www.konstruktion-industrie.com
13
'22
Written on Modified on
Maximale Leistung, höchste Energieeffizienz: Aktuelle Trends bei Wälzlagern für Industriemotoren
NSK hat die mechanischen Verluste von Wälzlagern an Hocheffizienzmotoren unter realen Betriebsbedingungen untersucht. Dazu wurde eine Testmethode entwickelt, die eine direkte Bewertung dieser Verluste erlaubt – mit dem Ziel, die Testergebnisse für ein Entwicklungsprogramm von Wälzlagern für Hocheffizienzmotoren zu nutzen.
Sowohl weltweite Vorschriften als auch der Wunsch der Industrie nach möglichst nachhaltigen Antriebslösungen führen dazu, dass immer häufiger Elektromotoren mit hoher Energieeffizienz bzw. hohem Wirkungsgrad zum Einsatz kommen. Bei der Entwicklung dieser Motoren gibt es aus Sicht der Konstrukteure drei „Stellschrauben“: Eisenverlust (Wärmeerzeugung durch den Eisenkern), Kupferverlust (Wärmeerzeugung durch die Wicklung) und mechanischer Verlust (z. B. durch die innere Reibung der Wälzlager).Reibungsarme Lager für hocheffiziente Motoren
Ein Test mit einem zweipoligen Hocheffizienzmotors bei 3000 Umdrehungen pro Minute ergab beispielsweise, dass der Schmierstoff bzw. dessen Widerstand die Ursache für etwa 80 % des mechanischen Verlustes ist. Daraufhin initiierte NSK ein Entwicklungsprojekt zur Optimierung der Fettart und -menge sowie der Käfigform des Lagers.
Anschließende Tests zeigten, dass allein die Optimierung der Fettmenge die mechanischen Verluste im Vergleich zu herkömmlichen Lagern um 60 % reduziert. Außerdem sind die Low-Torque-Lager von NSK mit einem speziellen Fett befüllt, das in Tests eine um den Faktor 2,7 höhere Lebensdauer bei Schmierstoffverschleiß zeigte. Weitere Tests ergaben, dass der von NSK entwickelte Kunststoffkäfig die mechanischen Verluste im Vergleich zu Stahlkäfigen um die Hälfte reduziert. Das ist vor allem darauf zurückzuführen, dass der Kunststoffkäfig den inneren Widerstand des Fettes zwischen Käfig und Kugeln unterdrückt.
Diese Low-Torque-Lager, die mechanische Verluste reduzieren und eine längere Lebensdauer des Fettes in hocheffizienten Motoren ermöglichen, sind in Größen von 16 bis 170 mm (Außendurchmesser) lieferbar.
Keramikbeschichtete Lager für Umrichtermotoren
Umrichtermotoren ermöglichen eine bedarfsgerechte Antriebsregelung und eignen sich u.a. für Energieeinsparungen bei Pumpen und Gebläsen. Der Trend geht hier zu steigenden Trägerfrequenzen, damit der Motor mit höherer Genauigkeit arbeiten kann. Mit zunehmender Trägerfrequenz kann es jedoch aufgrund des Hochfrequenzstroms im Lager zu elektrolytischer Korrosion kommen.
Bei dieser besonderen Art der Korrosion entstehen Funken zwischen der Laufbahnoberfläche und den Wälzkörpern. Sie dringen durch den Schmierölfilm und verursachen lokale Aufschmelzungen und Riffelbildung sowie, in der Folge, hohe Laufgeräusche oder gar Lagerausfall.
Einige NSK-Wälzlagerbaureihen für kleine Motorleistungen sind mit Keramikkugeln ausgestattet, die dank ihrer isolierenden Wirkung Schutz vor elektrolytischer Korrosion bieten. Bei Kugeln mit größerem Durchmesser, die für Lager von mittleren und großen Umrichtermotoren benötigt werden, bewährt sich als Alternative eine neuartige Keramiksprühbeschichtung des Außenrings.
Die neu entwickelte Baureihe mit einer solchen Sprühbeschichtung weist eine hervorragende elektrische Isolierung auf. Tests ergaben eine etwa zehnmal höhere Isolierung (bei Beaufschlagung mit Gleichstrom) als bei konventionellen allgemeinen keramikbeschichteten Lagern. Unter Wechselstromversorgung wurde eine gleichwertige oder leicht bessere Isolierung gemessen. Bei einer Frequenz von 1 MHz wird eine Impedanz von 100 Ω oder mehr erreicht. Außerdem ist die Schlagfestigkeit der Beschichtung etwa um den Faktor Drei höher.
Die Wärmeableitung – ein Nachteil keramischer Beschichtungen – kann durch die im Vergleich zu herkömmlichen Lagern relativ dichte Beschichtung unterdrückt werden. Das verlängert sowohl die Lebensdauer des Schmiermittels als auch die des Motors. In Tests war der Temperaturanstieg beim Betrieb um etwa 10 °C niedriger als bei herkömmlichen keramikbeschichteten Lagern.
Die neuen keramikbeschichteten Wälzlager von NSK sind in Größen von 130 bis 230 mm Außendurchmesser lieferbar. Sie eignen sich damit für mittlere und große Umrichtermotoren.
Lager mit geringer Partikelemission für Servomotoren
Die präzise Positionierfähigkeit eines Servomotors beruht auf der Übertragung oder Reflexion eines LED-Lichtsignals, das auf die Codierung einer Geberplatte oder –scheibe trifft. Dieses Signal wird ausgelesen und an die Motorsteuerung übertragen. So wird die Ist-Position des Antriebs bestimmt.
Eine Verschmutzung der Oberfläche der Encoderplatte mit Öl oder anderen Stoffen behindert jedoch den Signalempfang und die Rückmeldung der Positionsinformationen an die Motorsteuerung. Unter Umständen ist dann eine korrekte Positionserfassung nicht mehr möglich. Bei Servomotoren für die Robotik kommt als zusätzliches Risiko die Verschmutzung der elektromagnetischen Bremse hinzu.
Aus diesen Gründen – Vermeiden der Verschmutzung von Encoder und Bremse – müssen Lager für Servomotoren eine geringe Partikelemission aufweisen. Deshalb hat NSK eigens für diesen Einsatzzweck eine Lagerbaureihe entwickelt, die ein Schmierfett mit geringer Partikelemission und optimierter Zusammensetzung verwendet. Außerdem kommt bei diesem Lager die reibungsarme DW-Dichtung zum Einsatz, die gerade bei hohen Drehmomenten einen hervorragenden Schutz vor Verunreinigungen bietet.
Vergleichende Testreihen an Servomotoren mit Encoder-Bremsplatten bestätigten, dass bei dem Einsatz von Lagern mit reibungsarmer Dichtung und emissionsarmem LGU-Fett die Codierung wesentlich besser lesbar bleibt (im Vergleich zu Lagern mit berührungsloser Dichtung und herkömmlichem Fett).
Die partikelarmen Wälzlager von NSK mit LGU-Fett und DW-Dichtungen sind in Außendurchmessern von 26 bis 120 mm für alle gängigen Servomotoren erhältlich.
Ziel: Schritt für Schritt zu „Net zero“
Die hier beschriebenen Wälzlagerentwicklungen von NSK für hocheffiziente Umrichter- und Servomotoren leisten einen Beitrag zur Einsparung von elektrischer Energie, was wiederum dazu beiträgt, die Lebenszykluskosten von Maschinen zu senken und die CO2-Emissionen im Rahmen des weltweiten Netto-Null-Ziels zu reduzieren. Dieses Ziel nimmt NSK sehr ernst.
1) Bei den Low-Torque-Lagern von NSK für Hocheffizienzmotoren hat der Anwender die Wahl zwischen mehreren Käfigwerkstoffen.
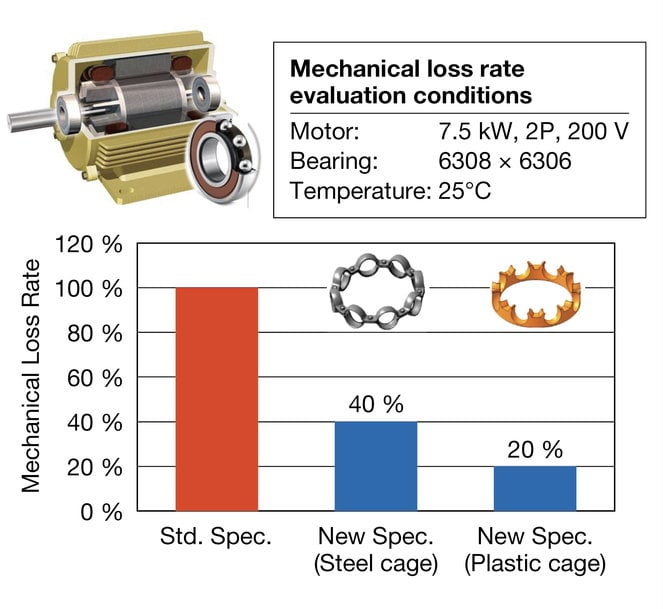
2) Für Umrichtermotoren hat NSK keramikbeschichtete Wälzlager entwickelt. Sie minimieren das Risiko von Elektrokorrosion.
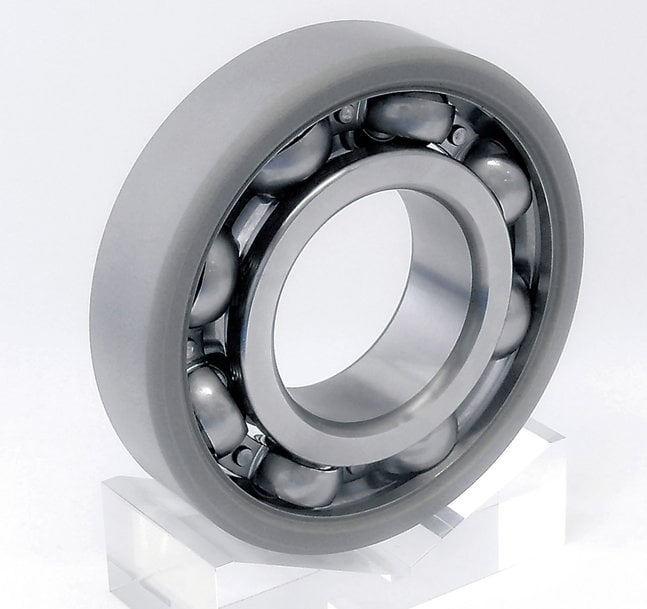
Fordern Sie weitere Informationen an…