www.konstruktion-industrie.com
29
'20
Written on Modified on
Bildverarbeitung für den ganz großen Bohrer
Zur Beurteilung des Gesteins und des Baufortschritts sowie für die geologische Dokumentation beim Tunnelbau hat die Montanuniversität Leoben in Österreich ein robustes Bildaufnahmesystem entwickelt und setzt dafür Bildverarbeitungskomponenten von STEMMER IMAGING ein.
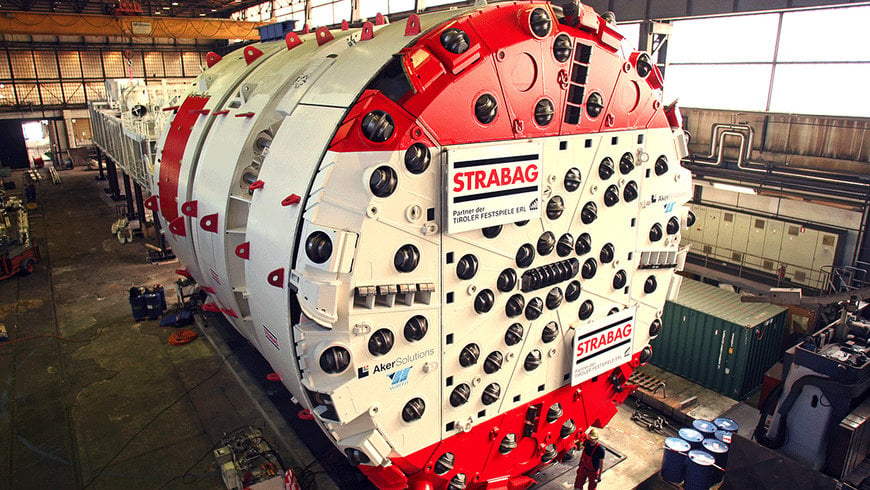
Mit Bohrkopfdurchmessern von bis zu 15 Metern und Längen bis zu mehreren Metern zählen moderne Tunnelvortriebsmaschinen (TVM) zu den größten Werkzeugen weltweit. Diese gigantischen Maschinen werden zum Bohren von Tunneln wie beispielsweise des Brenner Basistunnels eingesetzt und schaffen die Voraussetzungen für eine bessere Infrastruktur des Schienen- und Autoverkehrs.
Fester Bestandteil bei der Durchführung von Tunnelbauprojekten ist eine zuverlässige geologische Kartierung. Mit ihr wird die Beschaffenheit des im Tunnelquerschnitt liegenden abzubauenden Gesteins so vollständig wie möglich erfasst, um Informationen zum Baufortschritt zu dokumentieren und bei Bedarf Gründe für eventuelle Verzögerungen und die damit verbundenen erhöhten Kosten nachweisen zu können. Gesteinsformationen, die fester als erwartet sind, können beispielsweise dazu führen, dass die Vortriebsgeschwindigkeit hinter der Planung zurückbleibt und der Verschleiß der so genannten Disken, also der eigentlichen Abbauwerkzeuge, zunimmt.
Schlechte Zugänglichkeit
Im konventionellen Tunnelbau führen in der Regel Geologen diese geologische Kartierung durch, indem sie in regelmäßigen Abständen manuell mit Handskizzen oder Bildern die Beschaffenheit des Gesteins dokumentieren. Beim Einsatz von Tunnelvortriebsmaschinen ist dies nicht so einfach möglich, da die Schneidköpfe nur wenige Öffnungen zur Ortsbrust aufweisen und deren Einsehbarkeit somit stark eingeschränkt ist.
„Die Vortriebsgeschwindigkeiten von TVMs können deutlich über denen konventioneller Tunnelvortriebe liegen, doch der Entwicklungsstand der notwendigen geologischen Dokumentation der Ortsbrust hinkt bei diesen modernen Anlagen aufgrund der schlechten Zugänglichkeit erheblich hinterher“, erläutert Robert Wenighofer vom Lehrstuhl für Subsurface Engineering an der Montanuniversität Leoben in Österreich.
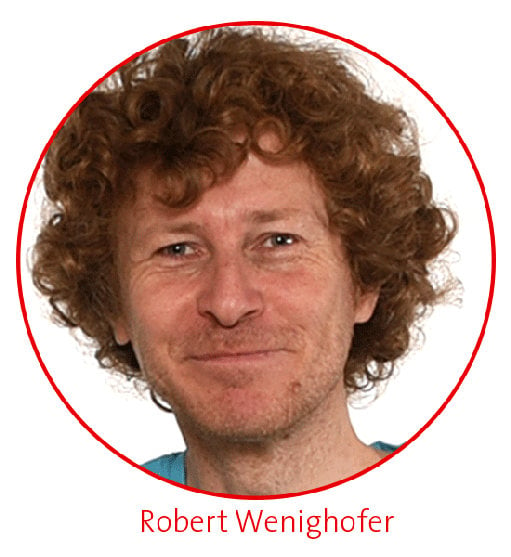
Um diese Situation zu verbessern hat das Institut der Montanuniversität gemeinsam mit Geodata, einem in Leoben ansässigen, auf Tunnelvermessungen spezialisierten Unternehmen, eine neue Herangehensweise entwickelt: Statt der bei Tunnelvortriebsmaschinen aus Platzgründen schwierigen manuellen Beurteilung sorgen in einem Bohrkopf montierte, kamerabasierte Aufzeichnungssysteme für die Aufnahme von Bilddaten, die als Basis für die geologische Kartierung dienen.
Dies ist natürlich nicht im realen Bohrbetrieb möglich, so Wenighofer: „Während einer Bohrung lassen weder die mechanischen Kräfte noch die Staubentwicklung die Aufnahme des nötigen Bildmaterials zu. Die Anlagen müssen jedoch regelmäßig gewartet werden oder stehen z.B. zur Verlängerung der Förderbänder zum Abtransport des entfernten Gesteins immer wieder still. In solchen Vortriebspausen besteht dann die Möglichkeit, das System zu montieren und Aufnahmen der Ortsbrust durchzuführen.“
Bis zu drei Kameras
Zur Vorbereitung wird dabei zunächst der Bohrkopf einige Zentimeter zurückgefahren sowie das angefallene Gestein und der Staub aus dem Zwischenraum zwischen Bohrkopf und Ortsbrust entfernt, um den Kameras freie Sicht zu verschaffen. Bis zu drei Kameras in stabilen Schutzgehäusen werden anschließend in verschiedenen Abständen zum Mittelpunkt des Bohrkopfes in vorhandene Diskenkästen montiert und mit der zugehörigen Steuereinheit für die Erfassung vorbereitet. „Die Installation in den Diskenkästen ermöglicht, dass Tunnelvortriebsmaschinen ohne zusätzliche Öffnungen mit dem Kamerasystem ausgerüstet werden können“, betont Wenighofer.
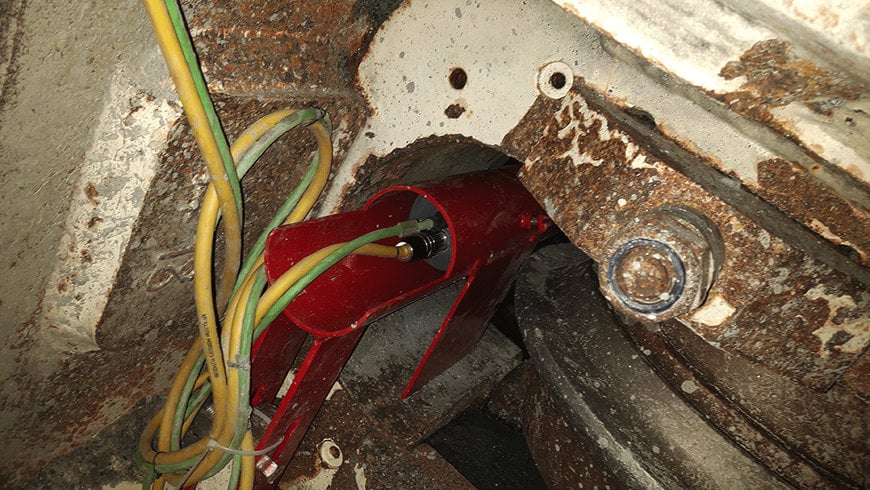
Zur Bildaufnahme wird der Schneidkopf manuell etwas mehr als 360° ohne Anpresskräfte gedreht. Die eingesetzten Kameras erfassen dabei über 1000 Bilder, die an die Steuereinheit überspielt und dort abgespeichert werden. Auf Basis dieser Bilder erfolgt später die 3D-Rekonstruktion der an dieser Stelle vorgefundenen geologischen Verhältnisse unter Einsatz von Stitching- oder Fotogrammetrie-Methoden. „Anfangs nahmen wir die Bilder nur aus einer einzelnen Öffnung auf, während der Schneidkopf gedreht wurde“, beschreibt Wenighofer die ersten Versuche mit dieser Technologie.
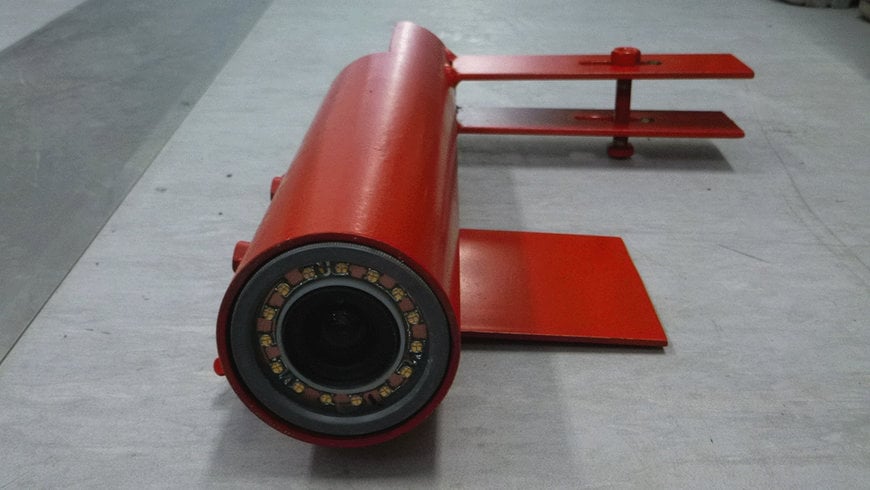
Mit dieser Vorgehensweise konnten jedoch nur schmale, ringförmige Streifen der Ortsbrust erfasst werden, was keine ausreichenden Aussagen über den Gesamtzustand zuließ und jeweils ein Ummontieren der Kameras an Positionen mit anderem Abstand zum Mittelpunkt erforderte. Mit der neuen Lösung ist das Aufnahmesystem nun auch für Tunnelvortriebsmaschinen großer Durchmesser adaptierbar. Bei geeigneter Auslegung der optischen Eigenschaften und Flexibilität, den Bohrkopf zurückziehen zu können, genügt selbst bei großen Bohrdurchmessern in der Regel ein System aus drei Kameras, um die gesamte Ortsbrust in einem Umlauf zu erfassen.
Lösung für ein raues Umfeld
Die Umgebungsbedingungen in einer Tunnelbaustelle sind extrem rau: Temperaturen von bis zu 40 °C, eine hohe Luftfeuchtigkeit und viel Staub stellen für die Bilderfassung eine besondere Herausforderung dar. Während der ersten Anläufe, ein geeignetes System zusammenzustellen, stieß Wenighofer im Jahr 2014 auf STEMMER IMAGING:
Bei der Auswahl geeigneter Komponenten haben uns die Experten mit Ihrer Erfahrung sehr unterstützt und haben sich auch schnell in das für sie fremde Terrain des Tunnelbaus mit den dortigen Besonderheiten eingearbeitet.
So fanden die Partner unter anderem gemeinsam eine Lösung für das Problem, dass nach dem Vortrieb im Bohrkopf hohe Temperaturen und Feuchtigkeit herrschen, was zu einem Beschlagen der vergleichsweise kühlen Kameraeinheit führt und somit die Aufnahme verzögert. Zur Abhilfe kann das Kamerasystem nun schon vor dem Einbau mit Strom versorgt werden, erreicht dadurch die geeignete Betriebstemperatur und akklimatisiert sich somit schneller im Schneidkopf.
Das gesamte System besteht aus einer leicht und flexibel montierbaren Kameraeinheit in einem robusten Schutzgehäuse, in dem eine 2 Megapixel-Industriekamera von Allied Vision, ein 5 mm-Objektiv mit fester Brennweite und ein speziell entwickelter LED-Ring zur Beleuchtung integriert sind.
Die Blende ist auf einen Tiefenschärfebereich von etwa 40 bis 200 cm eingestellt, um auch tiefe Gesteinsausbrüche erfassen zu können. Der LED-Ring ist mit einer Leuchtstärke von über 10.000 Lumen ausgelegt. Eine Blitzdauer von 4 ms und die Helligkeit sorgen dafür, dass die für die nachfolgende fotogrammetrische Verarbeitung erforderliche Bildqualität erreicht wird.
Durch den Blitzbetrieb wird auch die Bewegungsunschärfe vermieden, die sich aus der Drehung des Bohrkopfes ergeben könnte. Die Kamera ist auf eine kontinuierliche automatische Belichtung eingestellt, wodurch die Belichtungszeit für jedes Bild aktualisiert wird. So lässt sich eine Über- oder Unterbelichtung der Ortsbrustabschnitte vermeiden, was eine weitere Voraussetzung für aussagekräftige Ergebnisse der fotogrammetrischen Bildverarbeitung darstellt.
Ausgeklügeltes System
Der zweite Teil des Systems ist eine Steuereinheit, die während der Dauer einer Aufnahme an einer Position in einem Doppeldiskenkasten oder einem Mannloch montiert verbleibt. Sie enthält einen PC, eine Energieversorgung, einen einaxialen Neigungssensor und verfügt über Schnittstellen für den parallelen Betrieb mehrerer Kameras.
Um eine ausreichende Überlappung und einen Überschuss an Bildern zu erhalten, löst die Steuerung die angeschlossenen Kameras mit einer konstanten Rate von 2 Bildern je Sekunde aus. Sie ist so eingestellt, dass die Bildaufnahme automatisch nach dem Booten des PCs startet. Direkte Eingaben in das System sind nicht erforderlich, Interaktionen mit der Kamerasteuerung unter den harschen Bedingungen am Schneidkopf sind weitgehend unnötig. Als Besonderheit kann der PC mit einem Android-Gerät wie z.B. einem Smartphone ferngesteuert werden. Auf diese Weise ist eine schnelle Beurteilung der Bildqualität möglich.
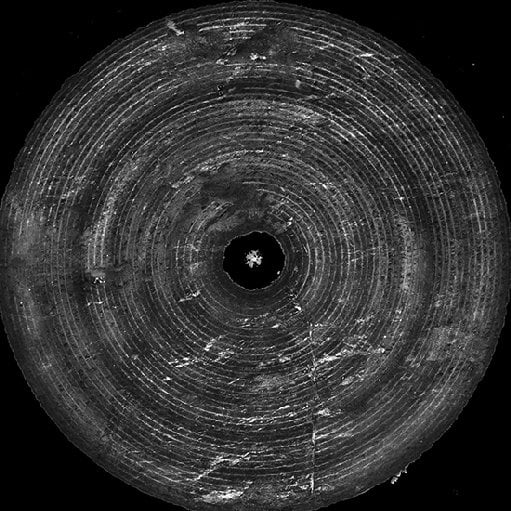
Durch das Zusammenfügen aller Bilder entstehen hochauflösende Orthofotos.
Der Neigungssensor der Steuereinheit hat die Aufgabe, ein gemeinsames Koordinatensystem für alle in einer Messkampagne aufgenommenen Bilder zu erstellen. Jedem Bild wird dabei ein vom Neigungssensor abgerufener Winkelwert zugewiesen, wenn eine Kamera ein Bild aufnimmt. Aus diesem Winkel und der bekannten Relativposition des Diskenkastens lässt sich die absolute Position der Kamera im 3D-Referenzkoordinatensystem des Schneidkopfes bestimmen, was eine wesentliche Voraussetzung für die nachfolgende fotogrammetrische Verarbeitung darstellt.

Farbkodierte Reliefdarstellungen zeigen die Position und Tiefe von Ausbrüchen.
Für diese Auswertung nutzt das System interessanterweise eine Software zur Verarbeitung von Bilddaten aus dem Luftfahrtbereich, mit der die große Anzahl an Bildern in Kombination mit den Orientierungsdaten gematcht werden kann, um eine Punktwolke der gesamten Ortsbrust zu berechnen. Aus dieser lassen sich dann ein so genanntes Orthofoto und die Interpolation eines digitalen Höhenmodells ableiten, mit deren Hilfe die benötigte geologische Kartierung und Auswertung realisiert werden kann.
Erfolgreiches Patent
Das System zur Aufnahme und Auswertung von Bildern hat sich inzwischen in verschiedenen Tunnelbauprojekten bestens bewährt und wurde Ende 2019 erfolgreich patentiert.
STEMMER IMAGING hat uns auf dem Weg dorthin hervorragend begleitet und bei Weiterentwicklungen wie beispielsweise der zeitgleichen Ansteuerung mehrerer Kameras über Software-Trigger in entscheidender Weise unterstützt.freut sich Wenighofer über die erzielten Fortschritte.
„In Tunnelbauprojekten werden damit die nötigen Auswertungen erleichtert und beschleunigt. So lassen sich durch die großflächigen Aufnahmen der Ortsbrust beispielsweise die Position und das Volumen von Gesteinsausbrüchen überhaupt erst zahlenmäßig erfassen. Je besser man die Rauigkeit der Ortsbrust kennt, desto genauer lassen sich auch der Verschleiß der Disken und asymmetrische Belastungen von Schneidköpfen analysieren und Aussagen über die Lebensdauer und die Materialermüdung der Schneidwerkzeuge treffen.
Ganz wesentlich ist zudem, dass die digitale Ortsbrustaufnahme eine objektivere geologische Kartierung erlaubt, die eine unwiderlegbare Grundlage der geologischen Beurteilung für Auftraggeber und Auftragnehmer darstellt. Die enge Zusammenarbeit mit STEMMER IMAGING bei der Entwicklung des Systems war daher für uns ungeheuer hilfreich.“
www.stemmer-imaging.com
Fordern Sie weitere Informationen an…