www.konstruktion-industrie.com
23
'13
Written on Modified on
Materialien in der Entwicklung
Dieter Steudtner, Sales Manager bei Morgan Advanced Materials gibt Entwicklern und Herstellern einen Einblick in moderne Keramikmaterialien und deren Eigenschaften.
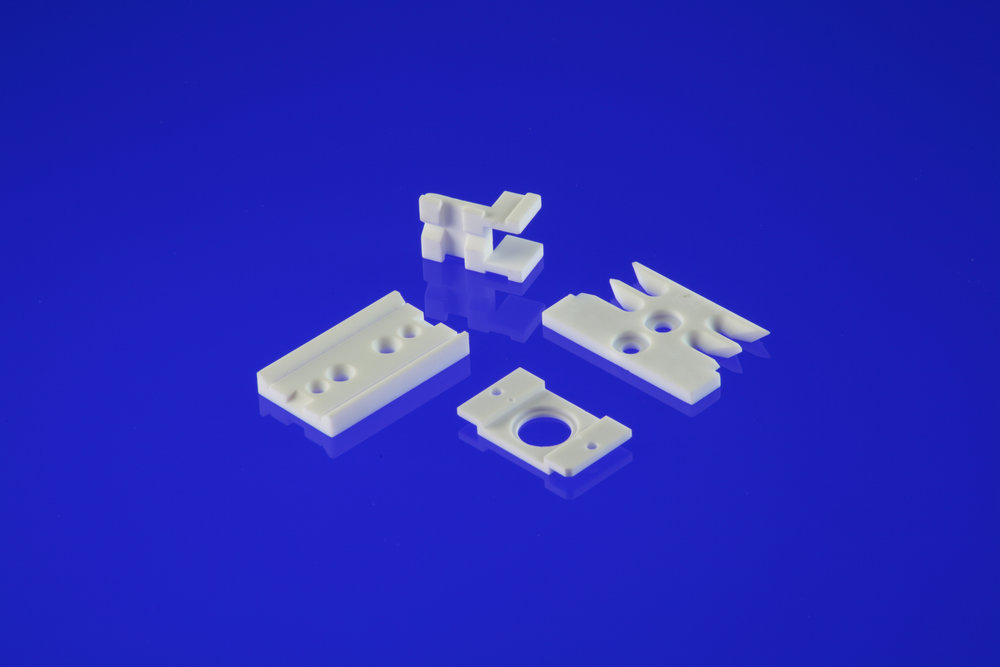
Keramische Werkstoffe überzeugen mit stabilen physikalischen, chemischen und elektrischen Eigenschaften, Einsatz bei hohen Temperaturen, stabil bei Biege- und Dehnkräften, Korrosion, Verschleiß sowie bei hohen Spannungen und Strömen resistent zu sein. Dies eröffnet Einsatzmöglichkeiten für Hersteller in zahlreichen Industriezweigen wie Transport, Gesundheitswesen, Elektronik, wissenschaftlichem Equipment und Halbleiterprozessen.
Moderne keramische Materialien wie Aluminiumoxid, Aluminiumnitrid, Zirkonoxid, Siliziumkarbid, Siliziumnitrid und auf Titan basierende Materialien – jedes mit seinen eigenen spezifischen Eigenschaften – sind günstigere und optimalere Alternativen zu traditionellen Materialien, wie Metallen, Kunststoffen und Glas. Durch Einsatz und Anwendung dieser Werkstoffe sind Produktionssteigerungen und damit verbundene Kostensenkungen zu erzielen. Neue Materialien werden ständig weiter entwickelt und verbessert um den Anforderungen von individuellen Anwendungen zu entsprechen.
Entwicklungsingenieure müssen die Eigenschaften der unterschiedlichen Materialien kennen, um den richtigen Werkstoff für die jeweilige Anwendung auswählen zu können. Gerade wenn es um die Form, Design und die Anwendung des Teiles geht, müssen viele Faktoren bereits in der Planungsphase beachtet werden. Häufig werden Keramikteile ähnlich wie Metallteile konstruiert. Dies kann erhebliche Auswirkungen auf Kosten, Haltbarkeit und Eigenschaften haben. Wichtig: Keramikgerechte Konstruktion !
Bei der Verbindung von keramischen Bauteilen mit Metallteilen sind ebenfalls die Eigenschaften beider Komponenten zu berücksichtigen. Morgan Advanced Materials ist weltweit führend mit dem entwickelten Aktivlot und Löten von metallisierter Keramik mit entsprechenden Metallteilen. Unsere Anwendungs-Ingenieure erarbeiten mit Kunden weltweit gemeinsame und integrierte Lösungen für Komponenten in jeder Größe, Abmessungen, Formen, Spezifikationen und Anforderungen.
Gewünschte Eigenschaften für die Anwendung, physikalische Eigenschaften wie Festigkeit, Härte, Abriebfestigkeit, Korrosionsbeständigkeit und thermische Stabilität müssen berücksichtigt werden bei der Auswahl bestimmter Materialien. Jede dieser Eigenschaften zeichnet spezifische Materialien aus; für eine Analyse der Materialeigenschaften siehe Fig. 1. Entwicklungs Ingenieure sind bestrebt, Materialien auszuwählen die die besten Eigenschaften kombinieren um einwandfreie und optimale Lösungen zu erzielen.
Materialien
Sind die Materialeigenschaften für die jeweiligen Anwendungen ausgewählt, müssen Entwickler die eeignete Keramiken auswählen. Es gibt eine Vielzahl von verfügbaren keramischen Materialien mit unterschiedlichen elektrischen, thermischen und/oder chemischen Eigenschaften. Beispiele sind unten beschrieben:
Aluminiumoxid
Aluminiumoxid ist ein vielfältig einsetzbares Material das eine Kombination aus guten mechanischen und elektrischen Eigenschaften bietet. Für ein weites Anwendungs-spektrum, z. B.: Laser-und Röntgen-Geräte, Elektronen-Röhren für Luft- und Raumfahrt sowie Apparaturen für Hochvakuum-Anwendungen, Durchflussmengenmesser, Drucksensoren und Verschleißkomponenten, wird dieser Werkstoff eingesetzt. Er hat eine gute Festigkeit und Steifigkeit, Härte ähnlich Diamant und eine hohe Abriebfestigkeit. Aluminiumoxid gibt es mit unterschiedlichen Reinheitsgraden von 60% bis 99.9% und weiteren Zuschlagstoffen, die die einzelnen Eigenschaften wie Abriebfestigkeit oder dielektrische Festigkeit erhöhen, erhältlich. Es kann mit unterschiedlichen Herstellungsprozessen geformt werden, z.B. isostatisch gepresst, „net shape“ oder überwiegend auch noch vor dem Sintern bearbeitet; unterschiedliche Größen und Formen. Nach dem Sintern erfolgt eine Präzisionsbearbeitung mit Diamantwerkzeugen um die geforderten Toleranzen durch Schleifen, Läppen, Honen oder Polieren zu erhalten. Durch Aufbringung eine Metallisierung an den entsprechenden Stellen können Metallteile angelötet werden. Weiterhin besteht die Möglichkeit, die Keramiken speziell durch Metallbedampfungs- und Löt-Techniken zu verbinden.
Aluminiumnitrid (AIN)
Aluminiumnitrid hat eine exzellente thermische Leitfähigkeit. Weitere Eigenschaften sind sehr gute Thermoschock- und Korrosionsbeständigkeit. Aufgrund dieser Eigenschaften wird AIN in Leistungselektronik, flugtechnischen Systemen, Bahn, Optoelektronik, Halbleiterentwicklung, Mikrowellen- und Militäranwendungen eingesetzt. Typische Anwendungen sind Heizgeräte, Fenster, IC-Gehäuse und Kühlkörper.
Zirkonoxid
Zirkonoxid hat eine besondere chemische und korrosive Beständigkeit bei hohen Temperaturen bis zu 2400 °C – weit über dem Schmelzpunkt von Tonerde. In reiner Form vermindern Kristallstrukturveränderungen den Einsatz in bei mechanisch/temperaturabhängigen Anwendungen. Durch Zusatz von Kalzium wird Zirkonoxid stabiler; Zusätze von Magnesium oder Yttriumoxid ergeben sich sehr hohe Festigkeit, Härte und in Einzelfällen auch verbesserte Zähigkeit. Morgan ist ein Pionier auf diesem Sektor der Materialtechnologie, wenn es um die Herstellung von teilweise stabilisiertem Zirkonoxid mittels Magnesia (Mg-PSZ) und Yttrium Tetragonal Polykristalines Zirkonoxid (Y-TZP) geht. Diese zählen zur Gruppe der äußerst festen und harten Zirkonoxid Keramiken, die über eine physikalisch chemische Umwandlung verstärkt werden. Sie eignen sich für konstruktive oder strukturelle Anwendungen bei denen außergewöhnlich hohe mechanische Festigkeit und Eigenschaft wie Härte, Abriebfestigkeit und Korrosionsbeständigkeit gefordert sind. 3Y-TZP ist ein ähnliches Produkt wie es auch bei medizinischen Implantaten eingesetzt wird. Aufgrund der guten Temperaturwechselbeständigkeit von stabilisiertem Zirkonoxid (FSZ) werden Komponenten für Tiegel, Ausgießer und Bauteile für Metallschmelze hergestellt und eingesetzt.
Siliziumnitrid
Siliziumnitrid hat eine exzellente hohe Temperaturbeständigkeit, Fließ- und Oxidationsbeständigkeit wobei der geringe thermische Ausdehnungskoeffizient, verglichen mit den meisten anderen keramischen Materialien, gute thermische Eigenschaften hat. Es besitzt eine hohe Bruchfestigkeit, Härte, chemische Beständigkeit und gute Abriebfestigkeit. In drei Haupt Produktgruppen werden eingeteilt: Reaktionsgebundenes Sliziumnitrid (RBSN), heiß gepresstes Siliziumnitrid (HPSN) und gesintertes Siliziumnitrid (SSN). RBSN ist ein relativ weiches Produkt verglichen mit HPSN und SSNM Nitrid Typen. Aus diesem Grund kommen HPSN- und SSN-Materialien häufiger zum Einsatz. Typische Anwendungen sind: Kugellager und Roll-Elemente, Schneidwerkzeuge, Ventile, Rotoren von Turboladern für Maschinen, Glühkerzen, Buntmetall-Schmelzbearbeitung, Wärmefühlerhülsen, Schweißvorrichtungen sowie Halterungen und Schweißdüsen.
Siliziumkarbid
Siliziumkarbid ist ein sehr abriebfestes Material mit guten mechanischen Eigenschaften, hoher Temperaturfestigkeit und -beständigkeit bis zu 1650 °C. Es hat eine geringe Dichte, hohe Härte und Abriebfestigkeit sowie eine hervorragende chemische Beständigkeit. Aufgrund seiner Materialcharakteristik eignet es sich besonders für fixe und bewegliche Turbinen-Komponenten, Stempel, Auflagen, Kugelventilteile und Ausrüstung in der Halbleiterplattenfertigung. Weitere Spezialanwendungen sind Balken- und Profilträger, Transportrollen, Röhren, Brennplatten- und Schildvorrichtungen aber auch Wärmefühlerhülsen.
Form der Komponenten
Ist das Material ausgewählt, besteht der erste Schritt darin, das Design zu entwickeln. Hierbei sind gewisse Richtlinien zu berücksichtigen, um mögliche Schwachstellen in den Komponenten auszuschließen. Entwicklungs- Ingenieure und Hersteller sollten die keramischen Bauteile möglichst einfach und tragende Teile nicht zu komplex zu konstruieren. Beispielsweise sollten scharfe Kanten und Ecken genauso wie extremen Querschnitts Änderungen vermieden werden.
Aktivlöten/Löten
Für zahlreiche Anwendungen ist es oft notwendig, Keramik mit Metall zu verbinden um ein entsprechendes Bauteil herzustellen. Keramik-Metall-Bonding ist eine der größten Herausforderungen zwischen Hersteller und Anwender. Aufgrund der unterschiedlichen thermischen Ausdehnungskoeffizienten der beiden sehr unterschiedlichen Materialien, ist eine exakte Abstimmung notwendig. Verschiedene Methoden wie mechanische Befestigung, Reibschweißen und Adhäsionskleben finden Anwendung. Die mit Abstand meist verbreitete und effektivste Methode für dauerhaft dichte, robuste Verbindung zwischen Keramik und Metall ist allerdings das Löten. Dies beginnt mit dem Aufbringen einer Metallbeschichtung auf die Keramik.
Die benetzte Oberfläche führt beim Lötprozess zu einer Lötlegierung.
Um eine optimale Verbindung zu erreichen, werden die Keramikteile üblicherweise mit Molybdän Mangan (MoMn) beschichtet und anschließend vernickelt. Nach diesem Prozess können die Bauteile gelötet werden. Meistens mit Metallen, die sehr ähnliche Ausdehnungskoeffizienten wie Keramik aufweisen.
Innerhalb Morgan Advanced Materials fertigt WESGO Lote für einen weiten Temperaturbereich. Höchste Reinheit, Unterdampfdruck Legierungen sowie Schweißzusatzstoff aus Edelmetall, Grundmetall und Aktivlote. Edelmetall Lote auf Basis von Gold-, Silber-, Platin- und Palladium sind hervorragend geeignet die Anforderungen bei Hochleistungsröhren, Luft- und Raumfahrt, Halbleiter, Medizintechnik, Elektronik und die Vakuum-Industrie, zu erfüllen. Grundmetall Schweißzusatzstoffe sind ideal für die Fertigung im Bergbau und Anlagen für die Schwerindustrie. Sie sind für Lötanwendungen zwischen 500 °C und 1200 °C geeignet.
Aktivlötlegierungen stellen einen einfachen Zugang bei der Verbindung von Metall und Keramik dar. Beim Aktivlöten ist eine Metallisierung der Keramik nicht erforderlich. Eine Metallbedampfung der Keramik erfolgt nicht, da die aktiven Komponenten die Benetzung der Keramik beim Prozess unterstützen. Da dies in einem einzigen Schritt umgesetzt werden kann, ist eine Metallisierung, Sintern und vernickeln nicht erforderlich. Als „single step“ kann dieser Prozess ausgeführt werden und ist mit relativ geringen Kosten verbunden.
Eingesinterte Pins für elektreische Durchführungen
Für spezifische Anwendungen, wie Durchflussmessgeräte kann eine elektrische Durchführung mittels eingesinterten Drahtes hergestellt werden. Ein Metallpin wird in die „grüne“, ungesinterte Keramik, nach dem Einbringen der Bohrung, eingeführt und gesintert. Während des Sinterprozesses verbindet sich der Pin mit der Keramik. Die Keramik schwinded beim Sinter-Prozess auf den Pin und somit erhält man einen gasdichten Übergang. Besonderes „ Know how“ ; Sinter-Prozess, Temperaturverteilung und Kontrolle sowie eine sorgfältige Auswahl des Metalls garantieren den stabilen Prozess.
Glasieren
Die Oberflächenstruktur des fertigen Produktes hängt von der Korngröße sowie der Qualität der Grünbearbeitung ab. Wenn eine glatte, gut zu reinigende Oberfläche erforderlich ist, können Bauteile glasiert werden.
Das ist besonders wichtig, wenn die Teile Staub oder Umwelteinflüssen ausgesetzt sind. In diesem Fall kann eine glasierte Oberfläche leichter gereinigt werden, um Oberflächenleckagen und Durchschläge zu vermeiden.
Die optimale Lösung:
Viele Faktoren spielen zusammen: Materialauswahl, Materialeigenschaften und Design sind zu berücksichtigen, um ein optimales Produkt zu entwickeln. Am wichtigsten ist es, die Anwendung, die Anforderungen an thermische, mechanische, elektrische und chemische Eigenschaften zu berücksichtigen. Die Härte der Keramik, physische Stabilität, extreme Hitzebeständigkeit, chemische Beständigkeit, Bioverträglichkeit, elektrische Eigenschaften und nicht zuletzt die Eignung für Massenproduktion, zeichnet die Keramik als eine der vielfältigsten Materialgruppen aus.
Nicht für alle Anwendungen ist Keramik geeignet. In zahlreichen Fällen ist es aber die einzig mögliche Option bei extremen Umgebungsbedingungen während des Einsatzes.
Technische Keramiken vereinen die Anforderungen höchster Leistungskomponenten in einem weiten Anwendungsspektrum. Mit der Kenntnis der Werkstoffdaten und physikalischen Eigenschaften über Keramik und Keramik-Metall Verbindungs-Techniken wie Aktivlötung, Metallisierung und Löten, die Vorteile von Glasuren und Beschichtungen sind Ingenieure und Hersteller in der Lage, zunehmend komplexere Komponenten zu entwickeln.
Für weitere Informationen besuchen sie http://www.morganadvancedmaterials.com
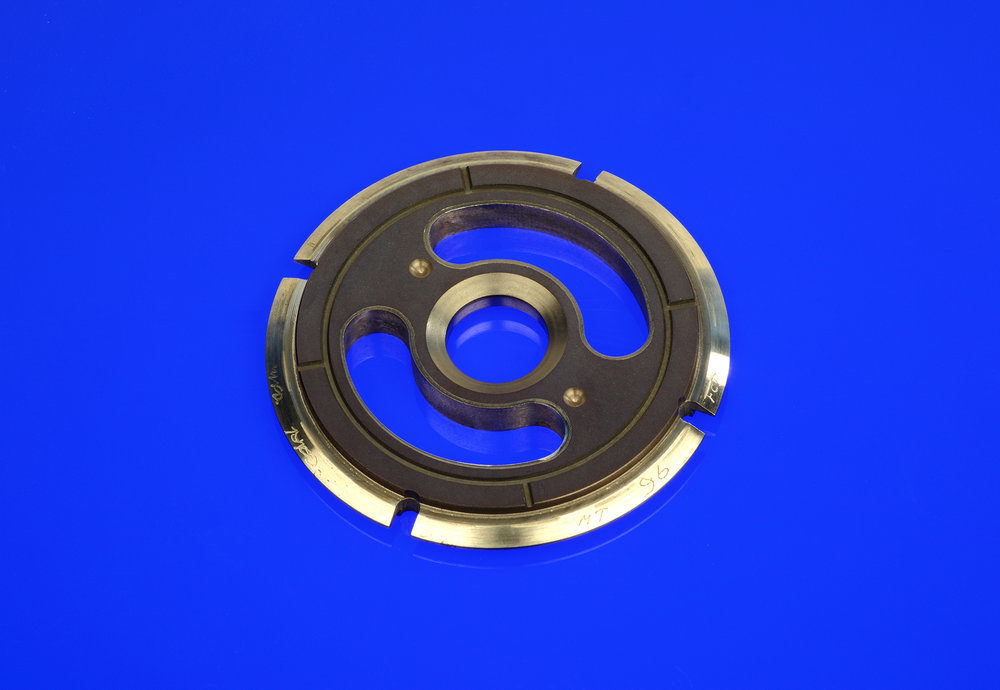

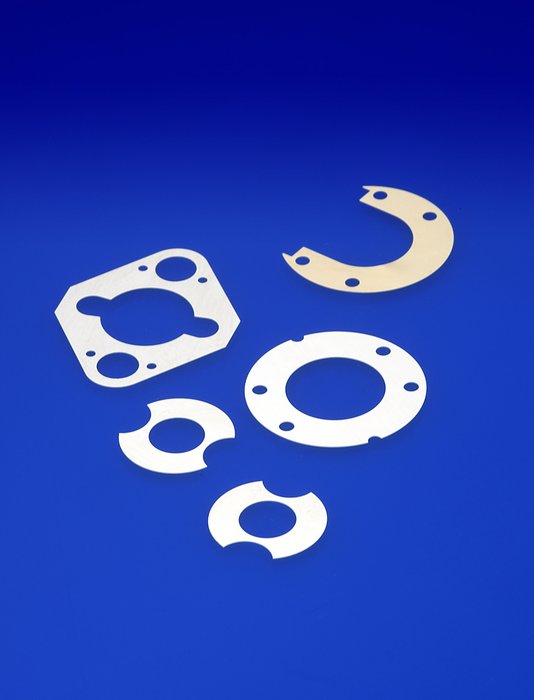
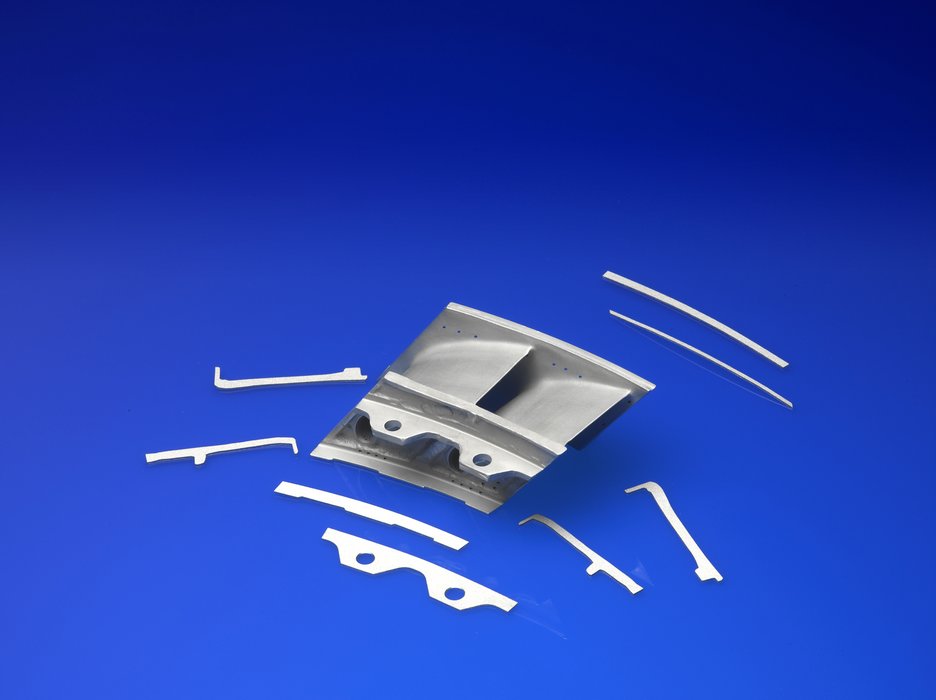
Fordern Sie weitere Informationen an…