www.konstruktion-industrie.com
18
'22
Written on Modified on
Kombination von Automatisierung und Effizienz steigert Platzierungsproduktivität
Mühsame manuelle Vorgänge, die mit Aufgaben wie Produktumstellungen verbunden sind, können die Oberflächenmontage ausbremsen und Stillstände der Produktionslinie verlängern.
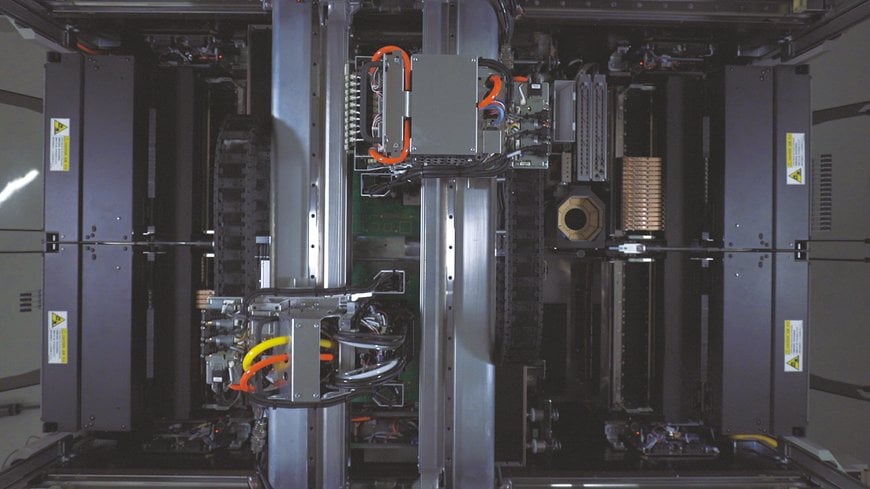
Eine Kombination aus fortschrittlicher Automatisierung und Funktionen, die die Effizienz und Flexibilität erhöhen, kann die Produktivität erheblich steigern. Menschliche Eingriffe werden auf ein Minimum reduziert.
Schaffung einer intelligenteren Welt
Intelligente „Dinge“ werden zu einem festen Bestandteil des Lebens.Die hochautomatisierte Fertigung ist der Schlüssel zur Herstellung der großen Stückzahlen, die zu einem erschwinglichen Preis benötigt werden, um in Haushaltsgeräten, Gebäuden, Fahrzeugen und industriellen Steuerungen eingebaut zu werden.
Die Minimierung menschlicher Eingriffe beim Einrichten und Umrüsten von Hochgeschwindigkeits-Montagelinien für die Oberflächenmontage ist von entscheidender Bedeutung, um Fehler, Verzögerungen und unproduktive Zeiten angehaltener Maschinen zu vermeiden. In Europa, wo Elektronik-Hersteller in der Regel eine Vielzahl von Produkten für industrielle, kommunikationstechnische, medizinische und Automobilanwendungen herstellen, kann eine Verringerung des mit Produktwechseln verbundenen Arbeitsaufwands die Produktivität spürbar steigern.
Es gibt verschiedene wirksame Ansätze, bei denen eine Kombination aus Produktions-Managementsoftware zur Minimierung der bei der Produktumstellung erforderlichen Anpassungen und zusätzlichen, in die Geräte selbst eingebauten Funktionen zum Einsatz kommt. Dadurch können verschiedene Arbeitseinsparungen erzielt werden. Das sind insbesondere der Wegfall mühsamer Aufgaben wie das Wechseln von Bestückungsköpfen, die Automatisierung von Verfahren wie das Setzen von Unterstützungs-Pins sowie Innovationen, die es ermöglichen, Routineaufgaben wie das Nachfüllen von Bauteilrollen ohne Unterbrechungen zu erledigen.
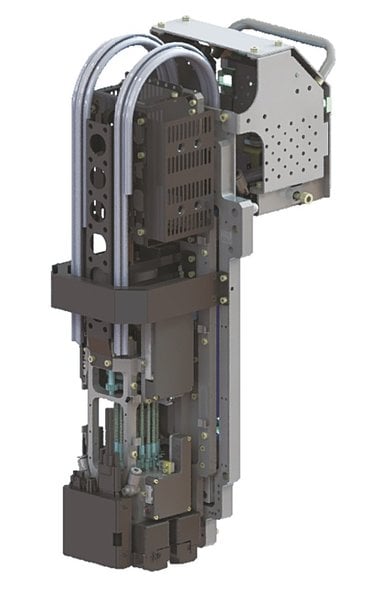
Der Hochgeschwindigkeits-Rotationskopf RM erweitert das Ein-Kopf-Konzept und ermöglicht die Hochgeschwindigkeits-Bestückung eines breiten Bauteilspektrums.
Verringerung der Umrüst-Arbeitsbelastung
Der Einsatz von Software-Werkzeugen zur Erstellung von Produktionsplänen und zur Optimierung der Anlagenauslastung ist hierbei unerlässlich. Von einem Ausrüstungslieferanten zur Verfügung gestellte Werkzeuge können besonders hilfreich sein, wenn die Kontrolle über wichtige Maschinen in der Linie wie Schablonendrucker, Bestücker und Inspektionssysteme konsolidiert werden kann. Diese kann die Gesamtproduktions-Anforderungen und die Fähigkeiten spezifischer Linien und einzelner Maschinen berücksichtigen, um Feeder-Konfigurationen zu schaffen, die die Herstellung mehrerer unterschiedlicher Produkte ohne Umrüstung ermöglichen. Durch geeignete Planung kann die Zahl der in einer bestimmten Schicht erforderlichen Umrüstungen erheblich reduziert werden. Stillstände und manuelle Eingriffe werden minimiert. Es stehen verschiedene Pakete zur Verfügung, wie z. B. Werkzeuge zur Programmierung und Planung, zur Produktionsunterstützung und für die M2M-Zusammenarbeit, die in Yamahas intelligenter Fabriksoftware YSUP enthalten sind.
Um Maschinenstillstände erfolgreich zu minimieren und die Produktivität weiter zu steigern, benötigen die Hersteller jedoch zusätzliche Instrumente. Jedes Mal, wenn ein neues Setup erfordert, dass eine Bestückungsmaschine mit einem anderen Bestückungskopf ausgestattet werden muss, um spezielle Komponenten zu handhaben, oder wenn Feeder ausgetauscht oder einfach ergänzt werden müssen, muss die betroffene Maschine und oft die gesamte Linie angehalten werden, damit qualifizierte Bediener diese Aufgabe erledigen können.
Es gibt verschiedene Ansätze, um dieses Problem zu lösen. Es können mehrere Bestückungsautomaten inline installiert werden, von denen jeder optimal für die Bestückung mit bestimmten Bauteiltypen eingerichtet ist. Ein Chip-Shooter, der für die Bestückung von kleinen, häufig verwendeten Bauteilen wie SMD-Passivbauteilen vorgesehen ist, kann vor einen flexiblen Bestückungsautomaten installiert werden, der ein breiteres Spektrum von Bauteilen verarbeiten kann. Dies mag nicht in allen Fällen ideal sein, da es zusätzliche Investitionen in die Ausrüstung und zusätzlichen Platz in der Fabrik erfordert.
Wenn Investitionsbudgets knapp und Produktionsflächen kostbar sind, können Hersteller davon profitieren, wenn sie einen einzigen, flexiblen Bestückungsautomaten verwenden, der alle Bestückungsanforderungen abdeckt. Hierfür hat Yamaha den Bestücker YRM20 mit neuen Funktionen entwickelt, die die Flexibilität erhöhen und Prozesse automatisieren, die herkömmlicherweise zeitaufwändige, manuelle Eingriffe erforderten.
Der Bestücker basiert auf Yamahas Ein-Kopf-Konzept, das jetzt mit dem Hochgeschwindigkeits-Rotationskopf RM (Bild 1) eine noch höhere Produktivität ermöglicht. Dieser Kopf arbeitet mit einer Bestückungsleistung von 115.0000 CPH und kann Bauteile von 0201 (mm) (SMD-Chips) bis hin zu Teilen von 12 mm x 12 mm und 6,5 mm Höhe platzieren. Er ermöglicht die Bestückung von Bauteilen wie großen LEDs und gängigen IC-Bauformen wie Chip-Scale-Package (CSP), Quad Flat Package (QFP) und Thin Small Outline Package (TSOP) mit extrem hoher Geschwindigkeit. Außerdem gibt es neue, für den RM-Kopf optimierte, Feeder, die die Teile mit hoher Geschwindigkeit zuführen und eine präzise Aufnahme gewährleisten.
Darüber hinaus erweitert Yamahas universeller HM-Kopf das Bauteilspektrum um größere Bauteile wie Elektrolytkondensatoren, BGAs (Ball-Grid-Array) und verschiedene Arten von Steckverbindern. Eine dritte Option, der ultraflexible FM-Kopf, eignet sich für ein noch breiteres Spektrum, einschließlich Odd-Shape-Bauteile und Teile bis zu 55 mm x 100 mm und 30 mm Höhe. Bild 2 zeigt die typischen Bauformen, die die verschiedenen Köpfe handhaben können.
Der Bestücker YRM20 ist in verschiedenen Konfigurationen mit einer oder zwei Traversen (Beams) erhältlich, so dass der Benutzer flexibel zwei Köpfe gleichzeitig betreiben kann. Um den mit einer Zweikopf-Konfiguration möglichen Durchsatz zu maximieren, hat Yamaha die Overdrive-Antriebstechnologie integriert, die sich in der Sigma-Familie von Hochgeschwindigkeits-Bestückern bewährt hat. Dies erhöht die Produktivität, da beide Köpfe mit minimaler gegenseitiger Beeinflussung zusammenarbeiten können (Bild 3). Das ebenfalls auf Basis der Sigma-Technologie entwickelte zweistufige Transportsystem des YRM20 verbessert die Leiterplatten-Unterstützung und verarbeitet Boards mit einer Breite von bis zu 510 mm bei hoher Geschwindigkeit, um die Wechselzeiten erheblich zu reduzieren.
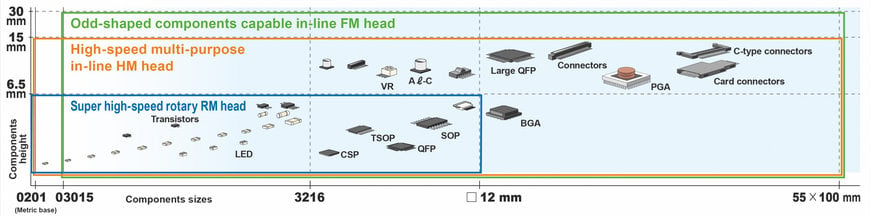
Der RM-Kopf mit 115.000 CPH sowie die HM- und FM-Köpfe decken das gesamte Spektrum oberflächenmontierter Bauteile ab.
Automatisierung von Produktwechseln
Die Automatisierung verschiedener Aspekte der Produktumstellungen trägt ebenfalls dazu bei, menschliche Eingriffe zu reduzieren, um Zeit zu sparen und Fehler zu vermeiden. Die automatische Programmumschaltung erspart dem Bediener die Suche nach dem richtigen Programm zum Laden und ruft stattdessen das richtige Bestückungs-Programm durch Scannen des Barcodes der nächsten zu produzierenden Baugruppe auf. In Verbindung mit einem angetriebenen Werkzeug-Array entfällt durch die Verknüpfung von automatischer Programmumstellung und automatischem Unterstützungs-Pin-Austausch eine weitere, mühsame manuelle Aufgabe beim Produktwechsel.
Darüber hinaus sind selbstladende Feeder erhältlich. Diese ermöglichen dem Bediener einen schnellen Wechsel der Bauteilrollen, wenn diese leer werden. Sie stellen sicher, dass der neue Trägergurt korrekt eingelegt wird, ohne dass die Maschine angehalten werden muss. Mit Yamahas ALF-Auto-Loading-Feeder kann ein neuer Gurt in nur fünf Sekunden eingelegt werden.
Mit dem YRM20-Bestücker hat Yamaha dieses Konzept des Non-Stop-Wechsels nun auch auf Teile erweitert, die normalerweise in Trays präsentiert werden, wie z. B. große ICs und Steckverbinder. Der Non-Stop-Trayfeeder eATS30 führt diese Komponenten kontinuierlich zu und verfügt über ein optimiertes Nachfüllverfahren. Ein einzelnes Tray oder ein komplettes Magazin mit bis zu 10 Trays kann eingelegt werden, ohne dass die Maschine angehalten werden muss, wodurch die Produktivität erheblich gesteigert wird.
Fazit
Durch die Verringerung arbeitsintensiver Einstellarbeiten an den Maschinen, wie z. B. das Wechseln der Bestückungsköpfe und die Ausweitung der Non-Stop-Bauteilnachfüllung auf Tray-Komponenten und Rollen können bisher erforderliche, menschliche Routine-Eingriffe stark reduziert werden. Zu den Vorteilen gehören eine geringere Fehlerquote und eine längere Betriebszeit der Maschinen, was beides zu einer höheren Produktivität beiträgt.
Wenn erfahrene Bediener von diesen einfachen Tätigkeiten entlastet werden, können sie sich auf Aufgaben konzentrieren, die entscheidend von menschlichen Fähigkeiten und Urteilsvermögen abhängen, wie z. B. schnelle Diagnose – und Behebung – der Ursachen unerwarteter Ausfälle, die jederzeit auftreten können. Dazu gibt es zusätzliche Hilfsmittel wie Yamahas QA-Option-Software, die die Vorteile menschlicher Erfahrung und fortschrittlicher Automatisierung kombiniert, um das ultimative Ziel zu erreichen: eine kontinuierlich steigende Produktivität.
Weitere Informationen finden Sie auf Yamahas Website unter at https://smt.yamaha-motor-im.de/.
www.yamaha-motor-im.de
Fordern Sie weitere Informationen an…