen Unernehmen bauen und die Steuerungssoftware selbst entwickeln, sind sie exakt auf unsere Anforderungen ausgerichtet und auf die Bedürfnisse unserer Kunden.“
Beim Herstellungsprozess wird jeder Motor getestet hinsichtlich der wichtigsten Betriebsparameter und des Geräuschpegels. „Um bei diesen Tests weiter voranzukommen, haben wir derzeit vier Prüfstände mit MEROBEL-Bremsen ausgestattet“, sagt Dipl.-Ing. Melato. „Die Prüfzyklen betragen fünf und zehn Minuten, abhängig vom jeweiligen Motortyp. Täglich werden etwa 8000 Produkte getestet.“
Die anderen fünf mit MEROBEL-Bremsen ausgestatteten Prüfstände befinden sich im Labor. Hier werden Zuverlässigkeit und Lebensdauer der Motoren und Getriebemotoren geprüft sowie Materialermüdungstests durchgeführt. Bei diesen Tests ist die Prüfungsdauer um einiges länger. Einige Langzeittests mit ausgedehnten Zyklen und Alterungssimulation durch Beaufschlagung mit Hitze in Klimakammern können bis zu 60 Tage dauern.
Es handelt sich hier also um zwei ganz unterschiedliche Applikationen.
„Im Labor werden die Prüfungen in erster Linie durchgeführt, um die Arbeitszyklen der Motoren zu simulieren mit unterschiedlichen Lastwechseln (d.h. mit unterschiedlichen Drehmomenten) und unterschiedlichen Umweltbedingungen (einschließlich thermischer Belastungen in einem Temperaturbereich zwischen -40 bis zu +90 Grad C und verschiedenen Werten relativer Feuchte) für eine bestimmte Anzahl von Zyklen oder über die gesamte Lebensdauer des Motors“, sagt Dipl. Ing. Melato. „Wir benutzen einen klar definieren Arbeitszyklus nach den Vorgaben des Kunden.“ Während der Testphase wird jeder einzelne Parameter kontinuierlich überwacht und aufgezeichnet (Stromaufnahme, Drehzahl und Temperatur).
Entspricht ein Motor nicht den geforderten Qualifikationen oder Standards (z.B. Überhitzung, vorzeitiger Verschleiß der Bürsten oder Versagen einer Komponente) werden die Gründe des Versagens analysiert und die erforderlichen Verbesserungsmaßnahmen eingeleitet. Nach der erfolgten Modifikation wird der Test ein zweites Mal wiederholt, um die geforderte Motorqualität zu erreichen.
Die eindeutige Zielsetzung besteht darin, alle kundenseitig geforderten Spezifikationen zu erfüllen und eine Fertigung mit null Ausschuss zu realisieren.
Das gleiche Verfahren wird auch einmal pro Jahr für Produkttests angewandt, um zu überprüfen, ob sich zwischenzeitlich nichts verändert hat.
Robuste und zuverlässige EMP-Bremsen – Benutzerfreundliche Closed-Loop-Regler
Zur Simulation der variablen Last, der der Motor während seiner gesamten Lebensdauer ausgesetzt ist, entschied sich Unus für eine Komplettlösung basierend auf MEROBEL-Komponenten. Unterstützt wurde Unus hierbei von der vor Ort ansässigen Tochtergesellschaft ANDANTEX Spa.
Bei den ausgewählten Komponenten handelt es sich um EMP Bremsen (Typ FAT120), einem Drehmomentsensor (Typ TRS50) und einem Closed-Loop-Regler (Typ DGT300).
„ANDANTEX beriet uns über den Einsatz der MEROBEL-Bremsen bei dieser Anwendung sowie über die Steuereinheit und die verschiedenen für diese Anwendung erforderlichen Parameter, sagt Dipl. Ing. Melato. Während der gesamten Entwicklungsphase dieser Applikation konnte mit ANDANTEX eine echte Partnerschaft aufgebaut werden. Insbesondere der Austausch von Fachwissen mit unseren Software-Entwicklern für kundenspezifische Applikationen war entscheidend für die erfolgreiche Umsetzung unserer finalen, den Kundenbedürfnissen vollständig angepassten, Testsysteme.“
Die breite Angebotspalette an Lösungen von MEROBEL umfasst High-Tech-Aktoren wie die EMP-Bremsen und Kupplungen, digitale Steuerungen, Sensoren und Wandler. Das spezifische Unternehmens-Know-how ermöglicht es, optimale Lösungen für fast jede Applikation mit variablem Drehmoment anzubieten, entsprechend den spezifischen Anforderungen.
MEROBELs EMP (Elektromagnetische Partikel)-Serie von Bremsen und Kupplungen besteht aus zwei konzentrischen Rotoren, dem äußeren und dem inneren, die durch einen Spalt voneinander getrennt sind, in dem sich die magnetischen Partikel befinden. Abweichungen des Magnetfeldes im Spalt (hervorgerufen durch einen über die Spule eingespeisten variablen Gleichstrom) bewirken eine variable Fluidität der magnetischen Partikel, was zu einer gleichmäßigen und variablen Kopplung zwischen den beiden Rotoren (mit variablem Drehmoment) führt.
Diese spezielle Technologie gewährleistet ein stabiles Drehmoment, das reproduzierbar und unabhängig ist von der Drehgeschwindigkeit und sich einfach auf eine niedrige Gleichstromstärke einstellen lässt.
Zu den wichtigsten Merkmalen der MEROBEL EMP Bremsen und Kupplungen gehört zum einen die Proportionalität zwischen dem bereitgestellten Strom und dem zur Verfügung stehenden Drehmoment, die Unabhängigkeit zwischen Drehmoment und Geschwindigkeit, der beidseitige Betrieb, der sehr geringe Verschleiß und der geräuschlose Betrieb.
Darüber hinaus erfordern MEROBEL EMP Bremsen und Kupplungen einen geringen Wartungsaufwand, sie bieten schnelle Reaktionszeiten (10 bis 50 ms), niedrige elektrische Leistungsaufnahme, ein lineares Ansprechverhalten. Sie verfügen außerdem über sehr einfache Fernbedienungseigenschaften und lassen sich äußerst einfach in jede Art von Testsystem integrieren.
„Wir waren sehr zufrieden mit den MEROBEL-Produkten und der Unterstützung durch ANDANTEX“, fasst Dipl. Ing. Melato zusammen. “Wir hatten die MEROBEL Bremsen zuerst bei den Prüfständen in der Produktion installiert. Und obwohl die Anforderungen beim Laboreinsatz viel höher sind, haben wir den Einsatz der Bremsen auf die Laborprüfstände ausgeweitet – mit großem Erfolg.“
REDEX ANDANTEX mit Hauptsitz in Ferrières, Frankreich, beschäftigt 320 Personen und verfügt über drei Produktionsstandorte in Europa und Nordamerika. Mehr als 75 Prozent des Umsatzes wird außerhalb Frankreichs erwirtschaftet.
Technologischer Fortschritt, eine Verpflichtung zu Qualität und ein außergewöhnlicher technischer Support sind die Grundwerte der REDEX ANDANTEX.
Gegründet in den 70er Jahren in Padua, verlegte Unus im Jahr 1995 seinen Hauptsitz nach Rival di Piangia (Venedig). Das Unternehmen beschäftigt derzeit rund 60 Mitarbeiter, mit einer Produktionskapazität von über 2.000.000 Stück pro Jahr.
Dazu gehören Motoren und Getriebemotoren für folgende Automobilanwendungen:
- Einrichtungen für Fenster, Schiebedächer und Sonnenblenden
- Bewegungs- und Ausrichtungsmechanismen für die Sitzverstellung
- Lenkradeinheit
- Implementierte Automatikgetriebe
Die vielfältige Produktpalette umfasst zudem Motor-basierte Ausrüstungen für andere Industriezweige wie beispielsweise die Kontrolle von Schiebetüren, Überbauten, für Tore und Automatisierung im Allgemeinen.
Die Ingenieure von Unus entwickeln neue Produkte zugeschnitten auf die jeweiligen Kundenanforderungen.
Hohe technische Fachkompetenz und Flexibilität sind die wichtigsten Unternehmenswerte. Diese Werte ermöglichen eine Reduzierung der Zeiten für die Entwicklung, die Erstellung des Prototyps und die Herstellung von Mustern. Diese Organisation gewährleistet eine schnelle Reaktion auf eine Vielzahl von Marktbedürfnissen und ein schnelles Time-to-Market. „Unsere Mission ist es, Produkte herzustellen, die genau auf die Bedürfnisse unserer Kunden zugeschnitten sind; hierbei sind ein hoher technischer Standard und hohe Qualitätsansprüche zentrale Themen“, sagte Ingenieur Massimo Melato, General Manager von Usus International. „Ausgangspunkt hierfür sind unsere Qualitäts-Richtlinien und unsere ständigen Bestrebungen im Bereich R&D, aber auch Design, Produktion und Unternehmensorganisation im Allgemeinen, mit dem Ziel, die Kundenzufriedenheit stetig zu verbessern.“ „Die hervorragenden Ergebnisse, die wir im In- und Ausland mit unseren High-Tech-Produkten erzielen konnten, bestätigen, dass wir damit auf dem richtigen Weg sind. Wir arbeiten kontinuierlich daran, unsere Wettbewerbsfähigkeit und unsere Qualität zu steigern. Im Übrigen werden Unus Motoren und Getriebemotoren als Erstausrüstung bei großen deutschen Autoherstellern sowie den wichtigsten Herstellern von Automatisierungssystemen eingesetzt.“
Die strategische Bedeutung von Testverfahren
Verantwortlich für den Erfolg des Unternehmens sind neben der technologischen Kompetenz die hohe Zuverlässigkeit und die Qualität in der Produktion.
Unus International gehört zu den 100 erfolgreichsten italienischen Unternehmen, die im dritten Eurispes Bericht aufgelistet sind. Um eine derart hohe Kompetenz sicherstellen zu können, kommt der Produktprüfung eine äußerst strategische Bedeutung zu. (während der Produktion, aber auch bereits in der Laborphase und während des Entwicklungsprozesses).
Insbesondere für die 100-Prozent-Prüfung der Motoren für die Automobilindustrie wurden spezialisierte Prüfstände erstellt. „Sie wurden vor allem zum Testen motorisierter Fenster, der Sitzverstellung, Schiebedächer, der Lenkradeinstellung und dem „tendon movement“ eingerichtet, sagt Dipl-Ing. Melato. „Momentan entwickeln wir einen Motor, der den Kompressor zur Luftfederung eines Autos steuert.“
Die zugehörigen Prüfstände wurden nicht für eine spezielle Kundenapplikation entwickelt. Unus hat die Richtlinien vieler Automobilhersteller gesammelt und eine Vielzahl von Prüfständen entwickelt, die in der Lage sind, diese Spezifikationen zu erfüllen.
„Lösungen, die man üblicherweise auf dem Markt antrifft, sind dafür ausgelegt, eine möglichst breite Palette von Anwendungen abzudecken“, sagt Dipl.-Ing. Melato. „Sie entsprechen jedoch oftmals nicht ganz unseren spezifischen Bedürfnissen. Dadurch, dass wir die Prüfstände im eigenen Unernehmen bauen und die Steuerungssoftware selbst entwickeln, sind sie exakt auf unsere Anforderungen ausgerichtet und auf die Bedürfnisse unserer Kunden.“
Beim Herstellungsprozess wird jeder Motor getestet hinsichtlich der wichtigsten Betriebsparameter und des Geräuschpegels. „Um bei diesen Tests weiter voranzukommen, haben wir derzeit vier Prüfstände mit MEROBEL-Bremsen ausgestattet“, sagt Dipl.-Ing. Melato. „Die Prüfzyklen betragen fünf und zehn Minuten, abhängig vom jeweiligen Motortyp. Täglich werden etwa 8000 Produkte getestet.“
Die anderen fünf mit MEROBEL-Bremsen ausgestatteten Prüfstände befinden sich im Labor. Hier werden Zuverlässigkeit und Lebensdauer der Motoren und Getriebemotoren geprüft sowie Materialermüdungstests durchgeführt. Bei diesen Tests ist die Prüfungsdauer um einiges länger. Einige Langzeittests mit ausgedehnten Zyklen und Alterungssimulation durch Beaufschlagung mit Hitze in Klimakammern können bis zu 60 Tage dauern.
Es handelt sich hier also um zwei ganz unterschiedliche Applikationen.
„Im Labor werden die Prüfungen in erster Linie durchgeführt, um die Arbeitszyklen der Motoren zu simulieren mit unterschiedlichen Lastwechseln (d.h. mit unterschiedlichen Drehmomenten) und unterschiedlichen Umweltbedingungen (einschließlich thermischer Belastungen in einem Temperaturbereich zwischen -40 bis zu +90 Grad C und verschiedenen Werten relativer Feuchte) für eine bestimmte Anzahl von Zyklen oder über die gesamte Lebensdauer des Motors“, sagt Dipl. Ing. Melato. „Wir benutzen einen klar definieren Arbeitszyklus nach den Vorgaben des Kunden.“ Während der Testphase wird jeder einzelne Parameter kontinuierlich überwacht und aufgezeichnet (Stromaufnahme, Drehzahl und Temperatur).
Entspricht ein Motor nicht den geforderten Qualifikationen oder Standards (z.B. Überhitzung, vorzeitiger Verschleiß der Bürsten oder Versagen einer Komponente) werden die Gründe des Versagens analysiert und die erforderlichen Verbesserungsmaßnahmen eingeleitet. Nach der erfolgten Modifikation wird der Test ein zweites Mal wiederholt, um die geforderte Motorqualität zu erreichen.
Die eindeutige Zielsetzung besteht darin, alle kundenseitig geforderten Spezifikationen zu erfüllen und eine Fertigung mit null Ausschuss zu realisieren.
Das gleiche Verfahren wird auch einmal pro Jahr für Produkttests angewandt, um zu überprüfen, ob sich zwischenzeitlich nichts verändert hat.
Robuste und zuverlässige EMP-Bremsen – Benutzerfreundliche Closed-Loop-Regler
Zur Simulation der variablen Last, der der Motor während seiner gesamten Lebensdauer ausgesetzt ist, entschied sich Unus für eine Komplettlösung basierend auf MEROBEL-Komponenten. Unterstützt wurde Unus hierbei von der vor Ort ansässigen Tochtergesellschaft ANDANTEX Spa.
Bei den ausgewählten Komponenten handelt es sich um EMP Bremsen (Typ FAT120), einem Drehmomentsensor (Typ TRS50) und einem Closed-Loop-Regler (Typ DGT300).
„ANDANTEX beriet uns über den Einsatz der MEROBEL-Bremsen bei dieser Anwendung sowie über die Steuereinheit und die verschiedenen für diese Anwendung erforderlichen Parameter, sagt Dipl. Ing. Melato. Während der gesamten Entwicklungsphase dieser Applikation konnte mit ANDANTEX eine echte Partnerschaft aufgebaut werden. Insbesondere der Austausch von Fachwissen mit unseren Software-Entwicklern für kundenspezifische Applikationen war entscheidend für die erfolgreiche Umsetzung unserer finalen, den Kundenbedürfnissen vollständig angepassten, Testsysteme.“
Die breite Angebotspalette an Lösungen von MEROBEL umfasst High-Tech-Aktoren wie die EMP-Bremsen und Kupplungen, digitale Steuerungen, Sensoren und Wandler. Das spezifische Unternehmens-Know-how ermöglicht es, optimale Lösungen für fast jede Applikation mit variablem Drehmoment anzubieten, entsprechend den spezifischen Anforderungen.
MEROBELs EMP (Elektromagnetische Partikel)-Serie von Bremsen und Kupplungen besteht aus zwei konzentrischen Rotoren, dem äußeren und dem inneren, die durch einen Spalt voneinander getrennt sind, in dem sich die magnetischen Partikel befinden. Abweichungen des Magnetfeldes im Spalt (hervorgerufen durch einen über die Spule eingespeisten variablen Gleichstrom) bewirken eine variable Fluidität der magnetischen Partikel, was zu einer gleichmäßigen und variablen Kopplung zwischen den beiden Rotoren (mit variablem Drehmoment) führt.
Diese spezielle Technologie gewährleistet ein stabiles Drehmoment, das reproduzierbar und unabhängig ist von der Drehgeschwindigkeit und sich einfach auf eine niedrige Gleichstromstärke einstellen lässt.
Zu den wichtigsten Merkmalen der MEROBEL EMP Bremsen und Kupplungen gehört zum einen die Proportionalität zwischen dem bereitgestellten Strom und dem zur Verfügung stehenden Drehmoment, die Unabhängigkeit zwischen Drehmoment und Geschwindigkeit, der beidseitige Betrieb, der sehr geringe Verschleiß und der geräuschlose Betrieb.
Darüber hinaus erfordern MEROBEL EMP Bremsen und Kupplungen einen geringen Wartungsaufwand, sie bieten schnelle Reaktionszeiten (10 bis 50 ms), niedrige elektrische Leistungsaufnahme, ein lineares Ansprechverhalten. Sie verfügen außerdem über sehr einfache Fernbedienungseigenschaften und lassen sich äußerst einfach in jede Art von Testsystem integrieren.
„Wir waren sehr zufrieden mit den MEROBEL-Produkten und der Unterstützung durch ANDANTEX“, fasst Dipl. Ing. Melato zusammen. “Wir hatten die MEROBEL Bremsen zuerst bei den Prüfständen in der Produktion installiert. Und obwohl die Anforderungen beim Laboreinsatz viel höher sind, haben wir den Einsatz der Bremsen auf die Laborprüfstände ausgeweitet – mit großem Erfolg.“
REDEX ANDANTEX mit Hauptsitz in Ferrières, Frankreich, beschäftigt 320 Personen und verfügt über drei Produktionsstandorte in Europa und Nordamerika. Mehr als 75 Prozent des Umsatzes wird außerhalb Frankreichs erwirtschaftet.
Technologischer Fortschritt, eine Verpflichtung zu Qualität und ein außergewöhnlicher technischer Support sind die Grundwerte der REDEX ANDANTEX.
Fordern Sie weitere Informationen an…