www.konstruktion-industrie.com
15
'24
Written on Modified on
Yamaha: Steigerung des SMT-Durchsatzes durch Einspur- und Doppelspur-Upgrades
Das Wissen um die tatsächlichen Engpässe von SMT-Linien hilft Herstellern, intelligent zu investieren, wenn die Zeit für eine Hochrüstung gekommen ist.
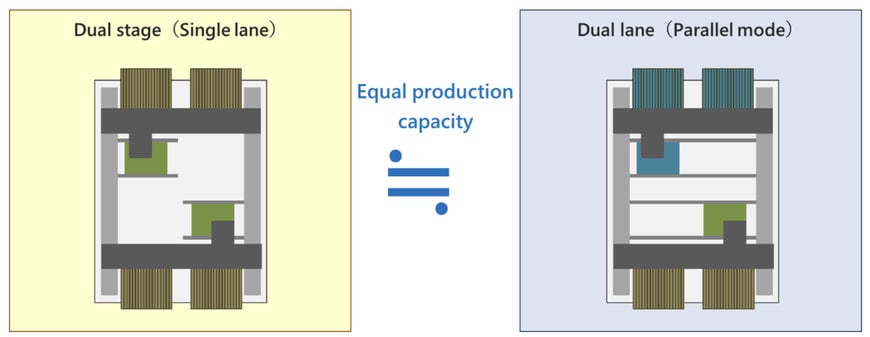
Bei dem Bestreben, die Produktivität zu verbessern, kann jede SMT-Montagelinie einen Engpass aufweisen, der einer Steigerung des Durchsatzes im Wege steht. Ein zusätzlicher Bestücker ist eine offensichtliche Möglichkeit, dieses Problem zu lösen, aber auch eine schnellere Maschine ist eine Option. Andererseits könnte es auch an der Zeit sein, die Linie zu einem Doppelspur-System auszubauen.
Die richtige Entscheidung kann von der typischen Zykluszeit der Baugruppen und der Vielfalt der auf jeder Baugruppe zu platzierenden Bauteile abhängen. Zudem wird die Beseitigung des Engpasses bei der Bestückung mit Sicherheit die Grenzen anderer Komponenten der Linie, wie z. B. des Reflow-Ofens, aufzeigen. Die Reaktion auf diesen unmittelbaren Bedarf an Durchsatzsteigerung sollte daher mit den künftigen Investitionsplänen der Fabrik eng koordiniert werden.
Zusätzlicher Bestücker
Das Einfügen eines weiteren Bestückers in die Linie führt zu einer erhöhten Bestückungskapazität, auch wenn die Steigerung möglicherweise geringer ausfällt als erwartet. Zwei in Reihe angeordnete Bestücker verlängern den effektiven Weg, den jede Baugruppe zurücklegen muss, um den nächsten Bearbeitungsschritt zu erreichen, was die Gesamtverluste beim Baugruppentransfer erhöht. Durch das Einfügen des zusätzlichen Bestückers vergrößert sich auch der Flächenbedarf der Linie um eine weitere Station, was bei begrenzter Produktionsfläche ein Problem darstellen kann.
Doppelspurig produzieren
Für die Steigerung der Linienleistung bei begrenzter Aufstellfläche kann der Wechsel hin zu einer Doppelspur-Linie Vorteile bringen. Mit zwei Spuren, zwei Traversen und zwei Bestückköpfen kann ein Bestücker die Bestückleistung der Linie rein rechnerisch glatt verdoppeln. Im praktischen Betrieb wird der Leistungsgewinn jedoch geringer ausfallen. Außerdem werden zwei Quertransport-Einheiten benötigt: eine für den Baugruppentransfer aus einem einspurigen Drucker in den Doppelspur-Bestücker und eine weitere für den Transfer aus dem Bestücker hin zum einspurigen Reflow-Ofen.
Der Doppelspur-Bestücker kann in zwei verschiedenen Modi betrieben werden. Im Parallelbetrieb werden zwei Baugruppen gleichzeitig geladen und bestückt, wobei die beiden Bestückköpfe unabhängig voneinander arbeiten. Die Transferzeit, um die Baugruppen in den Bestücker zu bringen sowie die für die Bestückung erforderlichen Werkzeuge einzuwechseln, muss bei der Berechnung der Gesamtzykluszeit berücksichtigt werden. Im Parallelbetrieb kann nur jeweils die der Spur zugewandte Feederbank-Seite genutzt werden. Dies kann ein Nachteil sein, wenn Baugruppen mit einer großen Bauteilvielfalt, und damit hohem Feederbedarf, zu bestücken sind.
Der Bestücker kann aber auch im alternierenden Modus betrieben werden. In diesem Fall wird die Baugruppe in einer Spur bestückt, während die zweite Spur den Transport und die Fixierung der nächsten Baugruppe übernimmt. Dadurch wird der Zeitaufwand für den Transport der Baugruppe effektiv auf Null reduziert. Die beiden Köpfe können jedoch nicht ununterbrochen zeitgleich arbeiten, da sie ggf. aufeinander warten müssen, um eine Kollision sicher zu verhindern.
Leistungsvergleiche
Da die typische Transferzeit für eine Baugruppe in der Regel zwei bis drei Sekunden beträgt, kann mit dem alternierenden Modus eine kürzere Zykluszeit erreicht werden, wenn nur eine geringe Anzahl von Bauteilen je Baugruppe bestückt werden muss. Hier wirkt sich die Zeitersparnis beim Baugruppentransfer am stärksten auf die Reduzierung der Gesamtzykluszeit aus.
Mit zunehmender Zahl zu bestückender Bauteile beansprucht auch der Zeitaufwand für deren Platzierung einen größeren Anteil an der Gesamtzykluszeit. Infolgedessen verringert sich der Vorteil durch die Einsparung von Transferzeit im alternierenden Modus. Sobald die Zykluszeit mehr als 15 Sekunden beträgt, überwiegen in der Praxis die Verluste, die im alternierenden Modus anfallen, während einer der beiden Köpfe nicht arbeitet, um Kollisionen zwischen den Köpfen zu vermeiden. Die Einsparungen, die durch den Wegfall der Baugruppentransferzeit erzielt werden, spielen dann eine untergeordnete Rolle. Wenn dies der Fall ist, kann der Parallelbetrieb eine höhere Produktivität bieten, vorausgesetzt, der Zugriff auf die benötigten Feeder ist gegeben.
Der andere Ansatz
Trotz der potenziellen Geschwindigkeitsverbesserung in beiden Modi ist ein doppelspuriger Bestücker nicht unbedingt die beste Lösung für eine ansonsten einspurige Linie. In der Praxis wird die Produktionskapazität des Bestückers nicht durch die Anzahl der Spuren, sondern durch die Auslastung der Bestückköpfe bestimmt. Die höchstmögliche Produktivität wird dann erzielt, wenn die Bestückköpfe während eines möglichst großen Anteils der Zykluszeit aktiv sind.
So kann ein einspuriger, zweistufiger Bestücker mit zwei Bestückköpfen die gleiche theoretische Kapazität haben wie eine doppelspurige Maschine im Parallelbetrieb (Bild 1), wobei auch der Zugang zu den vorderen und hinteren Feedern möglich ist.
Die Zeitverluste durch den Baugruppentransport beinhalten die Zeit für die Aufteilung der Baugruppen auf zwei Spuren, die innerhalb des Bestückers erfolgt. Andererseits wird kein Quertransport benötigt, um Leiterplatten aus dem Drucker zu übernehmen. Die Wartezeit zur Vermeidung von Kopfkollisionen ist gleich null, und die kompakte Stellfläche, die einem einspurigen Bestücker entspricht, sorgt dafür, dass der Gesamtverfahrweg für das Aufnehmen und Bestücken von Bauteilen sehr kurz ist.
Wenn keine besonderen Anforderungen an die Art der zu bestückenden Baugruppen gestellt werden, kann ein zweistufiger, zweiköpfiger Bestücker die Produktivität effektiver steigern als die Einführung eines Doppelspurbestückers oder zweier herkömmlicher Einspurmaschinen.
Den Flaschenhals verstehen
Wenn die Bestückung von Bauteilen die Leistung der Linie begrenzt, ist eine Erhöhung der Montagekapazität die geeignete Maßnahme. Wenn jedoch ein anderer Teilprozess den Engpass verursacht, kann die Erhöhung der Bestückleistung eine vergeudete Investition sein. Zur Veranschaulichung illustriert Bild 2 eine SMT-Linie mit Angabe der einzelnen Prozesszykluszeiten. Hier ist der erste Bestücker tatsächlich der Engpass, der die Zykluszeit der Linie (40 Sekunden) bestimmt.
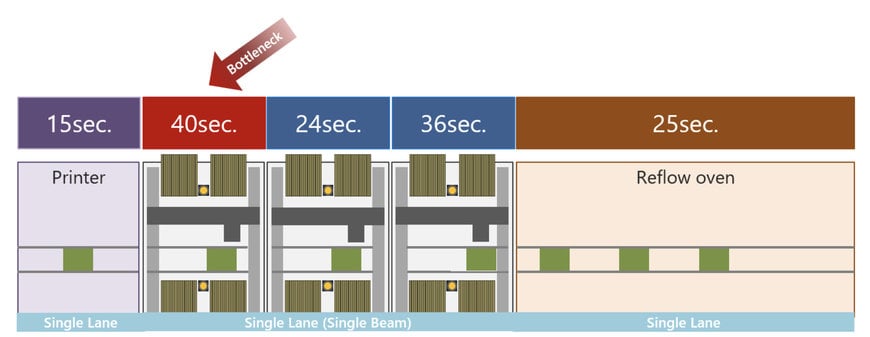
Der erste Bestücker begrenzt die Leistung der gesamten Linie
Wartezeiten der Bestücker vermeiden
Im Beispiel von Bild 3 wurde durch die Umstellung auf eine einspurige, zweistufige Bestückung die Bestückungszeit verkürzt. Der Reflow-Lötprozess bestimmt nun die Taktzeit der Linie. Diese Zeit kann nicht verkürzt werden, da das Reflow-Profil eine feste Zeitdauer hat. Im Bild benötigt jeder Bestücker deutlich weniger Zeit als die durch das Reflow-Verfahren vorgegebene Zykluszeit und befindet sich mehrere Sekunden pro Zyklus im Wartezustand. Die Investition in die Bestückgeschwindigkeit ist praktisch wirkungslos.
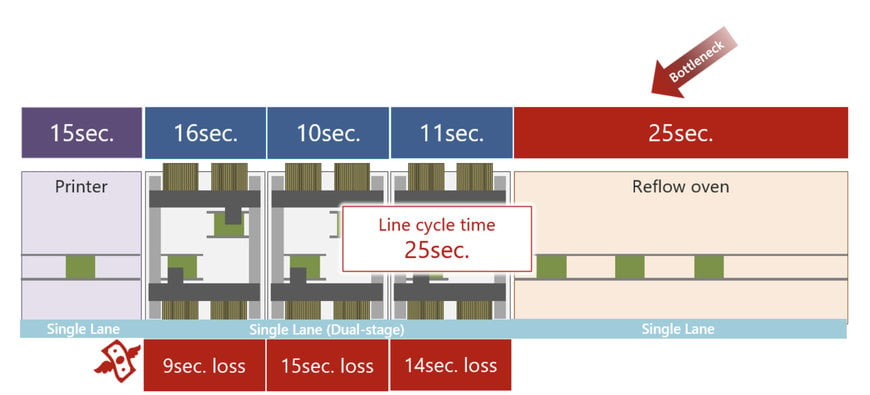
Der Reflow-Prozess definiert die Zykluszeit der SMT-Linie
Eine Zykluszeit von 25 Sekunden ist für das Reflow-Löten durchaus typisch. Wenn die Bestücker in der Linie schneller sind, ist der Reflow-Prozess der Flaschenhals.
Die Hochrüstung des Lötprozesses durch einen Doppelspur-Reflow-Ofen verkürzt die Löt-Zykluszeit auf 12,5 Sekunden (siehe Bild 4). In diesem Fall können doppelspurige Bestücker effizient mit dem Reflow-Ofen verbunden werden. Zwischen dem einspurigen Drucker und dem doppelspurigen Bestücker ist ein Quertransport erforderlich.
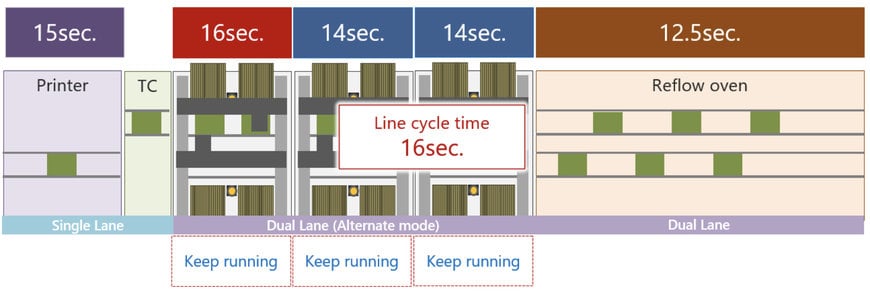
Kurze Zykluszeiten durch doppelspuriges Bestücken und Reflow-Löten Alle Bestückköpfe werden vollständig genutzt.
Der am längsten dauernde Bestückprozess bestimmt die Gesamtzykluszeit der Linie. Obwohl dieser Bestücker die Linienleistung effektiv begrenzt, ist die Zykluszeit im Vergleich zum Beispiel aus Bild 1 deutlich verbessert und alle Bestückköpfe sind voll ausgelastet. Hier hat sich also die Investition in die Bestückleistung gelohnt.
Ein zweistufiger Einspur-Bestücker, wie in Bild 3 dargestellt, kann Baugruppen mit Hilfe eines Quertransports an den doppelspurigen Reflow-Prozess übergeben und ermöglicht außerdem eine kürzere Zykluszeit als ein doppelspuriger Aufbau. Die zweistufige Maschine bietet auch die Möglichkeit, auf einen einstufigen Betrieb zurückzugehen, um kleinere Baugruppen zu bestücken, die eine kürzere Zykluszeit haben. Ein Software-Werkzeug wie Yamahas Line Optimizer kann automatisch die effektivsten Parameterwerte errechnen und anwenden. Die Tabelle fasst die typischen Optionen für SMT-Führungskräfte zusammen, die die Zykluszeit ihrer Anlagen verkürzen möchten.
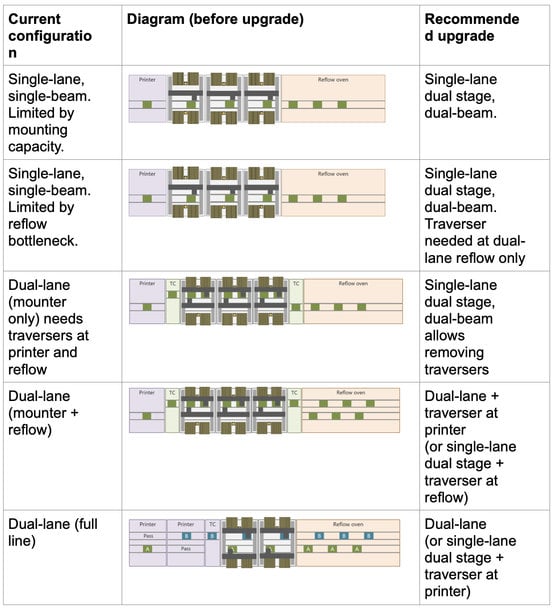
Konfigurationen zur Verbesserung der Zykluszeit
Fazit
Jede SMT-Linie enthält einen Flaschenhals. Wenn die Zeit zum Aufrüsten gekommen ist, ist die genaue Kenntnis des Flaschenhalses von entscheidender Bedeutung, um die Investitionen an der richtigen Stelle tätigen zu können. Wenn der Bestückungszyklus lang ist, wäre eine zweistufige Bestückung eine gute Option. Ist er jedoch kurz, könnte die Investition in einen doppelspurigen Reflow-Prozess effektiver sein.
Die Einführung einer Doppelspur-Automatisierung in einer einspurigen Linie ist kein einfaches Unterfangen und geht mit Kompromissen beim Durchsatz und der Verfügbarkeit der Feeder einher. Wenn die Produktionsfläche begrenzt ist und andere Einspur-Maschinen bleiben sollen, kann ein zweistufiger Einspur-Bestücker eine praktische und kostengünstige Produktivitätssteigerung ermöglichen.
www.yamaha-motor-robotics.com
Fordern Sie weitere Informationen an…