www.konstruktion-industrie.com
01
'21
Written on Modified on
VOLLER ÜBERBLICK IM SERVICE-SPEKTRUM: UMFANGREICHE MODERNISIERUNG FÜR PROZESSKRANE BEI WELSER PROFILE
Aufgerollte Stahlbleche sind die Grundlage für viele industrielle Prozesse. Aus ihnen stellt die Welser Profile Deutschland GmbH mit Sitz in Bönen bei Dortmund Profile für unterschiedlichste anspruchsvolle Anwendungen und Branchen her, wie zum Beispiel die Automobilindustrie und Energieerzeugung. Bei einer Inspektion stellten die Experten von Konecranes fest: Die Prozesskrane im Coil-Lager der Profil-Profis müssen dringend modernisiert werden. Das soll zeitnah geschehen und besonders schnell umgesetzt werden, denn ohne den Stahl aus dem Lager steht die Produktion bei Welser Profile still. Gleichzeitig sind hohe Sicherheits- und Qualitätsanforderungen einzuhalten, damit die Arbeit im Lager weiterhin effizient und sicher ist – eine Herausforderung, die die Experten von Konecranes und Demag Services gemeinsam mit ihren Kollegen des Tochterunternehmens KSR annehmen.
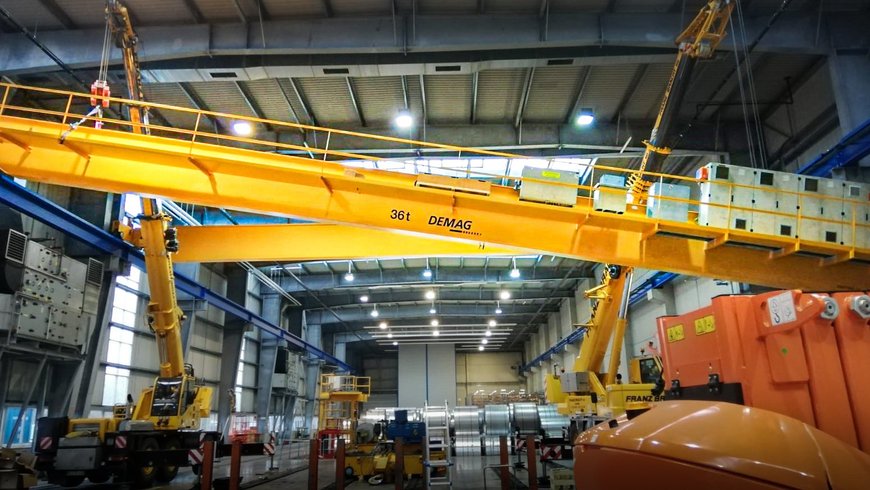
Schwere Stahlrollen, Coils genannt, werden in vielen Betrieben verwendet. Aus dem aufgerollten Stahlblech lassen sich verschiedenste Werkstücke fertigen. Deshalb ist das Material gefragt: Nachdem die Corona-Pandemie laut dem Stahlverband Eurofer den Stahlverbrauch im Jahr 2020 um etwa 13 Prozent gedrückt hatte, soll er im laufenden Jahr 2021 wieder steigen und mit etwa 152 Millionen Tonnen nahezu das Niveau von 2019 erreichen.
Aus Stahlblechen hergestellte Profile sind in beinahe jedem Industriesektor zu finden – von Automotive und dem Bau, wo insgesamt der meiste Stahl überhaupt zum Tragen kommt, bis hin zur Energiegewinnung und Agrartechnik. Die Welser Profile GmbH mit Stammsitz in Ybbsitz an der Niederösterreichischen Eisenstraße und Produktionsstandort in Bönen bei Dortmund hat sich auf Stahlprofile aller Art spezialisiert. Ihre Produkte kommen in den neuen Nachtzügen der Österreichischen Bundesbahn ebenso zum Einsatz wie in großen Photovoltaik-Anlagen – und das weltweit. Im Rollform-Verfahren haben die Experten seit 1960 bereits mehr als 23.500 einzigartige Profil-Querschnitte für individuelle Anforderungen in praktisch allen Branchen realisiert.
Schnelle Hilfe bei Materialermüdung
Im Coil-Lager in Bönen arbeiten zwei Prozesskrane, die das Rohmaterial für die Profilherstellung sicher und zuverlässig transportieren müssen. Bei einer Inspektion durch Experten von Konecranes und Demag Services stellt sich heraus, dass der Träger eines Demag-Krans Risse zwischen Kopfträger und Kranbrücke aufweist und damit nicht mehr einsatzfähig ist. „Im Laufe des Lebenszyklus eines Krans muss er immer wieder hohe Lasten aufnehmen und transportieren“, erläutert Sascha Oppenhäuser, Director Service EMEA Central North bei Konecranes. „Dabei kommt es zwangsläufig mit steigendem Alter des Krans zu Materialermüdung.“ Risse im Träger bedeuten: Der Kran kann so nicht mehr eingesetzt werden. Das ist Gift für die Produktivität im Werk, denn ohne Stahlbleche können auch keine Profile hergestellt werden. Für den Transport der bis zu 30 Tonnen schweren Rollen gibt es keine Alternative. Um den Träger kurzfristig zu stabilisieren, führten die Experten von Konecranes eine Notreparatur aus. Sascha Oppenhäuser: „Dabei werden die gerissenen Stellen aus dem Kranträger herausgeschnitten und mit frischen, eingepassten Stahlteilen ausgetauscht.“ Diese bewährte Art der Reparatur ist jedoch nur eine kurzfristige Überbrückungshilfe, denn sie verändert Form und Struktur des Trägers, was den Verschleiß deutlich erhöht.
Teamwork für eine effektive Modernisierung
Darüber hinaus hatte sich bei der Inspektion gezeigt, dass die Kranbahn ebenfalls stark verschlissen war. „Die Kranbahn und die Fahrwerke gehören zu den Haupt-Verschleißteilen an jeder Anlage“, betont Sascha Oppenhäuser. „Oft ändern sich mit der Zeit die Anforderungen an die Krane – wo früher etwa nur 15 Tonnen gehoben werden mussten, sind es heute schon einmal 30 Tonnen. Dafür wurden die ursprünglichen Kranbahnen allerdings meistens nicht ausgelegt.“ Eine langfristig ausgerichtete und zukunftssichere Modernisierung des Krans ist deshalb sinnvoll. Die Experten von Konecranes erstellen dafür ein Gesamtkonzept von der Teilebestellung bis zur Abnahme. Zeit ist dabei ein wichtiger Faktor: Die Schäden wurden Mitte des Jahres 2020 festgestellt und per Notreparatur behoben und die Modernisierung sollte bis Anfang des Jahres 2021 umgesetzt sein. Für ein optimales Ergebnis arbeitet das Service- und Modernisierungsteam von Konecranes und Demag mit seinen Kollegen der Tochtergesellschaft KSR zusammen. Sie sind auf die Ertüchtigung von Kranbahnen spezialisiert und übernehmen diesen Teil des Projekts, während sich die Konecranes-Experten auf den Austausch der Fahrwerke an beiden Prozesskranen des Coil-Lagers, den Austausch der kompletten Brücke des beschädigten Krans sowie neue Schleppkabel konzentrieren. Sascha Oppenhäuser: „Katze und Elektrik des Krans haben wir erhalten. So können wir eine wirtschaftlichere und schneller umzusetzende Alternative zu einem Komplett-Austausch des Krans liefern.“
Das Projekt ist umfassend: 200 Meter Kranbahn sind zu erneuern, vier Fahrwerke für die beiden Krane sowie eine komplett neue Kranbrücke mit mehr als 24 Metern Spannweite und eine neue Schleppkabelanlage werden geliefert und installiert.
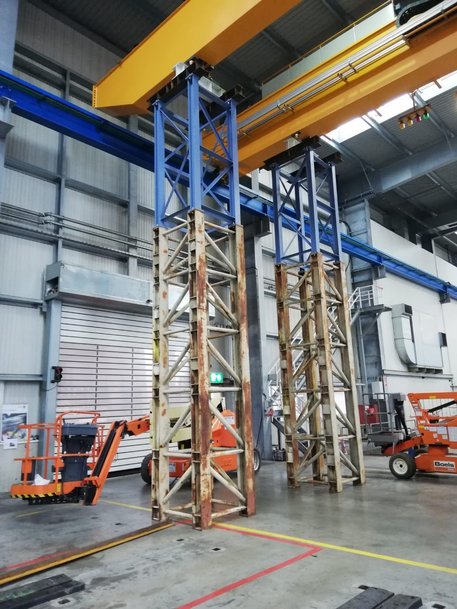
Mammut-Modernisierung im Coil-Lager
Um diese Mammutaufgabe fristgerecht zu bewältigen, ohne die Produktion zu stark zu beeinträchtigen, werden der Kranbahn-Austausch und die Arbeiten an den Kranen selbst zeitgleich stattfinden und optimal aufeinander abgestimmt. „Unsere Teams von Konecranes und KSR planen ihre Arbeitsschritte genau so, dass sie sich zu keiner Zeit im Wege stehen“, sagt Sascha Oppenhäuser. „Damit stellen wir einen flüssigen Arbeitsablauf sicher.“
Besonders der Transport der neuen, enorm langen und sehr schweren Kranbrücke ist dabei eine Herausforderung. Vom Sonder-Lkw in die Halle und dort hinauf zu ihrer endgültigen Position transportieren sie bis zu vier Autokrane. Sascha Oppenhäuser: „Unsere Projektleitung stellt sicher, dass nicht nur die Brücke, sondern auch die passenden Experten am richtigen Tag da sind, um sie einzubauen.“ Für den Austausch der Fahrwerke auch am zweiten Zweiträgerbrückenkran des Lagers wird dieser kurzfristig „aufgebockt“. Die neue Kranbahn und die Fahrwerke sind robuster und für höhere Belastungen ausgelegt als die ursprünglichen Komponenten und damit zukunftsorientiert.
Moderne Sicherheitsfeatures
Damit die Arbeit mit den modernisierten Kranen genauso sicher ist, rüsteten die Experten von Konecranes sie zusätzlich mit einer Bereichsabschaltung aus. Sie verhindert, dass die Katze unter Last in einen definierten Teil der Halle fährt – was die Statik der Kranbahn gefährden könnte. Dazu erfassen Laser-Distanzsensoren die Position der Katze und lösen eine Bremsung aus, wenn sie in die Nähe der definierten Sicherheitszone kommt. „Zudem haben wir die Ausgleichstraverse an der Katze mit einer Traverse mit integrierter Duplex-Messachse ausgetauscht. So erkennt die Steuerung zuverlässig, wie viel Last am Haken hängt“, erläutert Sascha Oppenhäuser.
Trotz des hohen Projektumfangs setzen die Teams von Konecranes und KSR gemeinsam das Projekt fristgerecht um. Sascha Oppenhäuser über den gemeinsamen Erfolg: „Wir haben gezeigt, dass wir uns mit unseren Kollegen von KSR bestens ergänzen, und für unseren Kunden einen hochkomplexen Prozess optimal realisiert.“ Die modernisierten Krane heben seit Anfang Januar 2021 wieder effizient und sicher ihre wertvolle Stahllast in Bönen.
www.konecranes.com
Fordern Sie weitere Informationen an…