www.konstruktion-industrie.com
10
'23
Written on Modified on
Yamaha startet agile Fertigung mit flexiblem Transport
Wie der programmierbare, modulare Werkstücktransport Herstellern hilft, ihre Produktionsleistung zu verbessern.
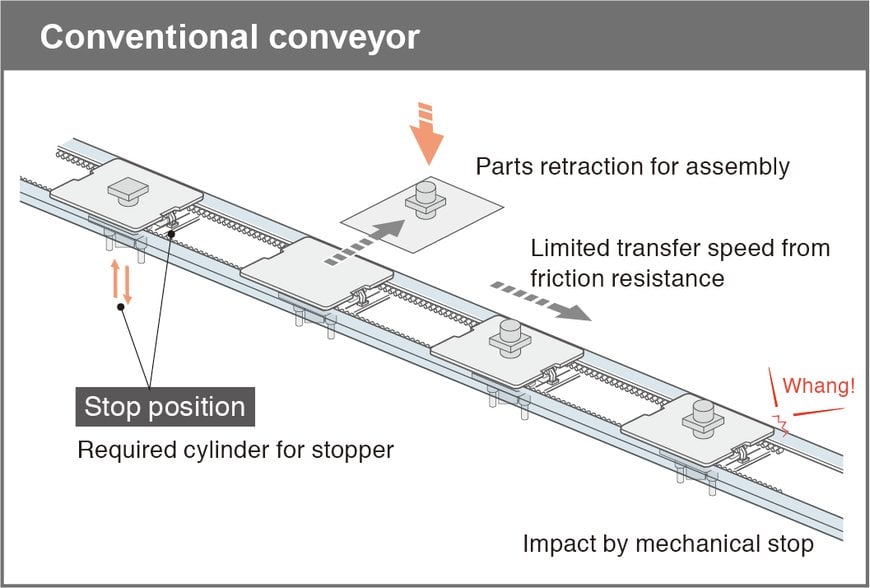
Um den heutigen Marktanforderungen gerecht zu werden, müssen Hersteller Skalierungseffekte erzielen und dabei gleichzeitig flexibel auf sich ändernde Marktanforderungen reagieren können, indem sie den Produktionsausstoß erhöhen und neue Produktvarianten schnell einführen. Flexibilität ist auch unabdingbar, um sicherzustellen, dass Produktionsflächen und Personalressourcen effizient genutzt werden, um permanent eine höhere Produktivität zu erzielen.
Automatisierung trägt entscheidend zur Erzielung von Skaleneffekten bei. Herkömmlichen Maschinen fehlt es jedoch oft an der nötigen Flexibilität, insbesondere bei der Art und Weise, wie Werkstücke zwischen Maschinen bewegt und in die einzelnen Maschinen geladen werden, um die vorgeschriebene Abfolge von Fertigungsprozessen durchführen zu können.
Typischerweise besteht eine Produktionslinie aus einer Kombination von Standard-, Semi-Custom- und Full-Custom-Maschinen, die durch Transportsysteme miteinander verbunden sind. Oft müssen die Transporteinheiten speziell konstruiert oder angepasst werden, wobei die Abmessungen und Konturen häufig vom Layout der Produktionsfläche abhängen. Die Geschwindigkeit eines einzelnen Transportsystems richtet sich immer nach den Geschwindigkeiten der anderen in der Linie sowie nach der Zykluszeit der langsamsten oder längsten Prozesse, so dass oft eine Pufferung erforderlich ist.
Diese Art der Automatisierung schränkt nicht nur die Möglichkeiten zur Individualisierung von Produkten ein. Sie kann auch nur schwer angepasst werden, um beispielsweise die Produktion zu beschleunigen, das Produktionsvolumen zu erhöhen oder die Produktionsflächen in der Fabrikhalle neu zuzuordnen.
Yamaha hat bereits einigen Herstellern aus verschiedenen Industriebereichen wie Automobil-Baugruppen, Industrieelektronik und Lebensmittelverpackungen geholfen, die bekannten Nachteile der herkömmlichen Automatisierung zu überwinden. Vier Kunden berichten nun über ihre Erfahrungen mit Yamahas Linearmodulen LCMR200 in Verbindung mit SCARA- und kartesischen Robotern, nachdem sie Vorteile wie kürzere Zykluszeiten, größere Effizienz und höheren Ausstoß erzielt haben.
Gesteigerte Produktivität in jeder Linie
Ein Automobilzulieferer, der seine Produktivität steigern wollte, stieß dabei auf typische Hindernisse, die eine herkömmliche Automatisierungstechnik mit sich bringt. Die Betriebseigenschaften mechanischer Stopper und pneumatischer Zylinder führen zu einer langen Positionierungszeit des Werkstückträgers an jeder Arbeitsstation. Außerdem sind Puffer zwischen den Arbeitsstationen erforderlich, und die Linie musste häufig für kurze Zeit angehalten werden, um kleinere Probleme zu beheben.
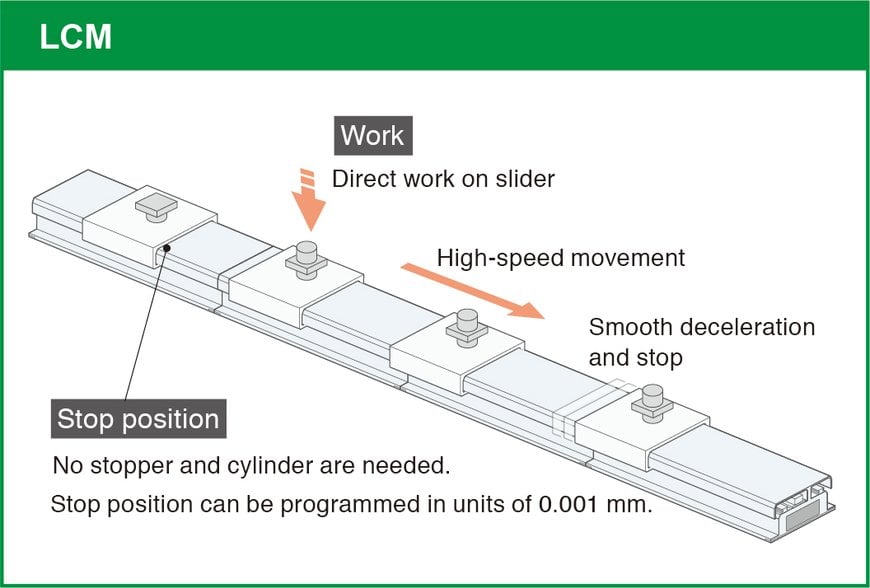
Typische Optionen für einen Hersteller in dieser Situation sind die Erhöhung der Anzahl der Produktionslinien, die Beschleunigung des Maschinentakts, um Bearbeitungszeiten zu verkürzen oder die Erhöhung der Werkstück-Transfergeschwindigkeit zwischen einzelnen Prozessstationen.
Durch die Überarbeitung der Produktionslinie, bei der herkömmliche Fördersysteme durch LCMR200-Module ersetzt wurden, konnte die Transferzeit verkürzt werden. Darüber hinaus wurden durch die flexible Einstellung der Transfergeschwindigkeit Puffer eliminiert. Das LCMR200 stoppt schnell an einer genau definierten Position, sodass die effektive Transferzeit zwischen den Prozessen deutlich reduziert wurde. Die Montageprozesse können direkt auf dem Schlitten des LCMR200 durchgeführt werden, was die Zykluszeit des Prozesses spürbar verkürzt.
In diesem Beispiel wurde die Transferzeit von zwei auf 0,7 Sekunden verkürzt. Als Ergebnis konnte dieser Kunde sein Produktionsvolumen um 23 Prozent steigern, ohne seine Montageprozesse umgestalten zu müssen. Außerdem wurden die Kosten für Werkstückträger eingespart, die zuvor für den Transport der Werkstücke auf ihren Transportsystemen benötigt wurden.
Verringerter Umrüst-Arbeitsaufwand
In einem anderen Beispiel hat der Hersteller eines breiten Portfolios kleiner Elektromotoren vom LCMR200 profitiert, indem er Zeit sparte, die vorher für die Umstellung der Produktionslinie für verschiedene Modelle aufgewendet werden musste. Dieser Kunde hatte die Produktion bereits optimiert, um die Umrüstfrequenz und den Arbeitsaufwand bei jeder Umrüstung zu minimieren. Die Möglichkeiten für weitere Verbesserungen waren aufgrund des Zeitaufwands für die Anpassung der Stopper-Positionen und den erforderlichen Wechsel der Werkstückträger sehr begrenzt. Außerdem beinhaltet jede manuelle Umrüstung ein gewisse Fehlerwahrscheinlichkeit.
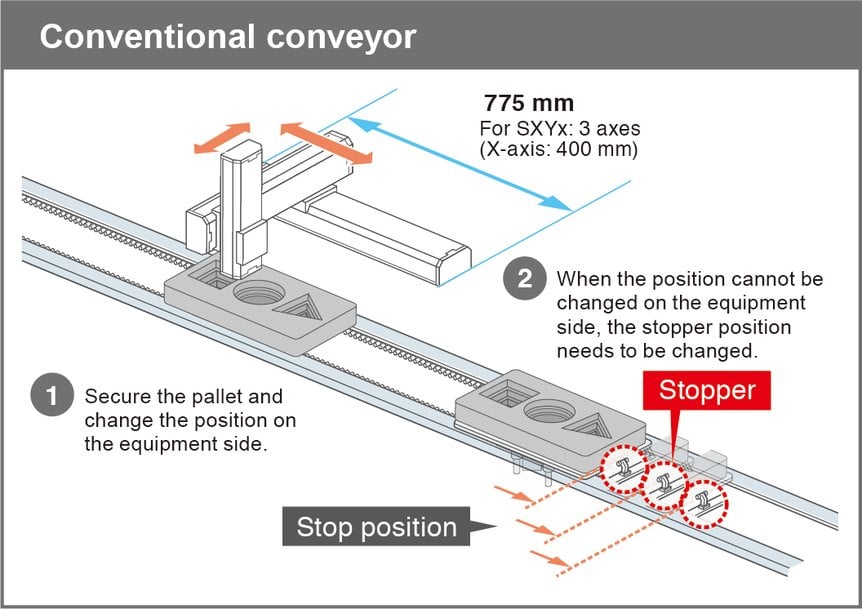
Durch den Einsatz des modularen LCMR200-Transportsystems konnte die Umrüstzeit auf nahezu Null reduziert werden, da die Haltepositionen durch einfaches Umprogrammieren geändert werden können und somit keine physischen Umrüst-Änderungen mehr erforderlich sind. Die Flexibilität der neuen Module ermöglichte es dem Unternehmen, ein vereinheitlichtes Werkstückträger-Design für alle Produktvarianten zu verwenden und so den Wechsel von Trägersystemen überflüssig zu machen, was Ineffizienz und Fehlerquellen eliminierte.
Insgesamt konnten durch den Einsatz des LCMR200 16 Stunden Produktionszeit zusätzlich gewonnen werden, die zuvor jeden Monat bei Produktwechseln verloren ging.
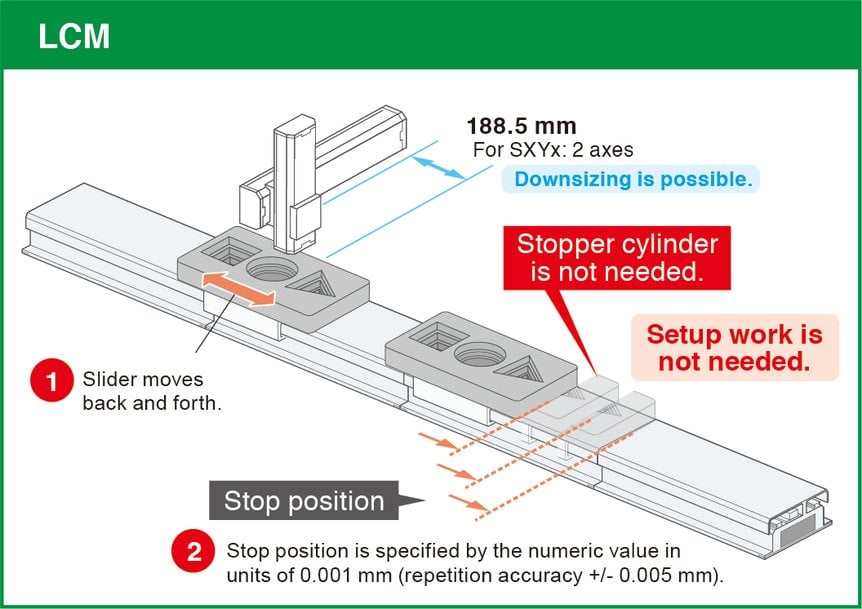
Vereinfachte Personalverwaltung
Ein drittes Beispiel aus der Lebensmittelindustrie zeigt, wie ein Unternehmen, das Süßgebäck verpackt, den LCMR200 einsetzt, um die Herausforderung zu meistern, jederzeit die richtige Anzahl von Mitarbeitern an der Produktionslinie zu haben. In Stoßzeiten können bis zu acht Mitarbeiter benötigt werden. Für die Verantwortlichen war es oft schwierig, zu diesen Zeiten genügend Arbeitskräfte hierfür zur Verfügung zu haben. Umgekehrt gab es meist einen Überschuss an Arbeitskräften, wenn nur eine kleine Menge verpackt werden sollte.
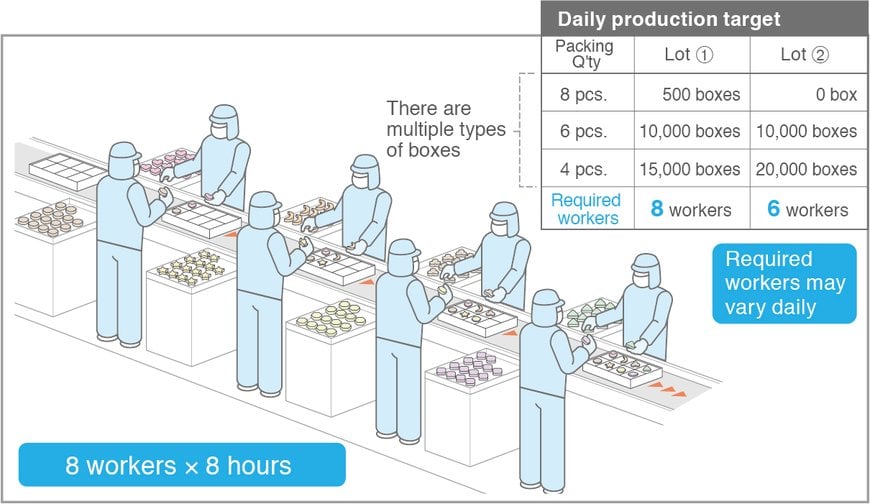
Durch den Einsatz von LCMR200-Modulen, einschließlich der innovativen horizontalen Transfereinheit, konnte ein Mitarbeiter die Gebäckstücke direkt aus dem Backprozess an zwei Reihen von SCARA-Robotern übergeben, die sie in einzelne Kartons verpackten, die dann versiegelt und für den Versand an Einzelhändler zusammengestellt wurden.
So konnte das Unternehmen die Herausforderungen bei der Personalverwaltung meistern. Drei fest angestellte Mitarbeiter sorgen nun im Wechsel für eine 24-Stunden-Produktion, um die hohe Marktnachfrage nach den leckeren Backwaren zu befriedigen.
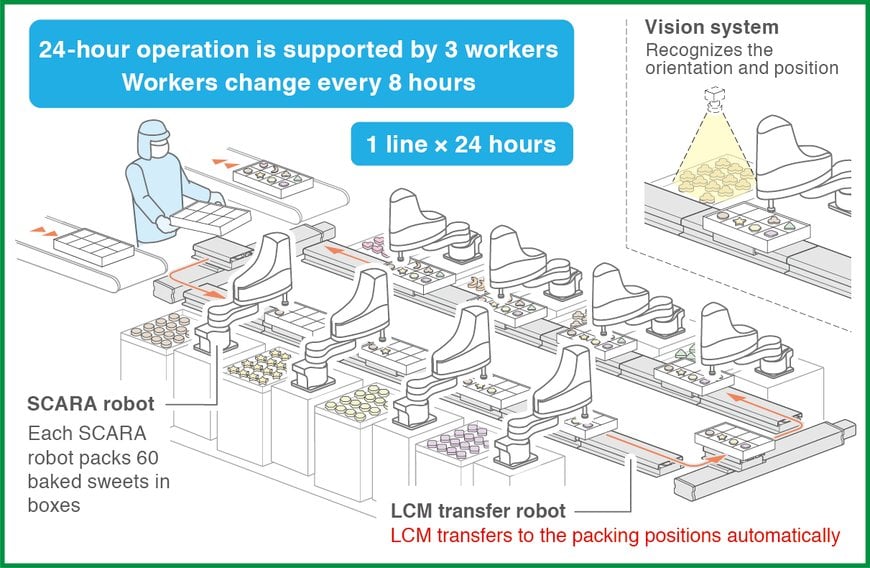
Einfachere Überwachung und Wartung
Ein anderes Unternehmen, das Automobil-Baugruppen herstellt, verwendete Rundschalttische, um Werkstücke in einer vorgegebenen Reihenfolge zwischen Montagerobotern zu bewegen. Rundschalttische haben mehrere Nachteile: Automaten für die Montage stehen dicht an dicht, was den Zugang für die Produktionsverantwortlichen einschränkt. Außerdem ist es schwierig, Haltepositionen zu wechseln und eventuelle Geräteausfälle können zu großen Verzögerungen führen.
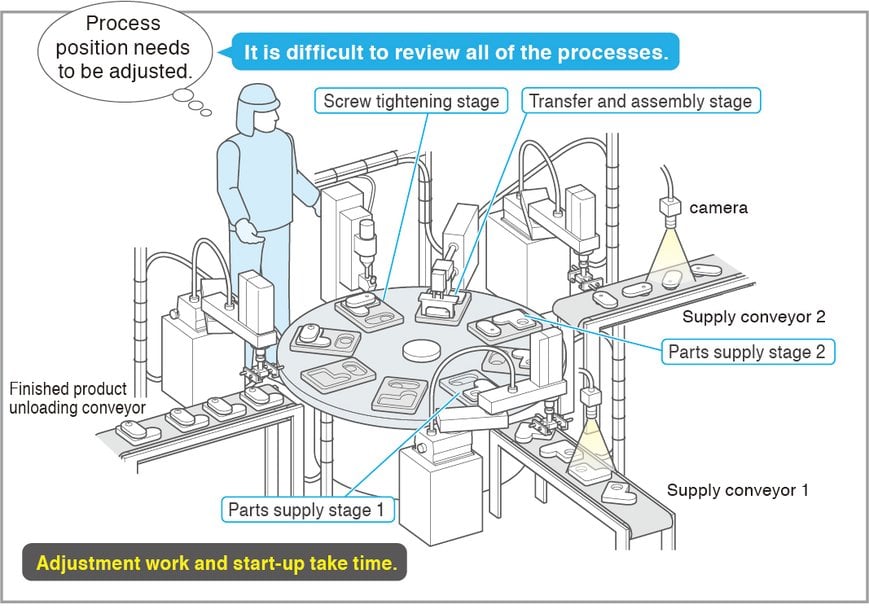
Durch den Einsatz von LCMR200-Modulen, einschließlich des Vertikaltransportmoduls, hat dieses Unternehmen eine Inline-Produktion realisiert, die leichter zu überwachen ist und gleichzeitig von hoher Positioniergenauigkeit und Präzision profitiert. Das Transportmodul LCMR200 erleichtert die Feinjustierung aller Stopp-Positionen.
Darüber hinaus wird die Planung und Installation der Anlage durch die hohe Positionsgenauigkeit und Flexibilität des LCMR200 wesentlich vereinfacht, während die modulare Bauweise auch die Wartung und Störungsbehebung erleichtert.
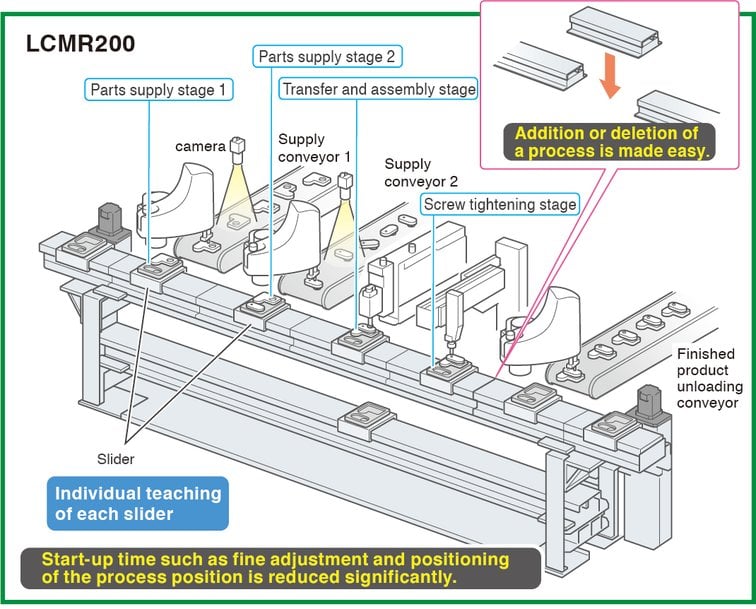
Fazit
Die industrielle Fertigung von heute erfordert Agilität, um sich an die Anforderungen des Marktes und manchmal sogar an die individuellen Bedürfnisse einzelner Kunden anzupassen. Herkömmliche Automatisierungslösungen lassen sich oft nur langsam installieren und nur schwer anpassen und skalieren, um die Produktivität zu verbessern und den Ausstoß zu erhöhen, falls dies erforderlich ist.
Eine flexible Lösung für den Werkstücktransport, wie Yamahas LCMR200, bietet die Grundlage für eine Automatisierung, die schneller implementiert, einfacher rekonfiguriert und leichter skaliert werden kann. Die Programmierung der Module mit demselben grafischen Softwaretool wie bei den anderen Robotern in der Produktionslinie trägt zusätzlich zu diesen Vorteilen bei und erleichtert die Auslegung und Konfiguration der Linie.
www.yamaha-motor-robotics.com
Fordern Sie weitere Informationen an…