www.konstruktion-industrie.com
05
'22
Written on Modified on
EMCO: MEGAMILL BRINGT BYSTRONIC ERHEBLICHE PRODUKTIVITÄTSTEIGERUNG
Ein sauber strukturierter Produktionsprozess, mit exakt eingetakteten Fertigungsabläufen und zuverlässig arbeitenden Fertigungssystemen, ist eine der Hauptvoraussetzungen für Produktivität und Lieferbereitschaft im Werkzeugmaschinenbau. Erreichbar ist dies nur, wenn Kunde und Lieferant in der Produktionskette gemeinschaftlich zielgerichtet Projekte angehen.
So geschehen bei der Bystronic Laser AG in Niederönz, Schweiz, im Projekt einer neuen Fertigungslinie bei der Bearbeitung von Maschinenrahmen für Laserschneidmaschinen.
Die Bystronic Laser AG ist ein weltweit führendes Technologieunternehmen im Bereich Blechbearbeitung, speziell bei Laserschneidsystemen. Zusammen mit der EMCO GmbH aus
Hallein / Salzburg wurde die Bearbeitung der Maschinenrahmen neu konzipiert und konnte jetzt durch die Hoch- Portalfräsmaschine Megamill von Emco Mecof voll übernommen werden.
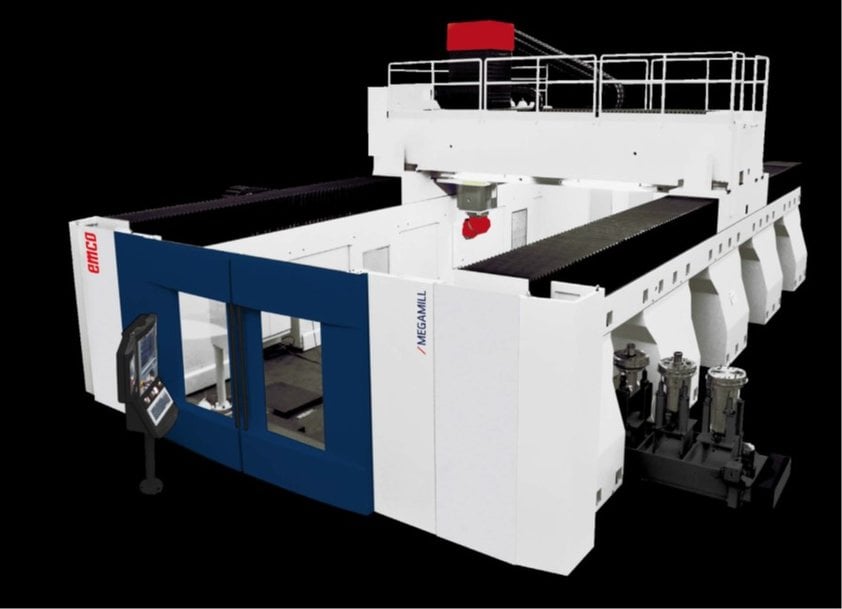
Portalfräsmaschine MEGAMILL im Dauerlauf an Maschinenrahmen
Neue Partnerschaft leben
„Die Stückzahlen an Maschinenrahmen waren derartig gestiegen, sodass ich mit meiner vorhandenen Fertigungskapazität nicht mehr zurechtkam. Wir suchten daher eine neue Maschine, die den Output hat, unsere hohen Qualitätsanforderungen zu erfüllen und flexibel einsetzbar ist“,
so die Aussage von Raphael Kopp, Leiter der Fertigung bei der Bystronic Laser AG.
Raphael Kopp hatte klare Vorstellungen von dem was die „Neue“ mitbringen musste, nämlich hohe Produktionsstückzahl pro Monat, eine perfekte Genauigkeit beim Ebenenfräsen der Führungsflächen im Maschinenrahmen (Ebenheit von 0,05 mm auf einer Führungsbahnlänge von 3-4 m) und Flexibilität zum Einsatz an verschiedenartigen Baugruppen. Vor allem musste auch die Dimension des Maschinentisches ausreichend groß sein, denn die Systembaugruppen an den Laserschneidanlagen erfordern den entsprechenden Platz.
Die Suche am Markt begann und neben Herstellerbesuchen und der Begutachtung von Testbearbeitungen war nach nicht mal vier Monaten klar, dass die neue Maschine eine Megamill
von Emco Mecof sein soll. In enger Abstimmung wurden in dieser Zeit die wichtigen Randbedingungen für den Kauf der Maschine definiert und geprüft, sowie die Machbarkeit
nachgewiesen.
Zur Kaufentscheidung meint Raphael Kopp, „ausschlaggebend war sicher der Pendelbetrieb, d.h. auf dem Maschinentisch können wir jetzt zwei Werkstücke spannen, eines wird bearbeitet, das zweite wird parallel dazu eingelegt, ausgerichtet und gespannt. Ist Teil 1 fertig fahren wir mit dem
Fräskopf auf die zweite Tischhälfte und starten den neuen Job. Die Maschine bleibt sozusagen „ im Span“. Das bringt uns enorme Einsparung an Fertigungszeit pro Rahmen“.
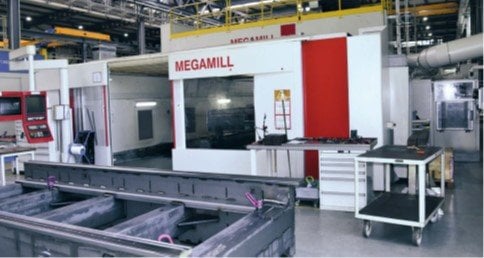
Die Megamill eingebunden in den Fertigungsprozess bei der Bystronic Laser AG.
Fertigungsprozess „just-in-time“
Die Anforderungen an den Fertigungsdurchlauf bei Bystronic sind hoch. Die Herstellzeit für eine Laserschneidmaschine vom automatisierten Schweißen des Maschinenrahmens über das Fertigen, Lackieren, Montieren, Qualitätsprüfen, Inbetriebnehmen bis zur Versandbereitschaft liegt bei 15 Arbeitstagen.
Allein die Fertigung eines Maschinenrahmens bis zum lackierten Bauteil muss in fünf Arbeitstagen getätigt sein.
Dabei wird an der MegaMill in drei Schichten gearbeitet, wobei eine Schicht unbemannt läuft. Die Maschinenrahmen, in fünf unterschiedlichen Größen vorhanden, mit einem Gewicht von ca. 5 t werden in 12 bis 16 Stunden in einer Aufspannung fertig bearbeitet.
Die Komplettbearbeitung läuft in drei Schritten ab:
/ Schruppen: Fertigungszeit ca. 5 Stunden; zwischenlüften der Teilespannung um Bauteilspannungen zu eliminieren
/ Vorschlichten: Setzen aller Merkmale, Bohrungen, Gewinde, etc.
/ Schlichten: Hochgenaues Bearbeiten der Führungsflächen (Ebenheit von 0,05mm /4m) und Bezugsmaße
Die Fertigung muss prozesssicher sein, denn Störungen und Fehler, längere Maschinenstillstände von mehr als einem Tag können bei diesem umfangreichen Fertigungsspektrum erhebliche Kosten verursachen, und eine Lagerhaltung von schon fertigbearbeiteten Maschinenrahmen gibt es nicht.
Prozessschritte müssen deshalb immer „just-in-time“ ablaufen.
Megamill – die Maschine mit Potential für den Kunden
Die Megamill ist ein Hochportal-Fräszentrum mit oben liegender Gantry, prädestiniert zur Bearbeitung großer Werkstücke für Anwendungen z.B. in Werkzeug und
Formenbau, im allgemeinen Maschinenbau und in der Luft- und Raumfahrtindustrie. Die Maschine kann mit ihren Systembaugruppen kundenspezifisch konfiguriert werden.
Hier bei Bystronic ist sie mit einer Tischlänge (X-Achse) von 15.000 mm und in der Querachse (Gantry- Y-Achse) von 5.000 mm ausgeführt. Der Z-Schieber (RAM ) macht einen Weg von 1.750 mm. Bystronic hat sich für einen Universal-Fräskopf aus dem sehr umfangreichen Fräskopf-Sortiment bei
Emco Mecof entschieden. Auch deswegen, weil der 2-achsige Kopf mit einem Drehmoment bis 1.000 Nm und 8.000 rpm genau die Fertigungsanforderungen beim Schruppen und Schlichten erfüllt und aufgrund seiner kompakten Form sehr gut die komplexen Zugänglichkeiten an der Rahmenkontur
problemlos anfahren kann. Dynamisches Anfahren der Positionen spart Zeit bei einer 16-stündigen Bearbeitung.
„Ein schneller Eilgang in den Achsen und die Dynamik im Fräskopf bringen uns zählbare Einsparungen in der Bearbeitungszeit, gerade wenn wir am Bauteil mehr als 50 Bohrungen anfahren müssen“ stellt Raphael Kopp fest.
Auch die Zahnstangenantriebe in X- und Y-Achse, ausgestattet mit je zwei Motoren, die im Master-Slave-Verband angesteuert werden, bringen Dynamik in den Prozess. Ein Highlight ist natürlich die Pendelbearbeitung auf dem Tisch. Dabei sind die Arbeitsräume sicherheitstechnisch bzgl.
Spänefall und Eingriffsmöglichkeit gegeneinander abgesichert. Auf der einen Seite wird gerüstet, während der Fräskopf auf der anderen Seite arbeitet. Die Megamill wird für diesen Anwendungsfall mit zwei Bedienpanels ausgerüstet, und zwar auf beiden Seiten des Tisches kann die Bedienperson
eingreifen und spart damit unnötige Wegzeiten.
Die Box-in-Box-Bauweise des beweglichen Querträgers ist eine weitere Stärke der Maschine. Box-in-Box-Führung bedeutet, die Vertikalachse des RAM ist mit seinen 4-fach Linearführungen an der oberen und unteren Seite des Querträgers „eingespannt“. Diese steife, FEM-gerechnete Baugruppe garantiert die Einhaltung der hohen Anforderungen an die Werkstückqualität, wie sie beim Schlichten der Führungsbahnen am Maschinenrahmen gefordert ist.
Die Maschine ist komplett gekapselt und mit einer Absauganlage ausgerüstet.
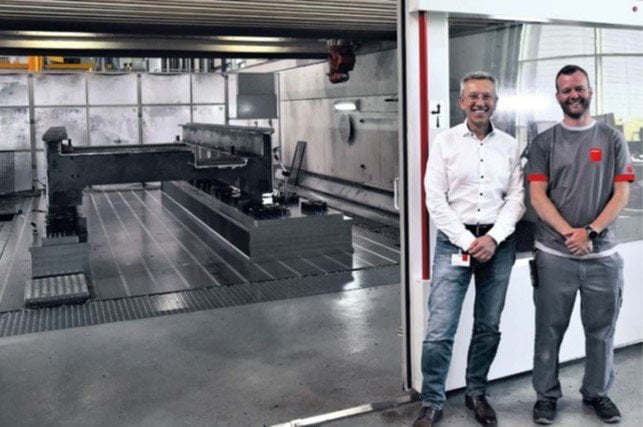
Die Hauptakteure im Projekt waren Uwe Urban, Vertriebsleiter Großmaschinen Deutschland und Raphael Kopp, Leiter der Fertigung bei Bystronic Laser AG. „Mit der MegaMill haben wir einen
„Quantensprung“ bei der Produktivität in unserer Fertigung erzielt“, resümiert Raphael Kopp.
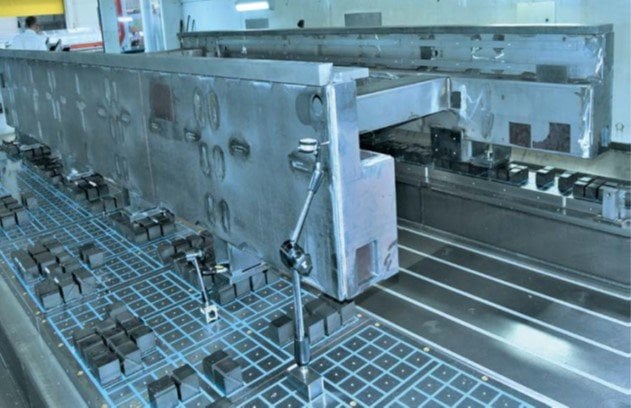
Maschinenrahmen der Laserschneidmaschinen Der Maschinenrahmen einer Laserschneidmaschine wird mit einer Magnetspannung auf dem Tisch gespannt.
Inbetriebnahme mit Hindernissen
Planung des Projekts, mit Beginn im Jahr 2017, Konfiguration der Maschine und anschließend der Bau der Maschine im Werk Emco Mecof in Belforte Monferrato liefen reibungslos.
Aber dann kam die Anlieferung in Niederönz im Herbst 2018: mit 13 LKWs war die Maschine unterwegs zur Aufstellung und Inbetriebnahme in Niederönz. Dann wurde es problematisch,
denn die neue Halle bei Bystronic war zwar geplant aber noch nicht fertiggestellt und die Maschine musste gestellt werden.
Wegen erschwerter Zugänglichkeit wurde ein Teil des Dachs der Halle abgedeckt und die Traverse von ca. 30 t über diese Öffnung auf die Längsträger aufgesetzt. Da war Präzision
gefragt.
Ein Teil der Maschine und das Werkzeugmagazin mit Wechsler standen „ im Freien“. Gemeinsam wurden Lösungen erarbeitet. Um die freistehenden Teile der Maschine wurde eine separate
Umhausung gebaut, damit eine Inbetriebnahme überhaupt möglich war. Dazu kam, dass gerade in dieser Zeit eine Stückzahlsteigerung nötig war, und diese musste quasi im „Notbetrieb“ hochgefahren werden.
Solche Unwägbarkeiten schweißen zusammen!
2-Achs-Universal-Fräskopf arbeitet effizient
Die Bearbeitungsköpfe werden bei Emco Mecof im eigenen Haus gebaut, ein wichtiger Faktor, wenn es um Genauigkeit in der Bearbeitung geht. Auch die Genauigkeit in der Verfahrbewegung der Achsen, beispielsweise das Umkehrspiel gegen Null zu realisieren, ist Emco Mecof eminent wichtig.
Dieser Anspruch der Realisierung maximal möglicher Genauigkeit an der Maschine ist ein Hauptanspruch an die Emco Mecof Maschinen.
Neben einer Vielzahl von Standardköpfen werden häufig innovative kundenspezifische Sonderlösungen realisiert, speziell in den Baureihen der großen Portalmaschinen. In der Megamill-Baureihe sind Bearbeitungsköpfe mit integrierter Rundachse und Schwenkachse motorisch stufenlos
verstell- und regelbar und mit einer Getriebe- oder auch Hochgeschwindigkeitsmotorspindel verfügbar. Durch die intelligente Auslegung der Kopfkonstruktion lässt sich in der Anstellung des Kopfes ein Unterschnitt von 15° realisieren, aber gleichzeitig auch eine horizontale Position ( 0° ),
lageparallel zur Tischfläche. Dies ist von Vorteil, da somit keine Kompensationswege in den Achsen gefahren werden müssen und die Programmerstellung und Postprozessorgenerierung einfacher sind.
Die Bearbeitungsköpfe werden vom zentralen Kühlsystem versorgt, das ebenfalls für Spindel und Torque-Motoren da ist.
Für Bystronic war diese Kopfkinematik „Neuland“. Die Kinematik der bisherigen Maschinen ermöglichte ein Programmieren der Arbeitsprogramme am Bedientableau. An der Megamill mit 2-Achs-Kopf war dies nicht mehr effizient. Zur Erstellung von optimalen Ablaufprogrammen musste ein
CAM-Tool beschafft werden, dessen Implementierung von Emco Mecof tatkräftig unterstützt wurde.
Koordinaten-Transformation, Fräskopfrückzugsabläufe – in all diesen Themen konnte Emco Mecof die jahrelange Kompetenz an den Kunden weitergeben.
Optimierungen für mannlose Bearbeitung im Team umgesetzt
Die Justierung und anschließende Spannung des Maschinenrahmens auf dem Tisch der Maschine wurde bisher herkömmlich von Hand ausgeführt. Das Teil liegt dabei auf Auflageflächen, die auf dem Tisch gepratzt wurden. Ein Ablauf, der zeitaufwändig ist und schon bald bei Bystronic die Idee einer anderen Spannmethodik entstehen ließ. Aus Erfahrungen mit der Magnetspanntechnik, die auch im Betrieb eingesetzt wird, wurde diese Technik auch auf die Spannung der Maschinenrahmen auf der Megamill umgesetzt. Dabei wird das Teil an den Enden vornivelliert, sodass es winklig auf dem Tisch
positioniert ist. Danach wird die Magnetspannung über eineKeilverstellung in den Spannsegmenten an alle Auflagepunkte angefahren und gespannt. Aufwändiges Ausrichten und Spannen von Hand jedes Auflagepunktes entfällt.
Besonders vorteilhaft und zeitsparend ist diese Methodik beim Zwischenlüften der Spannung nach dem Vorschruppen der Kontur, um innere Spannungen im Teil zu eliminieren.
Dies kann jetzt die Steuerung an der Maschine erledigen. Ein Bedienvorgang ist nicht mehr nötig. Dazu hat Emco Mecof ein Ablaufprogramm geschrieben und in der Steuerung hinterlegt, was dann direkt über M-Befehl aufgerufen wird und den Entspannvorgang einleitet.
Die Bedienperson läuft jetzt nicht mehr alle Spannpunkte ab, löst die Pratzen und zieht sie danach wieder mit 200 Nm an, und zwar 2 mal pro Teil. Dies bedeutet, in der mannlosen Schicht ist der Ablauf hochpräzise gewährleistet. Auch für eine Störung durch Bohrerbruch in diesem Zeitraum wurde eine praktikable Lösung gefunden. Die Maschine beendet die aktuelle Bearbeitung, fährt im Pendelbetrieb auf das daneben platzierte, gerüstete Teil und beginnt einen neuen Zyklus. Die Nacharbeit am gestörten Ablauf wird nachfolgend von Hand gemacht, denn hier ist es Bystronic sehr wichtig, dass ein Werkstück korrekt bearbeitet von der Maschine kommt.
„Die sehr gute Kunden-Lieferantenbeziehung, die wir im Projekt aufgebaut haben, konnten wir jetzt bei der Implementierung unserer neuen Idee - die Umstellung des Spannkonzepts auf Magnetspannung - voll nutzen.
Professionell und partnerschaftlich haben wir zusammengearbeitet“. Raphael Kopp ist mit dem jetzigen Ablauf in der Produktion äußerst zufrieden. Seit Februar produziert Bystronic hier Teile mit der magnetischen Spannung und hat damit keine Probleme, aber erhebliche Rüstzeiten eingespart.
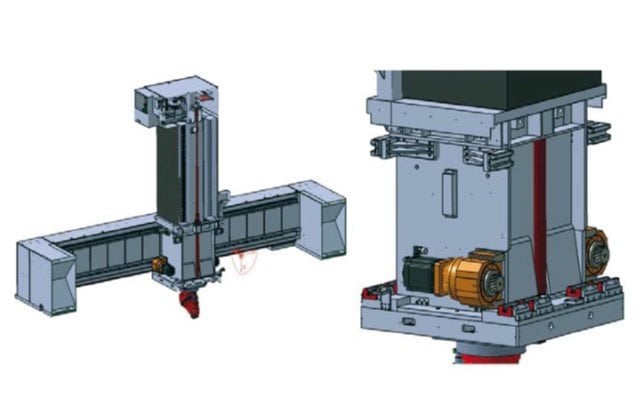
Die Vertikalachse (RAM) ist in der verfahrbaren Quertraverse in einer Box-in-Box Baugruppe gelagert, was maßgeblich zur Erhöhung der Steifigkeit führt
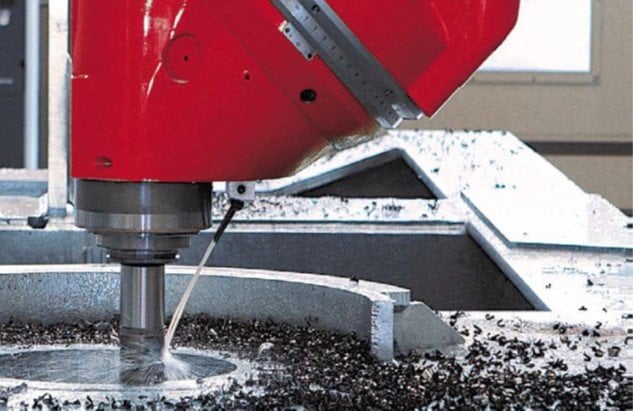
Universalfräskopf mit stufenloser Positionierung, Luft-/Ölschmierung, wassergekühlt, Leistung: 38 kW, Drehmoment: 1000 Nm, Max. Drehzahl: 8000 U/min, HSK 100-A
Die Bystronic Laser AG ist in der Zukunft angekommen
Die Geschäftsleitung, Herr Fabian Furrer, setzt sich stark für die Bystronic-Zukunftsstrategien ein und formuliert es so, „unser Anspruch ist bis 2025 klimaneutral zu sein und komplett auf fossile Energien zu verzichten. Dies erreichen wir, indem Öl-, Gasheizungen abgeschaltet werden und mit
Wärmepumpen gearbeitet wird, deren Strombedarf über PVAnlagen gedeckt wird. Schon heute beziehen wir Strom aus Wasserkraft“.
Die ökologische Verantwortung jedes Einzelnen für eine lebenswerte Umwelt bezieht er auch auf die Notwendigkeit über Einsparungen im Energieverbrauch nachzudenken.
„Wir müssen auch unsere Produkte, beispielsweise die Laser- Schneidanlagen, energietechnisch optimieren, damit auch unser Kunde Einspareffekte erzielen kann“. Die Bystronic hat schon in 2018 im Unternehmen einen neuen Bereich geschaffen, das SOLUTION CENTER, in dem an den Produkten,
in der digitalen Vernetzung des gesamten Produktionssystems im Betrieb des Kunden Lösungen erarbeitet werden. Das Ziel aller Innovationen, die hier entstehen, ist die SMART FACTORY.
„Die Kunden stellen immer häufiger die Anfrage nach einer komplett vernetzten Fertigung, und das müssen wir leisten können“, so die klare Aussage von Fabian Furrer.
Genau die richtige Maschine
Geschäfts- und Fertigungsleitung sind sich nach vier Jahren der Erfahrung in der Fertigung der Maschinenrahmen auf der Megamill einig:
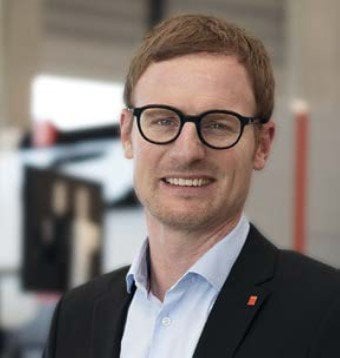
Fabian Furrer, Geschäftsführer in der Bystronic Laser AG “Die MegaMill erfüllt exakt unsere
Anforderungen. Wir sind hochzufrieden“, seine eindeutige Aussage.
„Jetzt nach vier Jahren können wir ganz klar sagen: Die Megamill ist absolut genau die richtige Maschine für unsere Produktion,“so das klare Statement von Fabian Furrer.
Dabei betont er besonders, dass die Anforderungen, die an die Maschine gestellt wurden, voll erfüllt sind und sie auch zukünftig in der Umsetzung ihrer Ideen mit der Maschine sicher sehr gut arbeiten können. Dazu hat er schon konkrete Vorstellungen.
„Wir haben Durchlaufzeiten optimiert, erreichen eine hohe Produktivität und fahren momentan 30-40% mannlos. Aber hier wird es weitergehen und wir werden die mannlose Produktion erweitern. Mit dieser Maschine ist das kein Problem“.
Bystronic Laser AG ist ein weltweit führendes Technologieunternehmen im Bereich Blechbearbeitung, speziell bei Laserschneidsystemen.
/ 3500 Mitarbeiter, weltweit
/ Hauptsitz: Niederönz, Schweiz
/ 40 Standorte
/ Nettoumsatz 2021: 939,3 Mio CHF
/ Produkte: Laserschneidsysteme, Abkantpressen,
Automation, Software, Service
/ Laserschneidmaschine: Herstellzeit: 15 AT /Masch.
/ Maschinenrahmen: Herstellzeit 7 AT / Rahmen
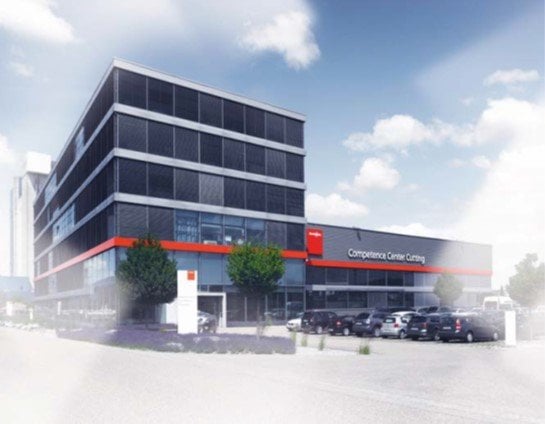
Bystronic Laser AG
Industriestrasse 21 / CH-3362
TECHNISCHE DATEN
Universalfräskopf mit stufenloser Positionierung
Leistung S1 / S6 38 / 57 kW
Drehmoment S1 / S6 1000 / 1550 Nm
Spindeldrehzahlen 15 ÷ 6000 U/min
Option 15 ÷ 8000 U/min
Standard Werkzeugaufnahme "ISO 50 DIN 69871
Option BIG PLUS
Option HSK 100-A DIN 69893"
Elektrospindel 50 / 63 kW
Leistung S1 / S6 50 / 63 kW
Drehmoment S1 / S6 100 / 125 Nm
Spindeldrehzahlen 12000 / 20000 U/min
Werkzeugaufnahme HSK 100-A / HSK 63-A
Elektrospindel 42 / 55 kW
Leistung S1 / S6 42 / 55 kW
Drehmoment S1 / S6 67 / 87.5 Nm
Spindeldrehzahlen 24000 U/min
Werkzeugaufnahme HSK 63-A
Elektrospindel 45 / 58 kW
Leistung S1 / S6 45 / 58 kW
Drehmoment S1 / S6 300 / 372 Nm
Spindeldrehzahlen 12000 U/min
Werkzeugaufnahme HSK 100-A
Elektrospindel 70 / 86 kW
Leistung S1 / S6 70 / 86 kW
Drehmoment S1 / S6 160 / 220 Nm
Spindeldrehzahlen 15000 U/min
Werkzeugaufnahme HSK 100-A
Lineare Achsen
Längsachse Verfahrweg 7500 und mehr (in Schritten von 2500 mm)
Querachse Verfahrweg 4000 - 5000 - 6000 - 7000 mm
Vertikalachse Verfahrweg 1500 – 2000 – 2500 mm
Vorschubgeschwindigkeit 30 m/min
Vertikalschlitten RAM
Querschnitt 550 x 640 mm
CNC-Steuerung
Heidenhain TNC 640 HSCI
Siemens 840D sl
Motorspindel
Standard 40 kW / 1200 Nm
Option 50 kW / 1500 Nm (S1), 61 kW / 1800 Nm (S6)
Werkstück-/Werkzeugkühlsystem
Niederdruck 28 l/min, 6 bar
Hochdruck (durch die Spindel) 20 l/min, 20 / 40 / 60 bar
Standard-Optionen
Kontinuierlicher 5-Achsen Universalfräskopf 6000 U/min
Fräskopf mit ausserachsiger Spindel 3000 U/min
Universalkopf mit Torque-Motoren und Elektrospindel 12000 / 20000 / 24000 U/min
5-Achsen Gabelfräskopf mit Torque-Motoren und
Elektrospindel 12000 / 15000 / 20000 / 24000 U/min
Automatisches Werkzeugmagazin 48 / 64 / 96 / 128 Plätze
Automatisches Kopfmagazin 2 / 3 Plätze
Fordern Sie weitere Informationen an…