www.konstruktion-industrie.com
21
'11
Written on Modified on
Intelligent verbunden
Innovative Werkstoffe in der Automobilindustrie erfordern neue Ansätze bei den Zulieferern - Hetal-Werke finden Antwort auf den Kosten-/Qualitäts-Spagat
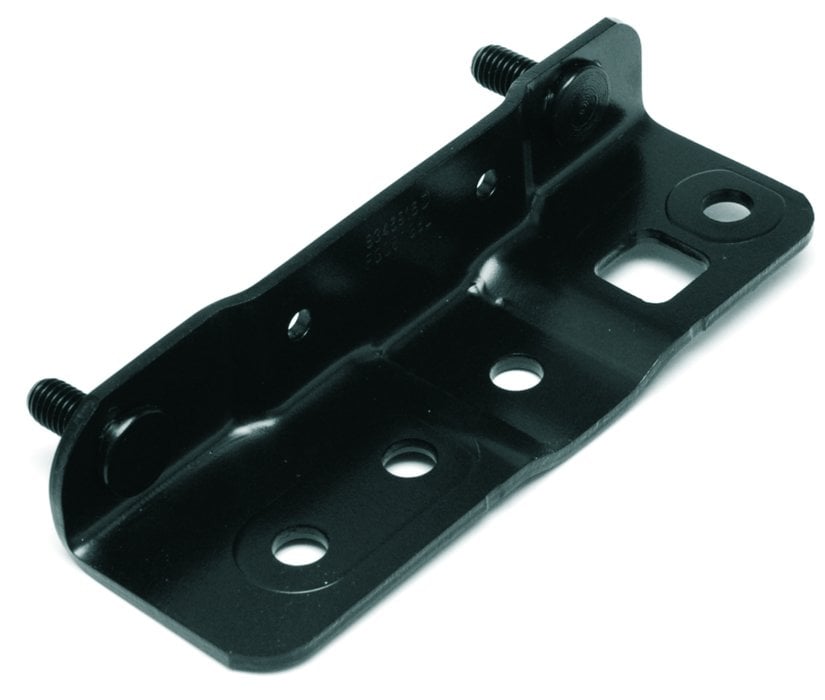
Diese Marktkräfte sind auch für die Hetal-Werke aus Alpirsbach im Schwarzwald nicht neu. Als renommierter und anerkannter Lieferant von anwendungsspezifischen Beschlägen und Gelenkbaugruppen im Bereich Sitzverstellung (Bild 1) für die Automobilindustrie steht das Traditionsunternehmen vor der Herausforderung, die Komplexitätskosten in der Verbindungstechnik nachhaltig zu senken, ohne Abstriche bei der Qualität machen zu müssen.
Kostenreduktionen über den Prozess möglich
Systematisch werden die einzelnen Kostentreiber über die gesamte Wertschöpfungskette von der Konstruktion bis zur Fertigung identifiziert und analysiert. „Die Hersteller binden uns ganz bewusst immer früher in den Prozess ein“, umreißt Hetal-Werke Vertriebsleiter Automotive, Reinhard Gruber, die Herausforderung (Bild 2). „Entsprechend entwickeln flexible Mittelständler wie die HETAL-Werke ihre Beratungskompetenz zunehmend weiter – was sich auch an der Qualität der Mitarbeiter ablesen lässt.“
Studien weisen nach, dass die Entscheidung bei der Auswahl der einzusetzenden Verbindungstechnologie die Kosten um bis zu 80 Prozent reduzieren kann. Im Rahmen eines neuen Projektes sucht die Mannschaft um Gruber aktuell eine kostengünstige, aber gleichzeitig qualitativ adäquate Verbindungsalternative zum Schweißbolzen. Angesichts der Tendenzen in Richtung Leichtbau und dem zunehmenden Einsatz hochfester Stähle erwartet das Unternehmen, dass bereits in der nächsten Fahrzeuggeneration Werkstoffe eingesetzt werden könnten, bei denen konventionelle Schweißtechnik nicht greift. Gleichzeitig steigen die Anforderungen an die Verdrehsicherheit und die Vibrationsbeständigkeit an den Verbindungsschnittstellen.
Einpressen statt schweißen
Bei der Marktrecherche wurde man auf die ATP®-Einpressbolzen der ARNOLD Umformtechnik GmbH aus dem württembergischen Forchtenberg aufmerksam. Das ATP®-ARNOLD TriPress ist ein dreieckförmiges Schnellbindersystem, das in Kunststoffe und Leichtmetalle eingepresst werden kann (Bild 3). Durch das Einpressen können zwei Bauteile schnell und wirtschaftlich miteinander verbunden werden. Die Anzahl der Fertigungsschritte wird radikal verringert, die Durchlaufzeiten verkürzt und die Qualität der Verbindungen gleichzeitig erhöht. Durch den Einsatz von ATP® können sich die Montagezeiten nach Erfahrungen von Detlev Schwarzer, Key Account Manager bei ARNOLD Umformtechnik, um bis zu 75 Prozent reduzieren. Zudem können – im Gegensatz zur geschweißten Variante – auch vorverzinkte Oberflächen verbunden werden (Bild 4).
Der trilobulare ATP®-Bolzen verbindet schon durch seinen Aufbau diverse Produktvorteile in sich. Umlaufende Sperrrillen auf dem dreiecksförmigen Schaft generieren eine hohe Auszugsfestigkeit, was zu einer erhöhten Qualität beim Vermeiden von Geräuschen an der Verbindungsstelle führt.
Der dreieckförmige Schaft und der achsparallele Rändel ermöglichen eine hohe Verdrehsicherheit. Die Verbindung ist unlösbar und unabhängig von Vorspannkräften. Das hohe Verdrehmoment resultiert aus dem trilobularen Aufbau des Bolzens, der – konsequent mittig integriert – an drei Montagepunkten verdrehsicher im Vorloch fixiert ist. Gleichzeitig erfordert die spezifische Form des Bolzens geringe Einpresskräfte. Die Montage des Bolzens ist mit konventionellen und kostengünstigen Betriebsmitteln wie Hydraulik- oder Pneumatikpressen durchzuführen. Weggesteuertes Einpressen ist ebenfalls möglich.
Thermische Belastungen entfallen
Erfahrungsgemäß müssen beim Schweißen weitere Arbeitsvorgänge einkalkuliert werden. Die beim Schweißvorgang kaum zu eliminierenden Rückstände gehören ebenso beseitigt, wie Verunreinigungen an der Oberfläche. Der Verzicht auf thermische Belastungen, die beim Schweißvorgang den Blechwerkstoff verändern und direkt an der Verbindungsstelle die Festigkeit reduzieren können, verringert den Aufwand für Materialprüfungen. Dokumentationen der Prozessabläufe bestätigen die Kalkulation: Allein bei der Prüfung entfallen 50 Prozent der Kosten. Der Bedarf an Zusatzwerkstoffen entfällt, was sich in der Energiebilanz des Unternehmens positiv niederschlägt. Umweltbelastungen wie Geräusche oder Dämpfe liegen ebenso wenig an, wie die damit verbundenen Schutzmaßnahmen. Zusätzlich wird der Anteil am Ausschuss in der Produktion auf Grund der rein mechanischen Bearbeitung nachhaltig gesenkt.
Fazit:
Angesichts der zu erwartenden Entwicklung, dass Leichtbauwerkstoffe und hochfeste Stähle noch stärker als bislang in die Automobilproduktion einziehen werden, sind die Aktivitäten der Hetal-Werke nur schlüssig, sich mit neuen Verbindungskonzepten auseinander zu setzen. Die Verwendung trilobularer Bolzen wie des ATP® TriPress von Arnold Umformtechnik wird ein weiterer Schritt des Mittelständlers sein, den Kosten-/Qualitäts-Spagat zu schaffen und sein Beratungsprofil beim Auftraggeber weiter zu schärfen.
Fordern Sie weitere Informationen an…