www.konstruktion-industrie.com
09
'15
Written on Modified on
Wälzlageroptimierung in der Materialflusstechnik
Regalbediengerät: Neue Radlagereinheiten sparen 58.000 € Betriebskosten pro Jahr
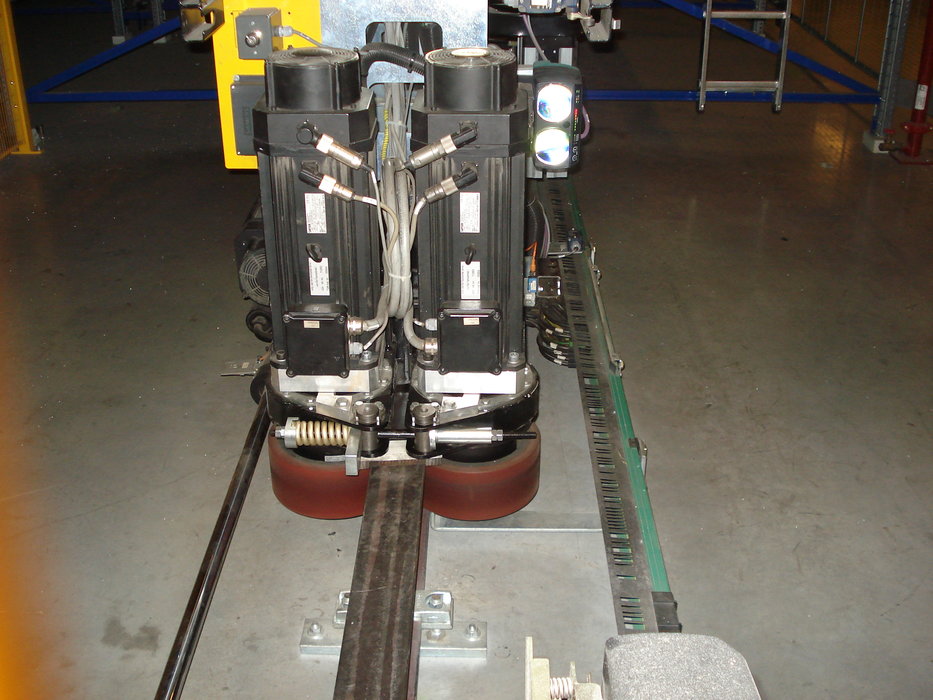
Regalbediengeräte (RBG) in automatisierten Lagersystemen müssen sehr hohe Anforderungen an die Verfügbarkeit erfüllen. Wenn das RBG steht, kommt der Materialfluss zum Stillstand, und die Produktion oder (wenn es sich um ein Fertigwarenlager handelt) die Kunden werden nicht mehr versorgt.
Dieses Problem hatte ein Lagerbetreiber, weil die Radlagereinheiten an den Regalbediengeräten im Zentrallager vorzeitig ausfielen. Insgesamt mussten in fünf Jahren 40 Einheiten ausgetauscht werden, was jedesmal eine unvorhergesehene Betriebsunterbrechung zur Folge hatte.
Experten von NSK analysierten im Rahmen des „Added Value Program“ (AIP) sowohl die defekten Lager als auch die Umgebungsbedingungen der Anwendung. Das Ergebnis: Die Radlager wurden durch Mangelschmierung und durch radiale Vorspannung belastet.
NSK schlug daraufhin die Verwendung vorgeschmierter, abgedichteter zweireihiger Schrägkugellager mit erhöhter Radialluft der Klasse C3 vor. Diese Lager nehmen Radial- und Axialkräfte in beide Richtungen auf. Sie sind mit RSR-Dichtscheiben aus Nitrilkatuschuk ausgestattet, in die eine Stahlscheibe einvul-kanisiert wurde. Diese Dichtungen bieten hervorragenden Schutz vor Verschmutzungen und reduzieren somit den Verschleiß von Laufbahn und Kugeloberfläche. Außerdem verringern sie Vibrationen und die Gefahr von Schmiermittelversagen.
Acht Laufräder wurden probeweise mit diesen Wälzlagern ausgestattet. Im Verlauf von zwölf Monaten kam es zu keinem einzigen Lagerausfall.
Außerdem erstellten die NSK-Ingenieure modifizierte Einbauhinweise und entwickelten ein Montageverfahren für den korrekten Einbau der Radlagereinheiten. Das Servicepersonal des Kunden wurde entsprechend geschult.
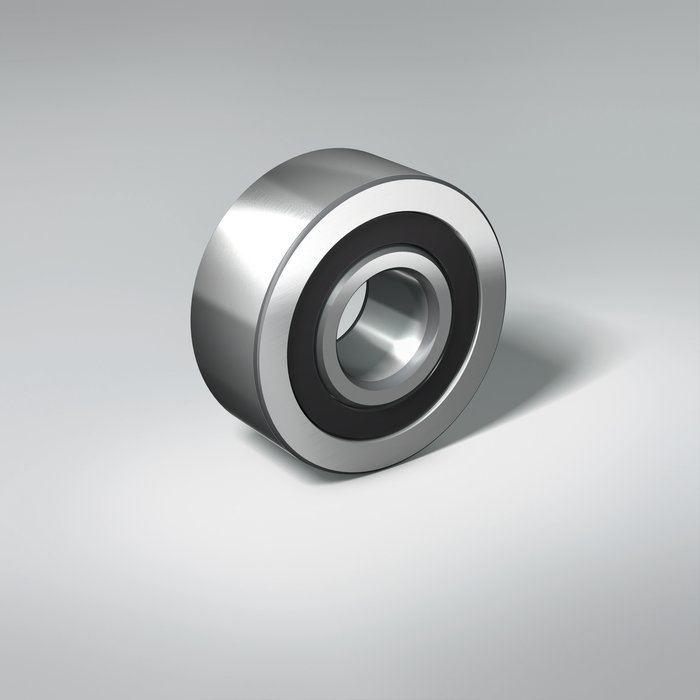
Zu jedem AIP-Projekt gehört eine exakte Kosten-Nutzen-Berechnung. In diesem Fall war die Rechnung einfach: Vor der Optimierung musste der Lagerbetreiber pro Jahr mehr als 70.800 € u.a. für OEM-Ersatzteile (26.880 €), Produktionsverluste (rund 30.000 €) und Reparaturkosten (rd.10.000 €) einkalkulieren. Nach dem Umbau reduzierten sich die Kosten auf 12.700 €, so dass pro Jahr gut 58.000 € eingespart werden.
Fordern Sie weitere Informationen an…