www.konstruktion-industrie.com
11
'22
Written on Modified on
MIT DIGITALEM ZWILLING KANN DER CNC-ROBOTER MEHR
Robotik-Integration und Edge-Computing für Bestandsmaschinen – das Siemens Motorenwerk in Bad Neustadt hat mit tatkräftiger Unterstützung von HEITEC ein Fräszentrum mit CNC-gesteuertem Roboter und Edge-Computing aufgerüstet. Der Clou: Ein digitaler Zwilling des Roboters für Inbetriebsetzung und Arbeitsvorbereitung – sogar das Teach-in neuer Werkstücke gelingt in der virtuellen Welt.
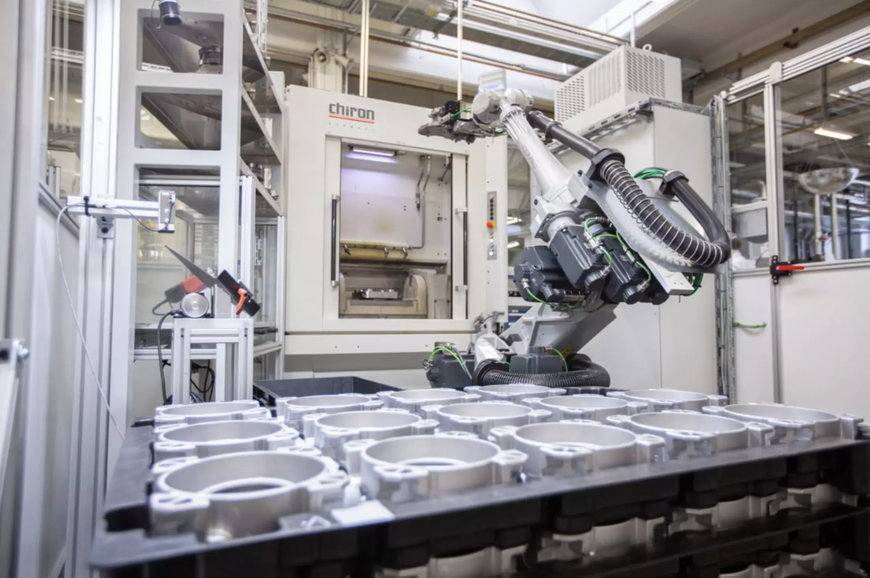
Ein Roboter – nur für das Handling? Da geht mehr!
Der Roboter entnimmt ein Rohteil aus einer Blisterpalette, legt es auf eine Ausrichtstation, eine Kamera prüft die Lage. Dann greift es der Roboter erneut – nun korrekt ausgerichtet – und tauscht im Arbeitsraum des Fräszentrums das fertige Werkstück gegen das neue Rohteil. Soweit eine typische Handling-Aufgabe für Roboter – und schon oft gesehen.
Ein solcher Automatisierungsgrad wäre allerdings nicht zufriedenstellend gewesen. Ziel war eine Automatisierung des gesamten Prozesses – inklusive Wechsel der Spannvorrichtungen, dem Entgraten als die Nachbearbeitung und eine prozessbegleitende Qualitätskontrolle für wechselnde Werkstücke. Außerdem sollten die CNC-Programmierer auch die Roboter-Programme selbst erstellen, anpassen und optimieren können.
Systembrüche der klassischen Robotik vermeiden
„Klassische Roboterprogrammierung und Fremdcontroller hätten die Prozessketten der Arbeitsvorbereitung verändert, und wir hätten die Automatisierung von Maschine und Roboter auf zwei unterschiedliche ‚Beine‘ gestellt“, so Johannes Schunk, Leiter der Arbeitsvorbereitung in Bad Neustadt. Um dies zu vermeiden, entschied man sich für die Integration eines Roboters der Firma Comau über Run MyRobot/Direct Control. Damit lassen sich alle Roboteraktionen direkt mit Sinumerik programmieren und steuern – mit vertrauten Zyklen, präzise und ohne Umweg über eine Fremdsteuerung.
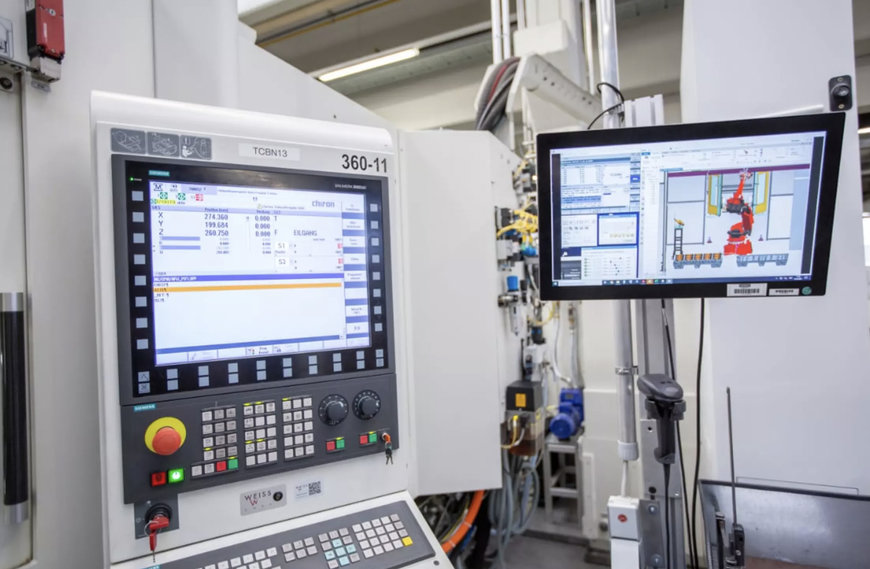
SINUMERIK Run MyRobot und der digitale Zwilling: mehr Flexibilität, kurze Projektlaufzeit
Grundsätzlich kann die Sinumerik CNC eines Fräszentrums den Roboter direkt steuern. In diesem Fall erhielt der Roboter eine eigene Sinumerik 840D sl, um die Produktionsunterbrechung durch das Projekt so kurz wie möglich zu halten.
Einen weiteren Ansatz zum Verkürzen der Projektlaufzeit bietet das CAD/CAM-System NX. Es erlaubt die Simulation von Maschine und Roboter mit digitalen Zwillingen. Das erleichterte das Programmieren der komplexen Prozesse enorm – insbesondere die Synchronisation zwischen Roboter und Werkzeugmaschine. Selbst das Anlernen der KI-Modelle für die Werkstückerkennung per Kamera konnte das Siemens-Team anhand der CAD-Modelle der Werkstücke erledigen. Dabei half die Edge-App „Protect MyMachine / Setup“.
Eine virtuelle Inbetriebnahme mit dem digitalen Zwilling erlaubte, das Bearbeitungszentrum für deutlich kürzere Zeit aus der Produktion zu nehmen als bei einer klassischen Inbetriebnahme. „Eine virtuelle Inbetriebnahme reduziert eben nicht nur Projektrisiken und -laufzeiten, sondern wirkt gerade bei Brownfieldprojekten direkt auf den Return-on-Invest des Gesamtprojekts“, erläutert Jakob Brottrager (HEITEC AG).
Hier lag auch der Tätigkeitsschwerpunkt von HEITEC als Teampartner für das digitale Umrüsten. „Ohne digitalen Zwilling hätte sich das Projekt nicht in dieser kurzen Zeit und mit derart reduzierten Produktionsunterbrechungen realisieren lassen.“
Prozessbegleitende Qualitätskontrolle und Monitoring
Roboter und Werkzeugmaschine sind jeweils über Sinumerik Edge an die Cloud MindSphere angebunden. Die Auswertung der Echtzeitdaten findet dabei auf der Edge-CPU statt – ohne die CNC zu belasten.
Das erschließt völlig neue Möglichkeiten – beispielsweise in der Qualitätsüberwachung. So werden die Prozessdaten der Werkzeugmaschine über die App „Analyze MyWorkpiece /Monitor“ visualisiert. Durch den Vergleich mit einem hier hinterlegten Soll-Prozess können relevante Abweichungen schon während der Bearbeitung erkannt und betroffene Werkstücke vom Roboter gesondert zur Nachkontrolle oder -bearbeitung abgelegt werden.
Der Vorteil: 100 % aller Werkstücke werden kontrolliert – ohne zusätzlichen Prozessschritt für die Qualitätssicherung. In der MindSphere visualisieren Apps wie Manage MyMachines zudem die von Maschinen und Roboter übertragenen Daten auf Auslastung, Ausbringung und andere Kennziffern – überall und jederzeit, auch fernab der Produktion. So lassen sich weitere Optimierungspotenziale erkennen und erschließen.
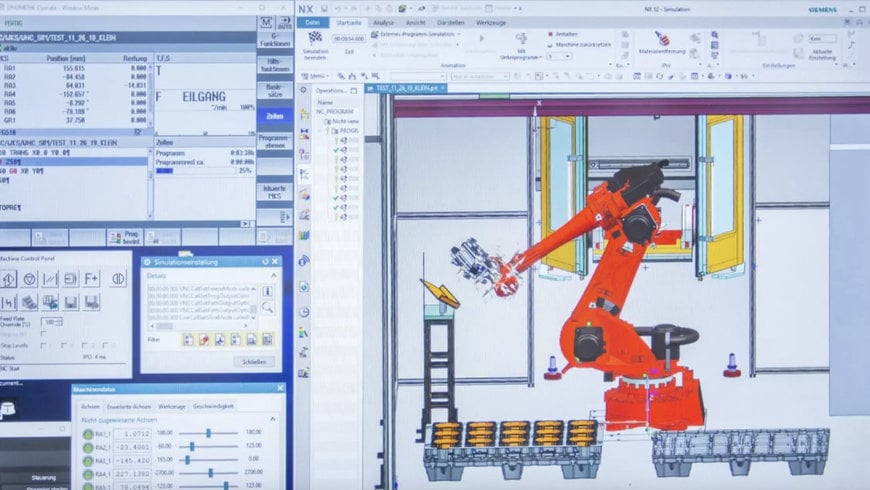
Roboter wechselt Werkstücke, Spannsysteme, stapelt Paletten – und entgratet
Und so leistet der CNC-gesteuerte Roboter an dem Chiron-Fräszentrum in Bad Neustadt heute deutlich mehr als ein üblicher Handling-Roboter: Die Edge-App „Protect MyMachine /Setup“ erkennt anhand der Kamerabilder, welche Rohteile – aktuell sind es 13 verschiedene – in der Blisterpalette liegen und veranlasst die Ausführung der entsprechenden CNC-Programme für Roboter und Werkzeugmaschine.
Indem der Roboter parallel zur laufenden Fräsbearbeitung das vorangehende Werkstück entgratet, verkürzt er die Durchlaufzeit jedes Werkstücks. Dazu führt „Robbi“ die zu entgratenden Kanten über zwei Schleifspindeln. Erfordern die neuen Werkstücke einen Wechsel der Spannvorrichtung, rüstet der Roboter die Maschine um.
Ist die Blisterpalette mit den Rohteilen leer oder die mit den Fertigteilen voll, übernimmt der Roboter auch das Umstapeln der Paletten. Durch die tatkräftige Unterstützung von HEITEC kann die Zelle so vollautomatisiert und mannlos 24/7 fertigen – Daten zur Qualität und zu den Key-Performance-Indikatoren (KPI) werden permanent über Sinumerik Edge erfasst und aus der Ferne kontrolliert.
www.heitec.com
Fordern Sie weitere Informationen an…