www.konstruktion-industrie.com
25
'21
Written on Modified on
COBOTS - HAND IN HAND MIT EINEM ROBOTER SCHRAUBEN
Spörk zeigt, wie eine kollaborierende Roboterlösung sicher und wirtschaftlich realisiert werden kann: Ein Praxisbeispiel bei ZKW illustriert, was bei der Automatisierung mit Cobots alles bedacht werden muss.
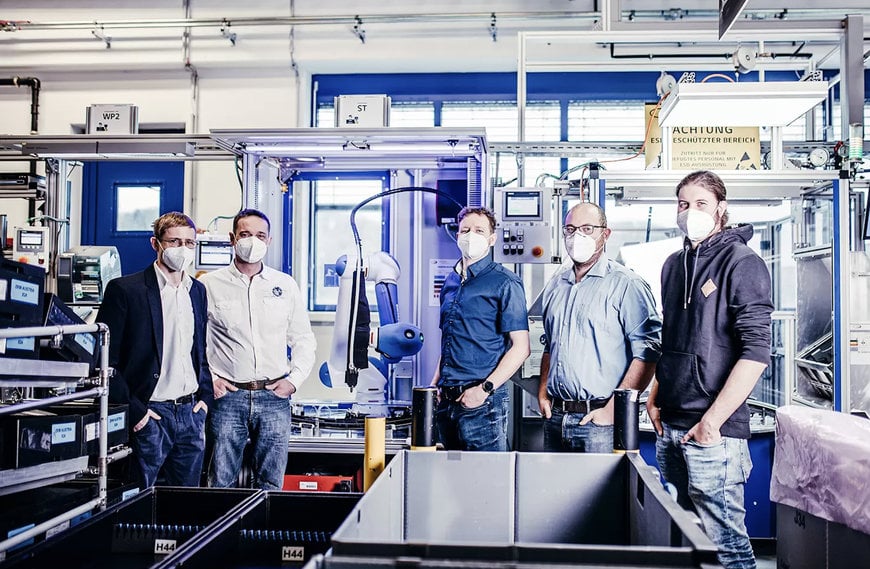
Für Christian Blamauer war es nur eine Frage der Zeit, bis eine kollaborative Roboteranwendung bei ZKW in einer passenden Applikation realisiert werden würde. Schon mit Beginn des Cobots-Hypes vor rund drei Jahren hat sich der Leiter der Abteilung Process Engineering mit seinem Team Gedanken darüber gemacht, welcher Use Case denn dafür in Frage kommen könnte. Letztlich war es die Fertigung eines neu entwickelten Produktes, bei dem ergänzend zu den bisher vorhandenen Roboterfertigungslinien eine kollaborierende Lösung erstmalig zum Einsatz kommen sollte. Dabei stand die Automatisierung einer kollaborierenden Schraubanwendung für ein Leuchtenband im Vordergrund.
Zuerst der Use-Case, dann der Cobot
„Wir haben schon bei der Planung aus meiner Sicht vieles richtig gemacht“, sagt Blamauer. Denn zuerst wurde der Use-Case definiert, dann ein Sicherheitskonzept dafür erstellt und auf diesen Vorarbeiten aufbauend eine Bewertungsmatrix erstellt, um den passenden Roboter für diese Applikation zu finden. In dieser Bewertungsmatrix, mit der letztlich fünf in Frage kommende Cobots analysiert wurden, ging Yaskawas Modell HC10 als Sieger hervor. Blamauer: „Wir wollten sicherheitstechnisch auf Nummer sicher gehen und dabei sowohl den normativen Ansprüchen als auch unseren eigenen, was die Sicherheit unserer MitarbeiterInnen anbelangt.“ Dazu wurden die Spezialisten von Spörk und Yaskawa ins Boot geholt. Diese wurden mit der Auslegung, Berechnung sowie Ausführung und Beratung beauftragt. Dies beinhaltete die Mitgestaltung bei der Planung, der Programmierung und Installation vor Ort beim Kunden, umfangreiche praktische Tests sowie die fachliche Einschulung der Anwender und Inbetriebnahme. Die Gespräche bewegten sich rasch auf eine inhaltliche Detailebene, so Blamauer: „Für so ein Projekt brauchten wir fachkundige Antworten, hier war die Zusammenarbeit absolut positiv!“
Menschen dürfen nie auf den Roboter warten
Die besondere Herausforderung bei diesem Projekt lag in der Prüfung der Machbarkeit und Umsetzung der notwendigen Anforderungen an den Roboter. Die automatisierte Schraubanwendung musste ohne jegliche Schutzumhausung, Sicherheitszaun oder Lichtgitter einsetzbar sein. Die Vorgabe war eine Verschraubung von mindestens 9 Schrauben in einem Leuchtenband innerhalb einer Taktzeit von maximal 70 Sekunden unter Beachtung der Richtlinien für Mensch-Roboter Interaktionen. Das Leuchtenband wird händisch von der Bedienerin in die dafür vorgesehene Aufnahme eingelegt. Nach Fixierung des Bauteiles wird durch Betätigung eines Freigabetasters die Arbeitsfreigabe für den Roboter erteilt. Während die Bedienerin manuell zusätzliche Bauteile positioniert, beginnt der Roboter die verschiedenen Positionen der Schraublöcher anzufahren. Die Schrauben werden vereinzelt und pneumatisch der Schraubspindel zugeschossen. Entscheidend für die Wirtschaftlichkeit ist, so Christian Blamauer, dass „die Menschen nie auf den Roboter warten dürfen, der Roboter hingegen auf den Menschen schon.“ Denn wenn die Werkerin darauf warten muss, bis der Cobot ihr etwas in die Hand gibt, ist es effizienter das Teil selbst zu holen. Daher musste der Prozess exakt am menschlichen Arbeitsanteil getaktet werden. Aufgrund der konzeptionellen Umsetzung ergab sich für ZKW eine Erhöhung der Produktivität durch den kollaborierenden Betrieb.
Patentierter Schraubkopf für sichere Kollaboration
Das gesamte Robotersystem wurde auf einem Universalschraubtisch aufgebaut. Das bringt erhebliche Platzersparnis aufgrund der nicht benötigten Einhausung, und aufgrund der integrierten Kraft- & Momenteüberwachung des HC10 in jeder Achse konnte auf weitere Sicherheitstechnik verzichtet werden. Diese Sicherheitsfeatures sind beim HC10 bereits Standard. Entscheidend für den Erfolg des Projekts erwies sich jedoch die Lösung, die für den Schraubkopf gefunden wurde. „Wir haben das am Markt vorfügbare Schraubequipment geprüft, doch keines hat unserer Anforderung entsprochen“, erzählt Blamauer. Also ging seine Abteilung, die mit 80 Mitarbeitern für Industrialisierung der Montageanlagen verantwortlich ist, daran, ein eigenes passendes Teil zu engineeren. Das Ergebnis ist ein mittlerweile patentierter Schraubkopf, der kollaboratives Schrauben unter Einhaltung höchster Sicherheitslevels erlaubt und so einen echten Wettbewerbsvorteil bietet. Der Universalschraubtisch konnte zudem auch so flexibel konstruiert werden, dass eine Umrüstung der Produktaufnahme ohne große Umbauten jeder Zeit möglich ist. Die Lehre daraus, so Blamauer: „Zuerst an die Sicherheit Denken, nicht zuerst an die Einsparung!“
Mit Spörk zur Lösung nach Maß
Alle an diesem Projekt beteiligten, das sowohl für ZKW wie auch für Spörk eine Premiere bei der Realisierung einer Cobot-Applikation war, haben enorm viel Know-how dazugewonnen. Andreas Pflügl, bei Spörk als Produktmanager Yaskawa und für den Vertrieb in der Ostregion erster Ansprechpartner von ZKW für das Projekt, ist der zentrale Lerneffekt klar: „Zuallererst muss geprüft werden, ob der Anwendungsfall für einen Cobot passend ist, oder ob nicht ein Industrieroboter die bessere Lösung ist.“ Hier kommt auch die Stärke von Spörk bei der Beratung zum Tragen: „Wir müssen keinen Cobot verkaufen, bei uns steht die Beratung an erster Stelle – wir entwickeln mit dem Kunden die Lösung, die für seinen Anwendungsfall am besten passt.“ Das Vertrauen von ZKW in die Kompetenz von Spörk und Yaskawa, der reibungslose Kommunikationsfluss, das Engagement für individuelle Lösungsfindungen sowie die kundenorientierten Optimierungsvorschläge machten die technische Aufgabenstellung zu einem gelungenen Cobot-Projekt.
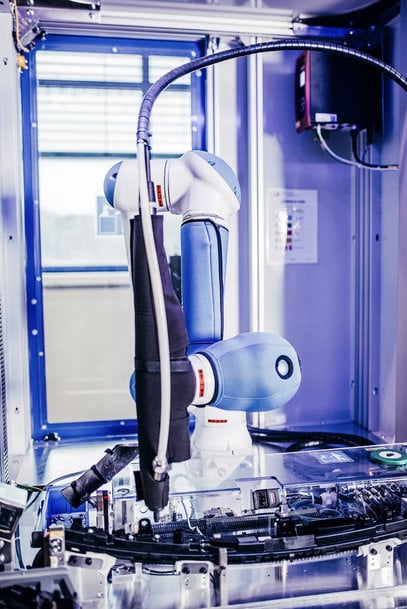
Lösungskonzept auf Augenhöhe
Für uns bedeutet „Lösungskompetenz auf Augenhöhe“, dass wir uns in erster Linie als Partner der Klein- und Mittelbetriebe in Österreich verstehen. Auf diese Unternehmen kommen Automatisierung und Robotik immer stärker zu. Wir als Spörk sind ja auch ein KMU, verstehen diese Kunden daher gut und können passende Automatisierungslösungen für diese gestalten. Kommunikation auf Augenhöhe hat sich aber auch bei ZKW ergeben, denn unser Ansprechpartner dort war die Abteilung für den internen Anlagenbau, die etwa 80 Mitarbeiter umfasst. Da arbeiten junge Techniker, die mit uns auf Augenhöhe an den Lösungen gearbeitet haben.
Das Cobot-Projekt war sowohl für ZKW als auch für uns eine Innovation. Beide haben an dem Projekt gelernt. Wir als Spörk transferieren diese Erfahrungen nun in andere Branchen. Bei Cobots geht es darum, den Prozess genau zu definieren und sukzessive eine Integrationslösung zu finden. Dabei geht es einerseits um Sicherheit am Arbeitsplatz bei der Mensch-Roboter-Kollaboration, andererseits um die Geschwindigkeit: MRK-Prozesse laufen im Vergleich zu Industrierobotik eher langsam ab. Das wird sich in den kommenden Jahren mit Sicherheit erhöhen, aber maximal bis zu einem Punkt bei dem der Mensch vom Arbeitstempo her noch mitkann.
Wir haben einige Anfragen zum Cobot-Einsatz, die wir mit den Kunden prüfen. Doch wir haben keinen Druck, unbedingt einen Cobot verkaufen zu müssen: Nur wenn es sich in der individuellen Analyse als beste Lösung herausstellt, empfehlen wir es und bieten einen Cobot an. Wir sehen bei KMUs, dass die Bereitschaft sich mit Automatisierung und Robotik zu beschäftigen, immer größer wird. Oft besteht aber noch zu wenig Klarheit darüber, was das konkret für den Betrieb heißt. Meist gehen wir zu Beginn einfach mit dem Inhaber durch seine Firma und können ihm schon aufgrund unserer Erfahrung sagen, wo Automatisierung Sinn machen könnte und wo nicht, weil die Kosten-Nutzen-Relation nicht gegeben sein wird. Das ist unsere primäre Beratungsleistung: Was heißt Automatisierung konkret für mich? Dazu bieten wir Lösungskompetenz auf Augenhöhe.
www.yaskawa.com
Fordern Sie weitere Informationen an…