www.konstruktion-industrie.com
28
'23
Written on Modified on
Yaskawa: Automation und Digitalisierung dank smarter Vernetzung von Robotern und Motoren
Innovative und wirtschaftliche Lösungen entstehen meist dann, wenn über den Tellerrand hinausgeblickt wird. Beim Automatisieren bedeutet dies oft einzelne Fertigungsschritte zusammenzufassen, sodass Werkstücke mehrere Fertigungsstufen automatisiert durchlaufen.
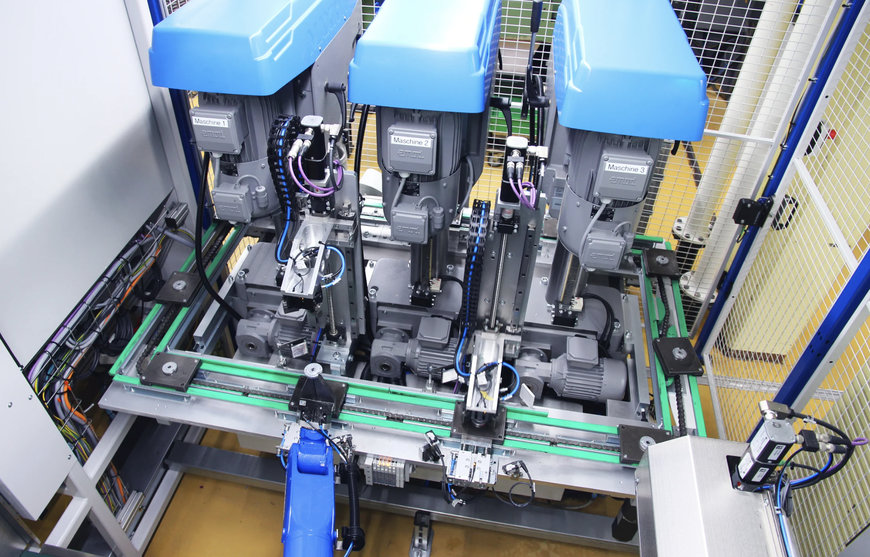
Die smarte Vernetzung der einzelnen Anlagen ermöglicht darüber hinaus eine vorausschauende Wartung, Zustandsüberwachung der Produktionsmittel sowie Kontrolle von Produktionsdaten. Die Integrierbarkeit eines fahrerlosen Transportsystems zur Aufnahme und vollautomatischen Übergabe der Fertigteile in den nächsten Fertigungsschritt komplettiert die zukunftssichere Gesamtlösung.
Aus fünf mach eins - Automation und Digitalisierung dank smarter Vernetzung von Robotern und Motoren
Dunkermotoren, eine Marke von AMETEK mit Sitz in Bonndorf im Schwarzwald entwickelt und produziert seit über 70 Jahren Antriebslösungen bis 5 kW Abgabeleistung. Die modulare Produktstrategie des Herstellers erlaubt es, seine bürstenlosen und bürstenbehafteten DC Motoren mit Getrieben, Gebern, Bremsen und Elektroniken zu einer kompletten Antriebslösung zu kombinieren. Ein Großteil der Antriebskomponenten des 1.300 Mann starken Unternehmens werden am Stammsitz in Bonndorf gefertigt. Intelligente Fertigungslösungen und eine konsequente Automation von Prozessen sind für Dunkermotoren wesentliche Grundlagen für die Wettbewerbsfähigkeit und Qualität der Produkte am internationalen Markt.
Veranschaulichen lässt sich dies an der Automation der Lagerschild-Bearbeitung, welche 2021 durch EGS Automation entwickelt und realisiert wurde. Als Lagerschild wird die vordere Abdeckung eines Elektromotors bezeichnet, aus der die Antriebswelle ragt. EGS Automation aus Donaueschingen beliefert Dunkermotoren bereits seit 2013 mit Roboter- und Automationslösungen. Der Roboterspezialist entwickelt seit 1996 sowohl standardisierte Maschinenbeladesysteme als auch kundenspezifische Sonderlösungen und ist spezialisiert auf die Automation von Fertigungsprozessen in der metallverarbeitenden Industrie.
Der Produktionsprozess im Überblick: Lagerschild-Bearbeitung
Vor der Automation wurden die Lagerschilde bei Dunkermotoren in fünf Arbeitsgängen bearbeitet. Jeder dieser Arbeitsgänge war ein Einzelarbeitsplatz, an dem das Lagerschild in eine Maschine eingelegt und nach dessen Bearbeitung wieder entnommen wurde. Anschließend folgte ein manueller Transport zum nächsten Arbeitsschritt. Der Gesamtprozess war damit „schwer planbar und mit hohem Personalaufwand verbunden“ sagt Mustafa Koyun, Manager Segment GP Production Parts bei Dunkermotoren. Bearbeitet werden zwei Lagerschildgrößen, von denen es in Summe zehn Varianten gibt. Die Bearbeitung umfasst das Einbringen von Bohrungen und Gewinden, sowie die zerspanende Bearbeitung der Innen- und Außenpassung, wo das Lagerschild in das Motorengehäuse verschraubt wird. Je nach Variante muss an dem Zinkdruckgussbauteil ein weiterer Einstich - innen oder außen - gedreht werden. Neben den Befestigungsbohrungen im Lagerschild sowie den Radialbohrungen zum Verschrauben im Gehäuse ist bei einigen Varianten eine letzte Gewindebohrung für die Erdung notwendig.
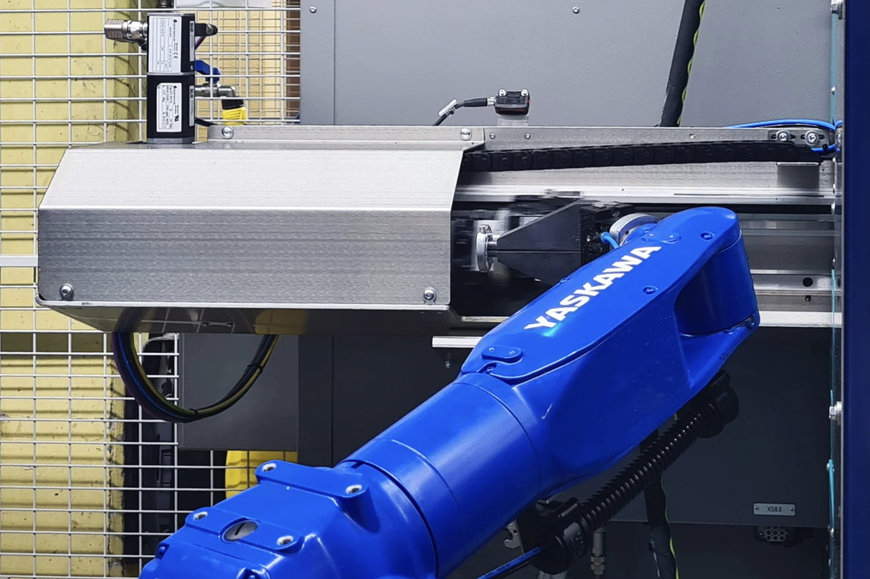
The automation in detail
At the center of the automated machining is an Index ABC lathe, which is advertised by the manufacturer as a dynamic production lathe. Prior to machining, the blanks are present as bulk material in portable mesh containers, where they are poured into a parts hopper by an operator. Via a conveyor system with pre-separation, they enter the detection area of a 3D camera from Keyence, which transmits the position of the blanks and the gripping position to the first robot in the system. This is a six-axis MOTOMAN GP7 from Yaskawa with a reach of around 900 mm and a payload of 7 kg. The radial orientation of the workpieces is also detected by the camera. A pure Bin Picking solution was not implemented, to achieve a maximum process reliability and availability, which is independent of detection difficulties and resulting malfunctions. "A very good decision", comments Koyun. "The system runs reliably and stably, and there are no malfunctions or production interruptions." The performance of Yaskawa robots already convinced Dunkermotoren in earlier production lines, which are still running stably. "Handling and adjusting programs is simple and is no problem even for our operators without robot experience after a short training," Mustafa Koyun admits.
The robot picks up the unsorted parts and transfers them to a transfer system, where they pass three tapping devices on workpiece carriers. Depending on the part variant, threads are inserted at one or more stations. The tapping units can each insert threads with different hole patterns and sizes.
After these processing steps, the workpiece carriers are returned to the first robot via the transfer system. In the transfer system, they are turned and automatically transferred to the transfer shuttle at the input of the index lathe, which feeds them to the machine.
Here, the variant-dependent machining of the total of ten end shield variants is carried out. With retooling, most of the time is spent on the machine. With automation, all that needs to be done is to select a different program and adjust the workpiece carriers of the transfer system and the gripping tools of the robots. "This is done in less than five minutes," says Koyun.
After machining is complete, the second robot, also a MOTOMAN GP7, removes the finished parts and layers them in wash baskets, where they are transported to the cleaning system and cleaned. A changeover station ensures that the baskets can be removed as and when an operator is available without interrupting the automation process. The system is already prepared install a palletizing system from the standard EGS SUMO Ecoplex2 series here at a later date, from which an AGV will pick up the baskets fully automatically and take them to the cleaning system.
The line runs completely autonomously for two to three hours, depending on the variant. The insertion of new blanks and removal of finished parts takes only a few minutes, which has reduced employee involvement to a minimum. Production takes place in two shifts. Due to the low employee commitment, an additional shift to cover short-term production peaks would be possible without any problems. Depending on the variant, the cycle time is between 15 and 35 seconds; the output is thus between 800 and 1,900 parts per shift.
Dunkermotoren Antriebe und EGS Roboter machen die Produktionsanlage IIoT-ready
In der kompletten Anlage sind insgesamt sechs Motoren des Antriebstechnikherstellers selbst verbaut. An den Förderbändern des Zuführsystems, dem Transfersystem sowie den Hubeinheiten für die Teileübergabe verrichten bürstenlose Gleichstrommotoren der Baureihe BG zuverlässig Ihren Dienst.
Die Integration der smarten Motoren legte auch den Grundstein für die Einbindung der Anlage in die digitale Infrastruktur des Unternehmens. Betriebszustände einzelner Fertigungskomponenten, Produktionsdaten sowie Informationen zu erforderlichen Wartungen sollten jederzeit online abrufbar sein. Eine Aufgabe für die IIoT-Spezialisten von nexofox.
Neben der Erfassung und Verarbeitung von kritischen Maschinenparametern sollten Informationen von verbauten Komponenten erfasst und verarbeitet werden können. Aufgrund der verbauten Dunkermotoren konnte nexofox die Anlage selbst sowie die verbauten Motoren digitalisieren.
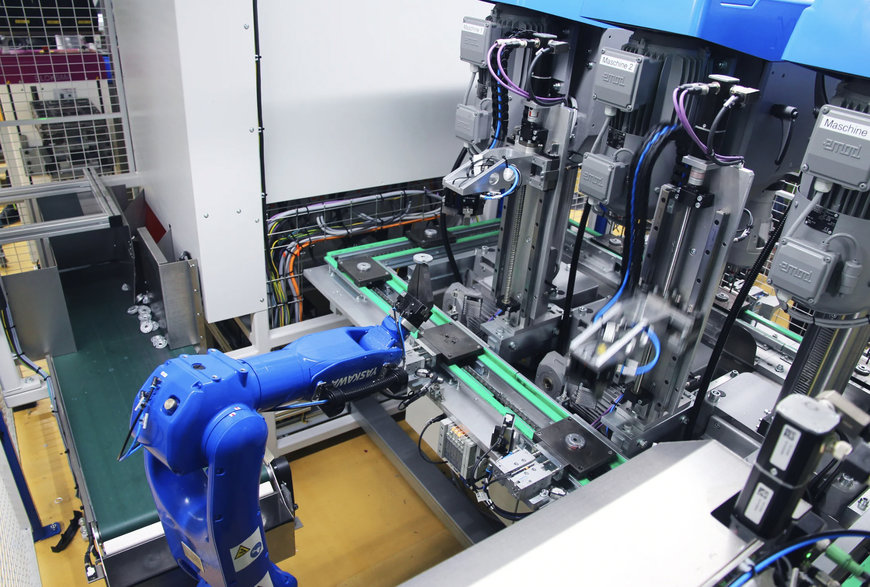
Digitalisierte Lagerschildautomation
Im ersten Schritt wurden zwei MOTOMAN-Roboter von Yaskawa und drei BG Motoren digitalisiert. Alle Komponenten wurden auf der Feldebene mit einem EDGE-Gateway verbunden. Die Motoren wurden über das CAN-Protokoll, die Roboter hingegen via PROFINET angebunden. Das verbaute EGDE-Gateway verbindet die Lagerschildautomation mit der Cloud von Dunkermotoren und ist für die Kommunikation mit dem ERP-System zuständig. Die von nexofox entwickelten digitalen Softwarelösungen wurden dabei sowohl auf der Feld- als auch auf der Cloudebene auf den Standards der Open Industry 4.0 Alliance (OI 4) aufgebaut. Der zugrunde liegende Standard wird in den jeweiligen Asset Administration Shells (AAS) definiert und beschrieben. Eine AAS ist dabei als Referenzmodell zu verstehen, welches Format und Ort der Datenspeicherung definiert, um Informationen später für weitere Assets verwendbar machen zu können.
Die von der OI 4 zur Verfügung gestellte Referenzimplementierung wurde auf der Feldebene und innerhalb der Cloud adaptiert und implementiert. Zuerst werden gewonnene Daten für die Überwachung der Maschine verwendet. Für ein vollumfängliches Condition Monitoring der Anlage werden verschiedene Komponenten-Parameter verwendet und sinnvoll aggregiert. Daraus ergeben sich dann z. B. OEE-Werte oder der Energieverbrauch der Lagerschildautomation. Mit der konsequenten Umsetzung der AAS eröffnete sich nexofox die Möglichkeit, spezifische Parameter, der verbauten Komponenten abzurufen bzw. zu überwachen. So stehen Informationen zu Motorenparametern wie z. B. Phasenstrom, Drehzahl oder Schleppfehler, aber auch wichtige Roboterparameter wie z. B. die Zykluszeit, Bewegungsstunden oder die Temperatur am Manipulator zur Verfügung. Die Auswahl der angezeigten und verwendeten Parameter wurden im Vorfeld der Lagerschildautomation mit Dunkermotoren besprochen und an die Anwendung angepasst. Innerhalb der Cloud wurden alle Parameter der Anlage und der Komponenten visualisiert.
Aufbauend auf dem Condition Monitoring System wurden auf der Cloudebene Drittsysteme integriert. Die Integration in die SAP-Instandhaltungssoftwarelösung gewährleistet z. B. die Weiterverarbeitung der von nexofox bereitgestellten Daten. Der Grundgedanke der einfachen, standardisierten Integrationsfähigkeit wurde in der Cloud weiterverfolgt. Sowohl SAP, ebenfalls Mitglieder der OI 4, als auch nexofox haben die jeweiligen Implementierungsarbeiten auf Basis der AAS umgesetzt, wodurch beide Systeme ohne nennenswerten Aufwand ineinander integriert werden konnten.
Mehrwert dank Digitalisierung
Werden Grenzwerte innerhalb des Condition Monitoringsystem überschritten, wird Dunkermotoren darüber benachrichtigt. Benachrichtigungen werden dabei in für die Produktion nicht kritische Meldungen sowie produktions- oder anlagenkritische Alarme, welche direkt in die SAP-Instandhaltungssoftware durchgegeben werden, unterteilt. Ein Alarm kann beispielsweise durch einen ungewöhnlich schnellen Anstieg der Temperatur am Manipulator ausgelöst werden. Wäre wie hier ein Service Einsatz notwendig, werden die in die SAP Instandhaltungssoftware bereitgestellten Daten an den entsprechenden Servicetechniker weitergegeben. Die von nexofox entwickelte App konnte dank AAS und OI 4 Standards ebenfalls einfach in den Kreislauf integriert werden. Hierdurch wird erreicht, dass sich der Servicetechniker im Einsatzfall optimal vorbereiten kann.
Via QR-Code kann die Anlage identifiziert und dem Servicetechniker die neusten Daten zur Verfügung gestellt werden. Innerhalb der App werden neben Live-Daten auch alle anlagen- und komponentenspezifischen Dokumente bereitgestellt. Nach Abschluss eines Services meldet der Techniker den Einsatz über die nexofox App zurück. Die Information über den Abschluss des Einsatzes inkl. Tätigkeitsbericht, sowie alle Servicedaten wie z. B. Dauer des Einsatzes werden an die SAP-Instandhaltungssoftware zurückgemeldet. Darüber hinaus wird z. B. dem Produktionsplaner gemeldet, dass die Anlage wieder für die Produktion bereitsteht. Der Alarm wird quittiert, steht jedoch in der Alarmhistorie zur Verfügung. So wird die Transparenz erhöht und wiederkehrende Fehler können effizienter identifiziert und schneller behoben werden.
Die erste von nexofox digitalisierte EGS Anlage konnte gleich auf mehreren Ebenen unter Beweis stellen, dass eine auf Standards basierende IIoT-Lösung in weniger als fünf Monaten realisiert werden kann. Zudem zeigt diese Anwendung, dass die Realisierung einer Digitalisierungslösung im Brown Field mit einer Kooperation verschiedener Unternehmen dank einfacher Integrierbarkeit problemlos möglich ist. Dunkermotoren hat durch die Automation der Lagerschild-Bearbeitung seine Effizienz deutlich erhöht und kann sich dank nexofox auch im Störungsfall vollumfänglich auf seine Kernkompetenzen konzentrieren.
www.yaskawa.com
Fordern Sie weitere Informationen an…